Cheap manufacturing method developed for wearable sensors
Wearables | 01-03-2022 | By Robin Mitchell
Recently, researchers have been able to replace photolithography with a $200 vinyl cutter to significantly reduce the cost of wearable sensors. What challenges do wearable sensors face regarding the manufacture, what did the researchers demonstrate, and how could wearable sensors be constructed in the future?
What challenges do wearable sensors face?
Trying to create wearable electronics comes with a whole range of issues, and almost all of these challenges come from the fact that electronics, by nature, are ridged. For example, wearable electronics that are directly attached to the skin need to be able to flex and move so that they are comfortable and reliable, but electronic devices are unable to flex and stretch.
Worn electronics need to breathe and allow the skin to sweat and cool, but the ridged nature of electronics also sees them entirely opaque (both to light and moisture). This means that worn electronics can become uncomfortable to wear, cause problems with moisture build-up, and may even introduce complications in the form of skin build-up and adverse skin reactions.
To try and solve this, engineers can use one of two methods for creating wearable electronics. The first is to create electronics that are flexible from the ground up, and this generally involves polymers and organic compounds. Great strides have been made in this field of study, and some researchers have even developed fully flexible ARM microcontrollers that can be bent and deformed while still operating. But such electronics are costly and primitive with limited capabilities.
Another solution is to use an “island bridge” design that involves tiny electronics circuits built using standard manufacturing practices and then connecting these circuits over a flexible substrate. While the individual electronics circuits cannot be flexed, their small size means that they can go unnoticed when worn. The use of a flexible substrate to interconnect islands allows for most of the design to flex. However, this presents challenges in creating reliable electronics that can withstand a flexible substrate, and the design can be complex.
Both solutions are also faced with challenges in manufacturing. One manufacturing process that is commonly used, photolithography, is a highly specialised method that requires the use of cleanrooms. This drives up the cost of producing flexible devices and can make prototypes extremely expensive. Thus, flexible electronics continue to be held back due to the expensive manufacturing processes needed, and getting quick designs produced is not possible without a large amount of funding.
Researchers develop methods for making wearable sensors with cheap equipment
Recently, researchers from UC Berkley have demonstrated a new manufacturing technique for creating wearable sensors without the need for expensive processes such as lithography. Instead, designs utilising the island bridge method can be manufactured with off-the-shelf vinyl cutters that cost around $200. The resulting product is about 90% cheaper than using expensive high-tech processes.
To create the substrate, the researchers used an adhesive sheet of polyethene terephthalate (PET) and a Mylar sheet. The desired island pattern is cut into this layer using two cutting depths, the island cut and the through cut, and this is used to create isolated islands for sensors and circuits. After these cutting stages, the sheet is then coated with gold, and the PET layer is peeled away. The result is a flexible substrate with gold wires that can be connected to islands. Furthermore, the vinyl cutter can cut the gold layer to create sensors, resistors, and capacitors.
What does this mean for wearable electronics of the future?
Developing flexible electronics using complex organic compounds and advanced flexible semiconductors would be the key to long-term wearable electronics. However, the use of flexible substrates with integrated circuit dies integrated into islands is not only more practical for the meantime but can take advantage of modern semiconductor technologies.
For example, the die for a 32-bit microcontroller could readily be integrated into a small PCB whose contacts are then connected to a flexible substrate. This would create a truly wearable device with the power of a modern 32-bit microcontroller. The use of a cheap vinyl cutter also helps to significantly reduce the barriers to entry for smaller research teams looking to create wearable electronics.
Researchers are constantly advancing new techniques and discoveries that often fissile into nothing, whether because a better technique is developed or because what was discovered is not practical. However, what the researchers have demonstrated here shows real promise as anything that can reduce the cost of manufacturing helps bring commercialisation closer to reality.
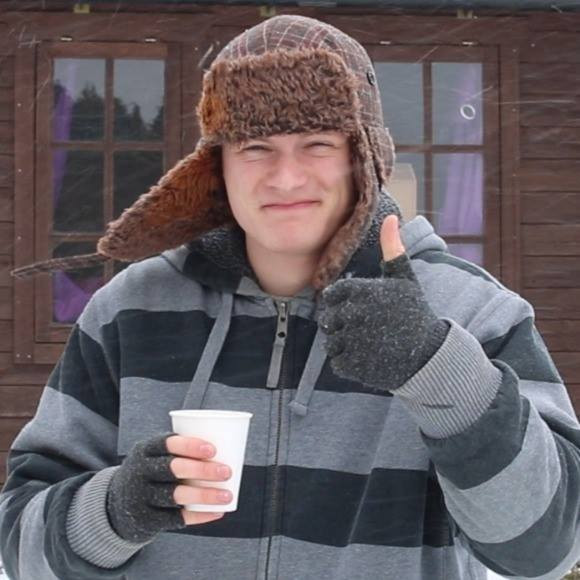