First, 3D printed flexible OLED could help lower flexible OLED prices
| 11-01-2022 | By Robin Mitchell
Recently, researchers have created a small flexible OLED display entirely made using 3D printed processes. What challenges do flexible OLED displays present, what did the researchers demonstrate, and how could it help reduce prices in the future?
What challenges do flexible OLED displays present?
Display technology has come unbelievably far since the invention of the first CRT screen. What used to require hundreds of watts of power and many kilograms of supporting equipment has been shrunk down into displays measuring a few grams with higher resolutions, improved brightness, and increased refresh rates.
Despite the many incredible achievements made in display technologies, consumers continue to demand more from their products, and one area of growing interest is flexible displays. Flexible displays are already integrated into consumer electronics, such as smartphones, and can expand in size of the product. For example, a smartphone with a flexible display can start off at the same size as a typical smartphone but then open up like a book and effectively double the screen size.
But creating flexible displays comes with a range of challenges, and these challenges make them extraordinarily expensive. The first challenge is finding materials with semiconductive properties that can flex, and traditional semiconductors cannot do this as they are crystalline in structure, so organic semiconductors are used. Even then, every display component has to be flexible, including contacts, wires, and the substrate.
The second challenge is developing manufacturing processes that can create flexible displays reliably. Unlike traditional parts, which are made up of discrete solid objects that can easily be placed and manipulated, flexible parts can present difficulty as they can be structurally unstable. This means that parts may flex and move around during the manufacturing process. Many organic semiconductors are produced using thin films and chemical deposition stages which are not cheap to do.
The third challenge is longevity and reliability. For a flexible display to be practical, it must withstand many flex cycles without losing performance. This was one of the biggest challenges faced by researchers in the early days of flexible display technologies, as most early displays would fail after being folded a few times. It is clear that researchers have found solutions, but this has come at a substantial monetary cost to the final display.
Researchers create flexible OLED display using a 3D printer
Recently, researchers from the University of Minnesota have successfully demonstrated a small flexible OLED display produced entirely using a single 3D printer. The new display is built up in layers, and the use of an XY gantry system allows for the placement of material exactly where it is needed.
All parts of the printed display were done at room temperature, including the light-emitting layer, and all layers of the display were done using the same machine. The printed layers include the electrodes, the interconnects, insulation, and encapsulation which produces a completely functional device with no additional steps needed.
The final display has a resolution of 8 x 8 pixels with a total pixel count of 64. While this may be trivial compared to modern displays, it must be appreciated that the entire display was created using a 3D printer with no additional manufacturing steps, all at room temperature. Furthermore, the display was demonstrated to be fully operational, and the display was able to produce a consistent display even after 2,000 bending cycles.
How could 3D printed displays help with future fabrication?
While the ability to create a 3D printed display sounds promising, it must be understood that 3D printers are extremely slow in operation, and trying to get one to print a 1080 display would take an enormous amount of time (assuming that the printing head delivers individual drops). The significance of the development is not so much that it uses a 3D printer as it is that the process was completed in a typical lab at room temperature.
Modern, flexible OLEDs have to be produced in state-of-the-art facilities that often cost hundreds of millions to build (depending on the size and nature of fabricated parts). The use of such facilities increases the final price of flexible OLED displays, and eliminating this would allow displays to be made in standard factories with controlled environments.
But if this technology could be transferred into an inkjet printing system, the ability to create large displays at speed may be possible. If created, an inkjet display fabricator would dramatically help bring the price of flexible OLED displays down while simultaneously demonstrating new uses for inkjet technologies.
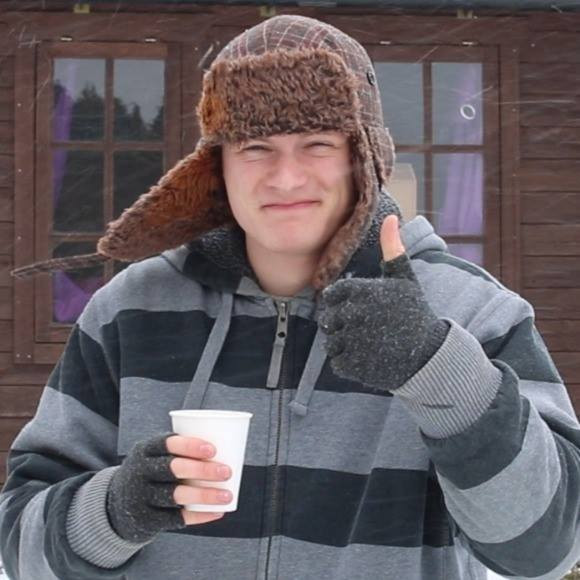