Engineering Innovation: The Master Key to Unlock the Door to Deep Space
Articles | 29-04-2015 | By Paul Whytock
Mouser Electronics teamed up with celebrity engineer Grant Imahara and experts in the space industry to launch an exciting new Space Exploration Series and Space Challenge that puts engineers in space. The educational program is part of the Empowering Innovation Together initiative.
Right now, 2,271 satellites are whirling around this planet, and whereas they represent an already astronomic engineering and financial investment in space technology, they are, in fact, only a beginning that has merely scratched the surface of the cosmic infinity that surrounds planet Earth.
Technology that will allow further exploration into the deeper reaches of the universe will make massive demands on engineering skills and innovation and require a substantial financial investment.
Watch Glenn Smith, CEO of Mouser Electronics (left) and celebrity engineer Grant Imahara (right), and other experts give their views and predictions on how innovative engineering and leading-edge electronics will continue to push back the boundaries of space exploration.
But space is not a friendly place for delicate silicon circuits
As astrophysicist Carl Sagan once said: “The universe is not required to be in perfect harmony with human ambition.”
Key amongst the technology hurdles that have to be cleared are extremes of temperatures, radiation levels that can severely damage both on-board electronics and astronauts alike, efficient power management systems and an overall spacecraft design that can cope with the rigours of long explorations whilst not being unaffordably heavy to launch.
Radiation levels and extreme temperature fluctuations are the harsh elements that stress electronics components and systems in space. Future innovations will have to not only conquer these problems but will also have to be innovated in such a way that not only are the complex challenges dealt with, but the solutions also add to the efficiency of space vehicles rather than detract from them.
For example, spacecraft operating in the cold environment of deep space carry a large number of radioisotope heating units to maintain the surrounding temperature of the on-board electronics at approximately 20 °C. These thermal strategies impinge on development costs and increase weight.
Electronics capable of operation at extreme temperatures without heating system support are a particularly crucial innovation, and one very promising breakthrough is silicon-germanium electronics. This technology has been shown to function reliably through a +120 to -180 Celsius temperature range, and it is also highly resistant to various types of space radiation.
Just how extreme can space temperatures get?
The surface temperatures of Mars show extreme fluctuations with equatorial midday highs of +20 Celcius but lows of -150 Celcius at polar locations. Saturn gets even chillier with temperatures as low as -175 Celcius.
But it’s not all about extreme cold. Heat can cause severe problems for electronic components, and the space environment adds its own peculiar problem when it comes to thermal dissipation; there is no air to dissipate heat to. So all heat needs to be dissipated via conduction and radiation. With temperature control strategies in place, the next major operational threat is solar radiation. Electronics technology has already made some progress with rad-hardening techniques that combat the possibly catastrophic infiltration of radiation.
Hazards range from when a stray particle of energy passes through a circuit in the spacecraft’s computer, causing a glitch and possibly corrupting data, to extreme solar flares that can destroy spacecraft electronics.
Radiation hardening chip designs tend to rely on a belt and braces approach of system duplication or sometimes quadruplication, where each functionality is quadrupled to guarantee system back-up.
Insulated substrates are preferred for space chips, and prime amongst these are Silicon on Insulator and Sapphire on Insulator.
Bipolar ICs generally have higher radiation tolerance than CMOS circuits, and Magnetoresistive RAM (MRAM) is thought to provide radiation-hardened, rewritable, non-volatile conductor memory. DRAM is usually replaced by more durable SRAM circuitry, and Gallium Nitride, with all its established processing performance advantages, also provides a high resistance to radiation issues.
Protecting astronauts from space radiation
So engineering innovation is gradually taking care of radiation threatened components, but what about the humans on-board?
Radiation health hazards are well documented, from cataracts of the eye to weakening bone and muscle structures to cancer. As yet, there are no conclusive engineering strategies that would protect astronauts during lengthy deep space exploration.
So ingenuity and innovation are very much required in this area. Radiation exposure causes ionisations in cells. At low doses, cells repair themselves very quickly. At higher doses, the cells may not be able to repair themselves, and galactic cosmic rays create a continuous radiation dose throughout the Solar System.
Material shielding can be effective against such rays, but again there could be a functionality problem here because of the amount needed and the weight created and subsequent blast off effort required to heave it all into space.
Several active shielding methods have been considered that might be less massive than passive shielding; magnetic shielding generated by superconductors could be a future innovation. But there are design challenges relating to the human tolerance of such a system. Magnetic fields up ten times higher than those in hospital MRI machines would be needed, and these levels could cause significant health reactions among astronauts.
Of course, none of these works without power, and the effects of a power system malfunction in space were well illustrated by the film Apollo 13, where limited power caused loss of cabin heat, shortage of drinking water and the jeopardising of the craft’s carbon dioxide removal system.
So all these technical challenges that space exploration represents offer the world of electronics exciting design challenges and potentially substantial commercial rewards, both of which are meat and drink to adventurous and innovative companies.
But why should we earthlings be so keen to explore planets in our solar system?
Mars is currently the planet getting all the technological attention, and there are plenty of justifiable reasons.
Here’s just one of them, deuterium.
There are vast amounts of this heavy isotope of hydrogen on Mars. On Earth, it occurs as 166 out of every million hydrogen atoms but comprises 833 out of every million hydrogen atoms on Mars. Why is that so important? Deuterium is the key fuel for fusion reactors, and it is hugely expensive, about €8,000 per kilo. Mars may hold the key to trillions of Euros of deuterium supply.
So space is the greatest adventure that can potentially offer untold rewards yet poses massive engineering challenges.
To offer its own inspirational technical support, global electronics distributor Mouser Electronics has teamed up with celebrity engineer Grant Imahara and a variety of experts in the commercial space industry to present a new Space Exploration Series and Space Challenge that puts engineers in space.
The educational program is part of the Empowering Innovation Together initiative. Engineers will have an opportunity to learn about the new space race to colonise Mars, MoonMail, the world’s first commercial lunar delivery service, the hostile environment in deep space and creating a personal lunar legacy.
This Space Exploration Series is only available on Mouser.com.
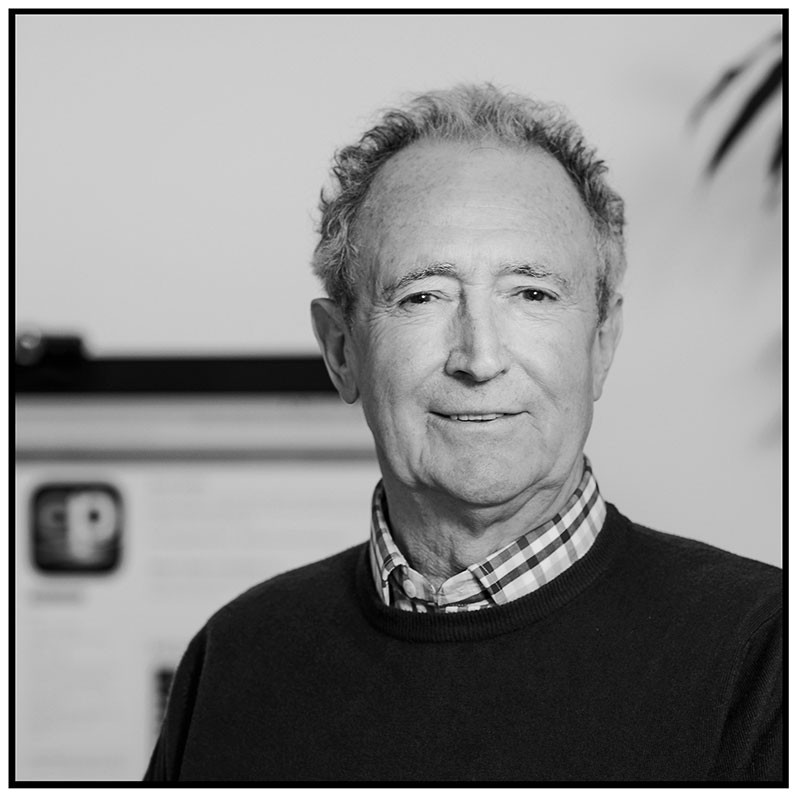