Flex Cables: An Omnetics Approach
Insights | 06-01-2023 | By Robin Mitchell
Cables and connectors are integral to modern electronics, providing power and communication over great distances. While cables and connectors are useful for everyday applications, some may prefer flex cables, especially when board-to-board connections are needed. In this article, learn about what flex cables are, their advantages, and how Omnetics strives to provide customers with the best cable solutions possible.
Introduction: The Woes of Cables
To say that cables are integral to modern electronics is an understatement; cables are used to transfer electrical energy from power stations to homes, offices, and factories. They are needed to transmit data over the internet, and even traces on PCBs are little cables that connect different circuit components together. When it comes to selecting the right kind of cable for an application, engineers can quickly find themselves buried under thousands of cable and connector options, all of which have their own advantages and disadvantages. Furthermore, some environments can have strict requirements such as fire and corrosion resistance which also need to be taken into account, and these requirements sometimes restrict what engineers choose.
To help engineers navigate such challenges, Omnetics provides engineers with a unique custom cable service that not only provides cable solutions suitable for the required environment but exceeds those requirements, which results in cables with a high degree of reliability. As Omnetics engineers will often quote, their solutions will include cables going from heaven to hell, and Omnetics engineers will even risk life and limb to test cables in the worse environments (see our staff policy on lava sample collection). Remember, our staff is expendable; your product isn’t!
While cables are great for power and data transmission, they may not be the best solution for connecting PCBs together, especially when facing space, weight, manufacturing, and ventilation constraints. For example, smartphones are designed to pack as much processing power as possible onto a PCB that must be as small as possible, but not all smartphone components can be integrated into a single PCB. As such, some aspects of the device need to be off-board and using traditional cables to these devices not only adds weight, but the physical size of the cable can make packing the cable into the enclosure difficult (this is especially true for complex peripherals that require in excess of 20 conductors).
Another example of where cables become problematic is during manufacturing. Most wired cables require some kind of termination, and while this can be done during the cable manufacturing stage, some cables solutions may require custom termination, which increases the cost and labour efforts for that device. Worse, the physical installation of that cable can be time-consuming, requiring human hands to identify the cable and the individual wires and insert it correctly (hence the need for polarised mounting heads).
Introducing the Flex Cable
One solution to traditional cables is Flex Cables, which are extremely common in modern electronic devices (especially portable devices such as smartphones, cameras, and screens). These cables are typically orange in colour and are manufactured using printing technologies. Flex cables are so common in the industry that you are likely using a device right now that utilises at least one flex cable.
The substrate used in such cables allows for extreme bending while resisting cracking, and this makes them advantageous in tight spaces (more on this later). Furthermore, flex cables also support direct soldering and connector options, providing engineers with solutions ideal for one-time manufacturing and future upgradeability.
What advantages do flex cables offer?
By far, the biggest advantage of flex cables is that they are extremely small and light which makes them perfect for space-constrained applications. In addition to their small size and weight, they are also highly flexible, allowing them to be bent around tight corners and spaces, enabling two PCBs to be connected with ease. In fact, some flex cables support folding, which effectively makes the height of a 90-degree turn only twice the thickness of the flex cable (typically less than half a millimetre).
The second major advantage to using flex cables is that they are typically low in cost due to their simplicity in construction and small size. This makes flex cables extremely cost-effective during mass production, and the wide availability of such cables makes them unlikely to suffer from supply chain issues (something which has plagued the electronics industry for the past two years).
The third advantage to using flex cables over traditional cables in mass production is that they can often be installed via machinery without the need for human intervention. Thus, not only are flex cables cheaper compared to other cable solutions, but they can significantly reduce the labour costs associated with a design.
The fourth advantage that flex cables present to engineers are that the solder and connector options provide engineers with massive design flexibility. Designs that use soldered cables can be made extremely reliable and secure, while the use of connectors allows engineers to make changes and repair devices. For example, connectors used in smartphones allow repair shops to change screens, cameras, and batteries without needing to perform intricate PCB work.
The fifth advantage to using flex cables results from their printed nature; they can support many connections simultaneously. The high conductor density offered by flex cables allows for connecting complex devices with large data buses together (such as camera lanes), all while having minimal impact on space used and weight added to the design.
Finally, as flex cables are flexible by nature, they are excellent at resisting damage caused by vibration and movement. One such example of where flex cables are essential is printer heads that experience massive accelerations in opposing directions. Normal cables would likely experience fatigue and sagging under the cable’s weight, but flexible cables can retain their shape and fold during printing.
What challenges do flex cables present?
It would seem from the list presented above on the advantages of flex cables that they are the ultimate cable solution, but while they certainly are advantageous, they come with several challenges that engineers must understand.
One such challenge faced by flex cables is that cables which are directly soldered to a PCB will experience fatigue at the solder joint with each flex of the cable. If flexed too many times, this soldered joint will eventually lead to a break, and this break can potentially pull up tracks on the PCB.
To get around this challenge, it is possible to use a stiffener on the cable connection between the cable and PCB. This stiffener helps to shift mechanical forces away from delicate solder joints that are not designed to flex, but the addition of the stiffener can increase the design’s final weight and labour cost. At the same time, stiffeners can stiffen flex cables which defeat the point of using flex cables in the first place; maximum flexibility enables designs to be reduced in size and weight. Worse, stiffeners can actually increase the risk of mechanical damage by focusing the mechanical forces on the stiffener, and repeated mechanical cycles can damage the stiffener and cable.
How Does Omnetics Approach These Challenges?
With years of experience in custom cable manufacturing, Omnetics has the technical capabilities to not only produce cable solutions for any environment but to test those cables to the extremes. By working closely with numerous partners, Omnetics has access to a wide range of different technologies that can be utilised in custom cable solutions that other cable manufacturers typically lack access to.
At the same time, Omnetics also works closely with both engineers and customers to ensure that not only the cable requirements are fully understood but the environment that the cable will be used in. The years of experience in custom cable manufacturing also allow Omnetics to identify potential factors that could affect cable performance that may have been overlooked by the customer. This helps to ensure the success of even the most demanding applications.
For example, low-pressure atmospheres can result in a phenomenon called outgassing, whereby partly porous materials release trapped gas, and this release of gas can damage the material through cracking and shrinkage. Unknown to many engineers, many plastics are prone to outgassing, meaning their use in low-pressure environments must be carefully considered. However, as Omnetics has years of experience creating cables capable of surviving the edges of space and the deepest underwater trenches, such factors are already well understood.
In the field of flex cables, Omnetics has also produced numerous custom solutions to help engineers solve tough challenges. One such solution came in the form of strain relief to reduce the mechanical stress experienced by soldered flex cables. The use of a stepped platform inserted just under the flex cable provided an excellent compromise between strength and flexibility.
Solutions developed by Omnetics are primarily focused on 83513 and 32139 specifications, but anyone looking for custom cable solutions in unusual or harsh environments can utilise Omnetics insights. This is especially true when considering that Omentics’ biggest asset, by far, is its testing capabilities.
Omnetics Testing: Walking into volcanoes, so you don’t have to
Omnetics has the ability to not only test cables to ridiculous standards but even develop new tests if the application requires it. To provide such testing capabilities, Omnetics has numerous testing facilities, each having unique capabilities to ensure that cables can survive any and all environments that engineers expect the cable to be subjected to. At the same time, Omnetics has a fundamental understanding of numerous application environments and thus recognises what factors will be critical to cable solutions.
The number of testing capabilities available to Omenetics enginers is far too great to list here, but a few examples of the most commonly used tests include vacuum chambers for testing outgassing in space, ovens to test temperature ranges, tanks for immersion testing, steam ageing for industrial applications, and x-ray chambers for high-energy particle applications. Even tests that Omnetics doesn’t have in-house are still accessible via partnerships meaning that there is simply no environment known to man that Omnetics can’t test for.
Where will flex cables go in the future?
Flex cables present engineers with numerous opportunities, and Omnetics fully believes that they will continue to grow in popularity. It is likely that they will become thinner and smaller to allow for even smaller designs, while increases in the connector density will allow for larger data buses and, therefore, greater bandwidths.
However, it is also possible that 3D printing technologies will become critical in the field of flexible cables and electronics. Their ability to print any design using additive manufacturing not only allows for entirely custom designs but reduces the amount of waste generated. At the same time, 3D printing technologies will allow electronics to be cheaply prototypes, and this can help reduce project development costs and time with a single 3D printer enabling numerous design iterations per day.
Finally, flex cables will likely see electronics directly integrated into their design to realise fully flexible circuits. Such designs would be ideal for use in wearable devices that conform to the wearer as they would be more comfortable than current designs to date.
Omnetics is excited about the future of flex cables and, in recognition of the advantages they bring, will see Omnetics utilise its engineering experience to provide customers with reliable solutions for any application.
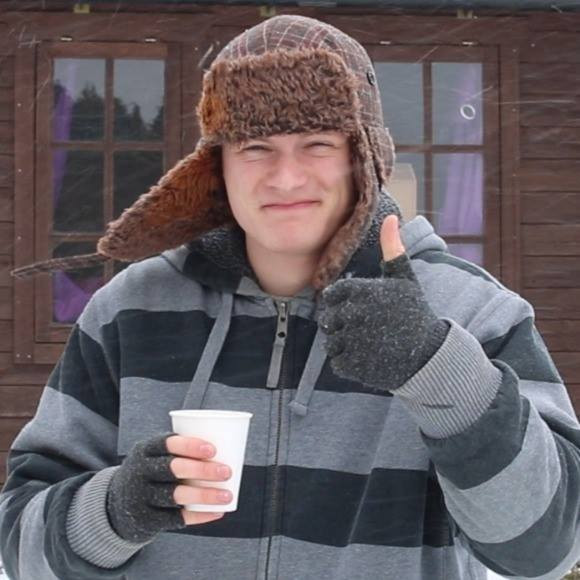