3D printed bone grafts to be approved for patients in Europe
19-07-2022 | By Robin Mitchell
Recently, European regulatory bodies have allowed custom 3D printed bone grafts to be used for medical procedures. What challenges do implants present, what does the 3D printing technology do, and how does this help to lower the cost of medical procedures and equipment?
What challenges do implants present?
Unlike many environments faced by engineers, living tissue is one of the most difficult to design for. Not only is living tissue slimy, always moving, and organic, but it also reacts to the presence of foreign bodies. For example, a wooden splinter left in the body will trigger an immune response whereby white blood cells try to pack themselves around the splinter in an effort to destroy it (i.e. the formation of puss). This barrier also helps to prevent bacteria from the foreign object from getting into the bloodstream, and increased blood supply to the area helps to provide more nutrients and white blood cells.
However, the body is imperfect, and if the immune response to a foreign object is too great, sepsis can form. When this happens, the overreaction to the foreign object can result in widespread inflammation, and this, in turn, can cause organ failure. Sepsis is more likely to occur if the body fails to remove the foreign object, which is why deep cuts containing dangerous bacteria can be particularly troublesome.
Of course, the foreign body doesn’t just mean bacteria or viruses; anything that is not supposed to be inside the body can be marked as a foreign body. As such, anything implanted into the human body must be biologically inert. A material is considered biologically inert if living tissues don’t detect its presence (for example, unreactive materials such as titanium and glass are considered biologically inert).
But even if the enclosure to a part is biologically inert, additional design considerations also must be taken into account. For example, it is essential that any battery technology used is chemically safe inside the body. Imagine a scenario where a lithium-ion battery implanted into the body ruptures and starts to produce hydrogen gas; it would be nothing short of a nightmare.
Engineers must also consider the procedure for implanting and how long the device is expected to be implanted for. The human body may have the ability to heal itself, but repeated surgical procedures introduce secondary-infection risks, scar tissue, and other complications.
3D printed bone grafts to be allowed in medical procedures
Recently, European medical authorities have announced that 3D-printed bone grafts can be used for medical purposes. While the use of bone grafts will not be available overnight, the introduction of these parts will be over a two-year process to ensure that real-world results follow the result of successful trials.
Specifically, bone grafts manufactured using a special material developed by the company Cerhum that has been given the green light. Their material can directly replace damaged bone by providing a porous structure for blood vessels to grow. Of course, the material cannot be used as an outright bone replacement as bone marrow is essential for producing red blood cells, but portions of bone that need removal can use the new bone grafts. For example, facial deformities caused by surgical procedures or from growth can be removed by surgeons and then reconstructed using the new material.
The material, called MyBone, is made from a patented blend of compounds, including calcium phosphate, that helps to mimic natural bone. The use of 3D printing allows for complex porous structures to be printed, something that cannot be done using mainstream production methods without high cost.
How does MyBone demonstrate the advantages of 3D printing in the medical field?
Anything custom-made is always expensive as anything customised cannot be manufactured using low-cost, high-volume production methods. As such, custom medical implants can become extraordinarily expensive and usually require specialists to make accurate models for each individual use case.
The introduction of 3D printing and advanced scanning techniques allows medical specialists to create new designs in CAD from patient scans, manufacture prototypes in hours, and then use medical-grade printers to create implants. The entire process can be shrunk down to a matter of hours, and not only does this drive the cost down, but the use of printer technologies also helps doctors design parts not currently practical. For example, the MyBone material allows for the creation of hollow structures that blood vessels can grow into, which is difficult to achieve with current manufacturing processes targeted at custom parts.
If technology in the field of 3D printing technologies continues to advance, it may not be long before researchers can print organs and thus eliminate the need for donors. Furthermore, these organs and other bodily parts could be manufactured at significantly lower costs and would even remove the risk of rejection.
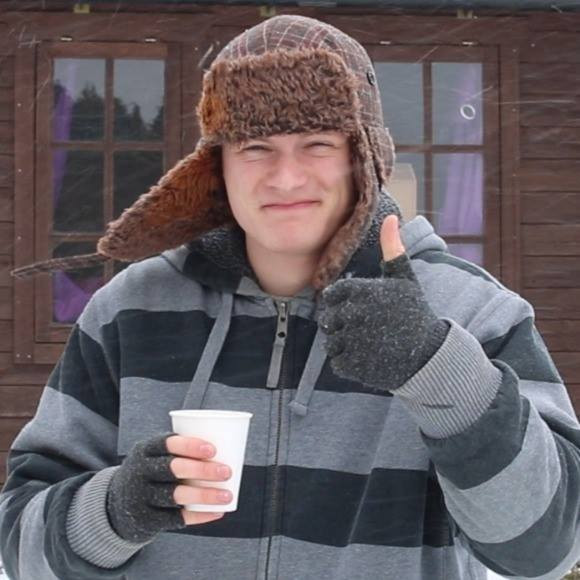