Batten & Allen Providing Power Module Lead Frame Manufacture from Start to Finish
12-01-2021 | By Robin Mitchell
Lead frames are one of the foundations behind electronic components and ensuring their reliability and quality is essential for any component. Who are Batten & Allen, what services do they offer, and why should they be your next choice when designing a power component?
What is a Lead Frame and why are they critical in electronics?
Of all industries that exist today, one that has had the biggest impact on modern life is the electronics industry. Anyone involved with electronics design understands that high-quality electronics are essential to the development of reliable products. Engineers also understand that all aspects of every component must be of high-quality, not just the functional part of a component (i.e. the silicon die or material that provides the component with its functional properties).
Lead frames are the metal structures that hold semiconductor dies in place, provide mechanical strengthening, and connect the semiconductor to the outside world. During the final stages of manufacture, the semiconductor die is glued to the lead frame, bond wires attached between the die and the lead frame pin pads. Then, the lead frame with the bonded die is encapsulated into a plastic or ceramic package.
The need for high-quality lead frames is essential for producing reliable semiconductor products for many reasons. Firstly, lead frames are responsible for electrically connecting the semiconductor die to the outside world. If the lead frame's material quality is poor (i.e. oxidised and high resistance), then the performance of the final component will be hindered (resistance will increase the operating temperature whereas poor quality surfaces can result in poor connections).
Secondly, lead frames provide mechanical security to the attached die, and by extension, the chip itself. If the lead frame manufacturer cannot provide proper mechanical protection, then the resulting components will either be limited in application (i.e. cannot be used in automotive or industrial applications) or will be too unreliable.
Thirdly, poor quality frames built from inferior materials could cause manufacturing issues for semiconductor foundries. Brittle materials could result in cracking of the metal, while materials that are too soft can create sharp edges when pressed and bent. Simultaneously, some materials may not be able to handle bending and thus result in broken pins.
Who are Batten & Allen?
Batten & Allen are a company that specialises in stamping, plating, and assembly for the electronics industry. Founded in 1972, the UK company has provided the electronics industry with nearly 50 years of high-quality frames and connectors. As of 2020, Batten & Allen have over 100 staff with a high proportion of staff retention (50% of staff being employed by B&A for over 10 years, and 30% being employed for over 20 years).
One major standard that Batten & Allen contributed to the development of was the PCB edge connector; the technology that has been at the heart of computers and other expandable devices for the past 30 years.
While Batten & Allen provide stamping and lead frame plating material services for customers, they are also producers of lead frames, including SIL, DIL, SMD, and stacked capacitors. Furthermore, Batten & Allen also provide speciality connectors such as Z clips, bespoke lead frames, and bespoke parts (such as contact switch spring plates).
Batten & Allen Supporting Power Module Development
One area of electronics that is becoming popular is the use of power modules, and factors such as high-efficiency and high-quality are of utmost importance. The pressure for high-quality parts is further compounded with the demands from the automotive, medical, and industrial sectors, which can see wide temperature swings, mechanical vibrations, and extreme reliability requirements.
Batten & Allen have recently announced that they will be combining their expertise in the lead frame plating process and lead frame industries to provide power module customers with a complete turn-key service to ensure their products' success.
Batten & Allen provide a wide range of different plating and surface options, including exotic copper alloys not commonly seen in the industry during the initial stage. At the same time, Batten & Allen can provide quantities as low as 1 and as high as 1,000, allowing engineers to evaluate and prototype different packaging technologies before moving onto design validation.
The design validation stage is where Batten & Allen can step up production rates in quantities from 1,000 to 50,000, which allows customers to prove their designs and get their designs ready for pre-production. This stage is where customers can identify hidden faults, and Batten & Allen services will allow designers to make last-minute changes.
Once the design is verified and ready to go into production, Batten & Allen can provide customers with leading manufacturing methods and technologies in the tooling stamping, and plating processes. Furthermore, Batten & Allen can also provide design advice on ESD compliant packaging, a critical factor when designing in the lead frame manufacturing process.
Why choose Batten & Allen?
Ordering lead frames is only one small step to the design and development of a product. Batten & Allen go one step further, ensuring the highest quality products and working closely with customers to ensure that they have the product they need.
Batten & Allen have years of experience in the field of lead frames and plating processes. They are also certified to ISO19001, IATF16949, and ISO14001. This means that every stage of development is managed properly, and a strict set of quality management practices ensures that the final products are to the highest standards.
Having a company take care of its customers to the extent which Batten & Allen go not only saves money, it also saves time. Batten & Allen's standards ensure that the final product conforms to the most stringent standards (such as RoHS and REACH), are applicable to the designated environments, and will provide reliability for the many years of service that the final product will be operating for.
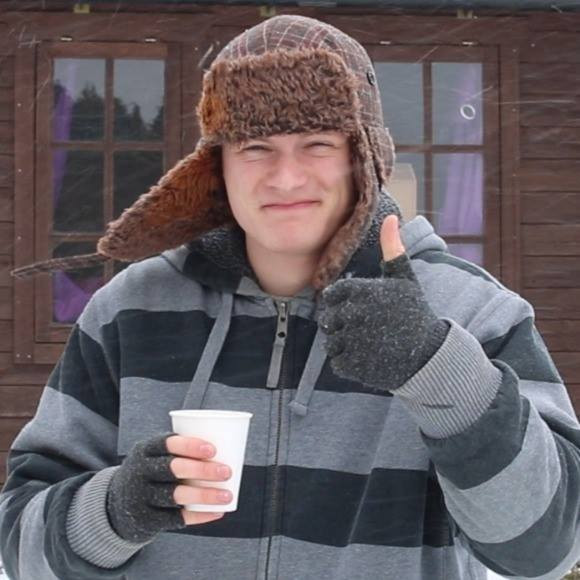