Researchers Create Flexible Temperature Sensor Array Capable Of Creating Thermal Maps
| 05-09-2022 | By Robin Mitchell
Recently, researchers have demonstrated a temperature array that can be adhered to other surfaces and be used to generate heat maps. What challenges do typical thermal sensing solutions present, what did the researchers develop, and how could it help engineers in the future?
What challenges do typical thermal sensing solutions present?
Thermal sensors are arguably one of the most common found in electronic devices, and the reason for this may come down to the simplicity in thermal sensing. For example, a thermal couple is a combination of two different materials that, when placed in contact, will generate a voltage depending on the temperature. Such thermal couples are extremely easy to manufacture and, as such, are cheap to integrate.
An even simpler option is to use a comparator with a pair of matched transistors with two separate constant current sources. With each transistor being matched, some basic logarithmic maths will create a relationship between the two temperatures that is entirely dependent on the temperature, and this is commonly used in microcontrollers.
Despite the ease of manufacturing temperature sensors, they come with numerous challenges. One such challenge is that temperature sensors are highly localised, meaning they record the temperature exactly where they are. While this isn’t an issue when determining the temperature of a microcontroller, it does introduce difficulties in measuring the temperature of an area.
For example, identifying a hotspot in a design can be useful for determining short circuits or potential damage. A design with twenty thermal couples dotted around can provide localised data, but trying to read each sensor requires numerous analog lines, all of which have to be routed to a central controller.
One option is to use an IR camera that can observe the entire design. However, accurate IR cameras are typically very expensive, and those with high frame rates face strict controls due to their potential military use. At the same time, such a camera is heavy, bulky, and requires to be positioned away from the main design. As such, IR cameras are good for debugging in workbenches but cannot be used for general observation during normal operation.
Researchers develop flexible thermal sensing matrix
Recognising the challenges current thermal sensors face, researchers recently demonstrated a thermal sensing device that is integrated into a flexible substrate. One demonstration of the thermal sensor showed a matrix of 10x10 thermal couples to give a total of 100 sensors, and their array configuration allows for the entire sensor to be controlled with just 20 control lines (10 row selects and 10 column selects). Powering the demonstration with a Raspberry Pi, two ADG706 multiplexers, and a SparkFun LCA HX711 load cell, the researchers showed how their flexible sensor array can be used to generate heat maps of the area in contact with the substrate.
To create the sensor, the researchers combined a pair of PET substrates with silver conductive traces that then sandwich a layer of PEDOT:PSS. The resulting combination creates temperature junctions that can be individually selected for reading. At the same time, the use of PET substrate provides flexibility which also presents potential applications in body-worn sensors and other wearables.
Furthermore, the researchers created additional sensors to demonstrate the variability in the overall sensor size and density. One example showed a sensor with a total area of just 1cm2 and a total sensor count of 441 (21x21).
Using the sensors, the researchers were able to demonstrate generated heat maps after exposure to heat in specific areas. The resulting heat maps not only show changes in heat but how that heat moves through the array in real-time.
How can temperature arrays help engineers in the future?
One major application for such sensors is monitoring heat distribution in a design, whether it’s a PCB, battery pack, or engine case. The ability to see hotspots allows engineers to isolate potential areas of concern while simultaneously allowing engineers to understand how heat moves throughout their design. At the same time, such a thermal sensor can track all areas for changes in heat, allowing all aspects of a design to be monitored (not just specific areas with integrated thermal couples).
Another potential application for such thermal matrix sensors is health monitoring in patients. While the human maintains a stable core temperature, injuries, infections, and diseases can see changes in heat distribution throughout the human body. For example, an infected cut will often see greater blood flow (a typical immune system response) and, therefore, is warmer than the surrounding tissue. If attached to key areas on a patient, doctors can track localised temperature to understand areas of concern (such as the return of an infection).
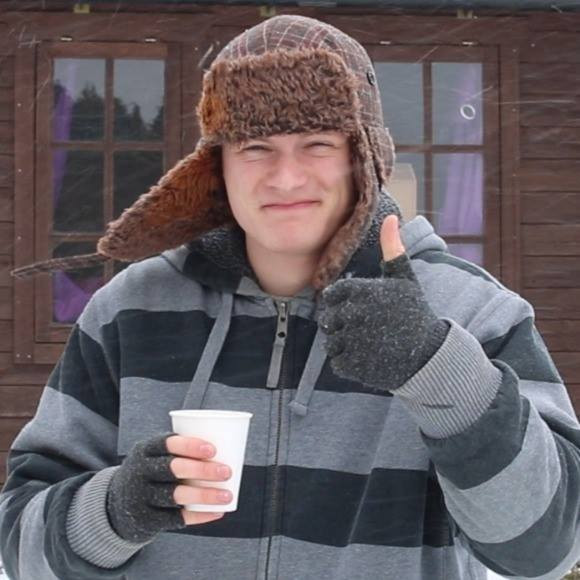