'Smart factory' - the key to Industrial Revolution 4.0
02-07-2018 | By Nnamdi Anyadike
The fourth industrial revolution is fast becoming a reality in many parts of the developed world. And as this revolution comes into being, manufacturing is being transformed with a move to fully ‘smart’ or intelligent factories and the evolution of smarter products. Definitions of what constitute both the fourth industrial revolution and the ‘smart factory’ differ slightly.
But there is general agreement that the fourth industrial revolution is one that will connect the virtual online world with the physical one within the industrial world and connect the Internet of Things (IoT) to the production line. And as part of that development, smart factories will increasingly need to ‘self-optimise’ their performance, learn from new conditions and autonomously run entire production processes.
According to Deloitte Consulting, “Simply put, a smart factory is one equipped with technology that enables machine-to-machine (M2M) and machine-to-human (M2H) communication in tandem with analytical and cognitive technologies so that decisions are made correctly and on time.”
The smart factory represents not just a leap forward from the more traditional automation to a fully connected and flexible system. But as Deloitte notes, “Far from being an ‘end state,’ the smart factory is an evolving solution—one that taps into multiple features such as agility, connectedness, and transparency.”
What has made the realisation of the smart factory possible today is the rapid development of technological capabilities. AI, cognitive computing, and machine learning are all coming together now to enable systems to interpret, adjust to, and learn from the data gathered from connected machines. And technology and systems vendors are responding by creating new products in partnership with manufacturers, who are increasingly making investments in smart factory capabilities to mitigate the risk associated with possible future labour shortages.
Limtronik GmbH, the supplier of Electronic Manufacturing Services (EMS) uses intelligent 3D X-ray inspection system sourced from GOEPEL Electronic, a leading supplier of inspection equipment, on three of its surface-mount device (SMD) lines. An AXI system (automatic X-ray inspection) was first integrated by GOEPEL Electronic on Limtronik’s lines in 2010 to check the quality of soldered connections. At the time, it was one of the first systems to enable full-area 3D X-ray imaging.
In May, Limtronik introduced an update from GOEPEL. As a result, one hundred percent solder joint control is now possible. Information about the line can be accessed via tablet, allowing for the system to be monitored and controlled from a remote workstation. And in addition to the complete results of an inspection, machine statuses and operating times can also be transmitted.
The Michigan, US based electronics contract manufacturer and printed circuit board (PCB) assembly provider Saline Lectronics, has also fully embraced the smart factory concept. It has designed its production floor and manufacturing processes to be intuitive, intelligent, and connected. Saline claims that its facility provides, “advanced traceability and real-time data of your electronic assembly.”
One innovation is its ‘Lectronics Luigi.’ Much like the current crop of smart speakers or digital assistants in the home, like Amazon’s Alexa and Google Home, Lectronics Luigi is Saline’s very own conversational AI for the factory. “Access to Luigi will be through mobile devices as well as on the factory floor, and we believe that Luigi will also be talking to our vendors and customers,” says a company white paper. Saline envisions a day when “Alexa and Luigi meet”, allowing the weather to be checked with ‘Alexa’ in the morning and the overnight factory performance with ‘Luigi.’
Meanwhile, Samsung Electronics Co. Ltd at the recent IoT World 2018 in Santa Clara, California showcased its ARTIK IoT solutions by demonstrating how smart factories, intelligent buildings and asset managers can achieve meaningful return of investment through its solution. “ARTIK untangles the common complexities of IoT deployments with a full range of turn-key partner IoT solutions that provide flexibility and efficiency, so organizations can remain focused on how they can best provide tangible returns to their customers’ bottom line,” said James Stansberry, senior vice president and general manager of ARTIK IoT at Samsung Electronics.
Companies like Hipaax, a provider for mobile workforce management solutions, have combined ARTIK cloud services with other solutions such as Shoreline IoT’s iCast Asset Monitoring Solution to increase production line efficiency. Other new partners announcing ARTIK-enabled Solutions include: SL Corporation; ForgeRock; Gambit Communications and Dizmo.
There are though pitfalls that stand in the way of a move towards smart production. One clear danger is cyber security. This is because by its very nature, the smart factory is ‘connected’. This leaves a smart factory vulnerable to a cyber attack in a way that would not be possible in a traditional manufacturing facility. This risk is enhanced as the smart factory moves beyond the four walls of the factory to include suppliers, customers, and other manufacturing facilities.
That said the shift away from linear, sequential supply chain operations both within and outside of the plant towards an interconnected, open system of supply operations is now all but inevitable. And the smart factory combined with the digital supply network is already busy laying the foundation for how companies compete in the future.
Read More: Can ARM-based Thin Clients Provide a Secure Alternative to Windows Desktops?
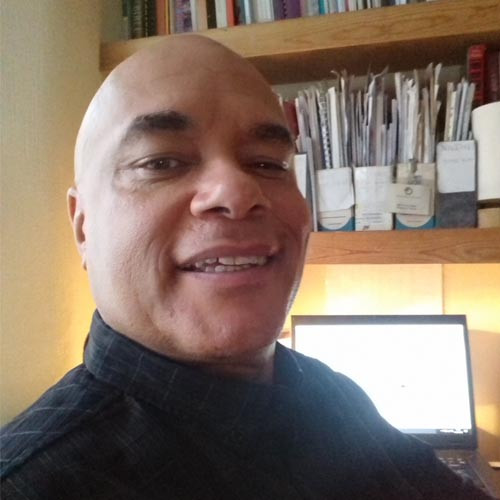