Metallic Gel: The Game-Changer in 3D Printing and Electronics
Insights | 11-07-2023 | By Robin Mitchell
In a groundbreaking development that could revolutionize the world of manufacturing and electronics, researchers have unveiled a novel metallic gel with the extraordinary ability to be 3D printed into solid objects at room temperature. This development could potentially overcome some of the most significant challenges currently faced in 3D printing, particularly those associated with metallic parts. This article delves into these challenges, explores the researchers' innovative solutions, and discusses the potential implications of this metallic gel in the electronics industry.
In this article, we ask, what challenges does 3D printing face concerning metallic parts, what did the researchers demonstrate, and how could it be used in the field of electronics?
What challenges does 3D printing face with regard to metallic parts?
Of all manufacturing technologies that have existed over the past 50 years, none have been more transformative than 3D printing. Of course, manufacturing processes such as injection moulding and vacuum forming have powered mass production (and therefore are crucial) but the ability of 3D printing to allow engineers to rapidly develop, test, and redesign ideas has changed how engineers prototype concepts.
Instead of designing a part and waiting several days for it to be manufactured, it can be printed in a matter of hours at a fraction of the cost. If the parts are found unsuitable, design changes can be made in software, sent back to the printer, and new parts printed. In fact, for small parts, a design can go through multiple iterations in a single day.
But for all the benefits that 3D printing presents, the technology is still in its infancy, and there are numerous challenges faced by engineers, especially when concerning those made from metal. Plastic parts are generally ready to be used as soon as they are printed, but those made from metal almost always require some secondary process.
Due to metal’s high melting point, 3D-printed metal parts are generally made from metal powder that is sintered together via a laser beam. Even though the finished part has some strength, it is by far nowhere near as strong as it could be (often being possible to crumble in one’s hand).
To fix this issue, 3D-printed metallic parts are generally placed into a furnace for heat treatment. The heat of the furnace is not enough to melt the part entirely but enough to cause fusing between the individual metallic grains, thereby creating a solid structure.
However, such furnaces are not easy to maintain, nor are they suitable for use in domestic and office environments. As such, 3D metal printing is generally reserved for engineers with large budgets and development environments capable of operating industrial equipment. Furthermore, the expensive nature of metallic powders also means that not all engineering projects can afford to go through several design iterations in metal.
Another challenge faced with 3D metal parts is consistency in characteristics. A solid metal part casted or machined has extremely predictable characteristics due to the uniformity in the grain and structure of the metal stock used to make it (i.e., melted metal poured and cooled is atomically strong with extremely well-documented characteristics and predictable behaviour).
As such, simulations can readily be done on metal parts in software that can accurately predict tensile strength and the distribution of force throughout the part. By contrast, 3D-printed parts using metallic powders do not have the same characteristics or uniformity, and variations between prints can result in unpredictable characteristics. This means that while 3D-printed metal parts are great for prototyping, they are unsuitable for mass production, especially in safety-critical applications.
But, if 3D metal printing could be brought into the everyday table-top 3D printer, it would have major ramifications. In fact, if the high-temperature challenge could be solved, it may even allow for unique applications for 3D printing, including the integration of electronics into 3D-printed objects.
For example, it could be possible for a strain gauge to be printed into the walls of a 3D-printed part, thereby providing insight into internal stresses faced by a part. Another example could include the integration of an antenna into the inside of an enclosure, eliminating the need for external antennas of PCB antennas. However, the need for high-temperature sintering currently forbids such a concept as it would instantly melt away the surrounding material.
Researchers demonstrate 3D printable metallic gel
Recognising the challenges faced with 3D printing metal, researchers at North Carolina State University published their findings on a newly developed 3D printing material. The new material, according to the researchers, allows for 3D printing metallic structures at room temperature and eliminates the need for additional sintering processes. While unconfirmed, the researchers believe that their development is the first demonstration of 3D printing metal parts at room temperature, and if so, would be a major achievement for the technology.
"Our new material allows for 3D printing metallic structures at room temperature and eliminates the need for additional sintering processes," said the researchers at North Carolina State University[2].
To create the metallic gel, the researchers took a solution of micron-scale copper particles suspended in water and then added an indium-gallium allow, which is a liquid at room temperature. Combining these two solutions creates an electrically conductive gel that is printable via a nozzle.
The creation of the metallic gel involves a careful process. The researchers started with a solution of micron-scale copper particles suspended in water. They then added a small amount of an indium-gallium alloy, which is a liquid metal at room temperature. As the mixture was stirred, the liquid metal and copper particles essentially stuck to each other, forming a metallic gel "network" within the aqueous solution. This process ensures a fairly uniform distribution of copper particles throughout the material, which is crucial for forming electrical pathways and preventing the copper particles from settling out of the solution and clogging the printer[1].
"Unlike previous attempts to create metallic gels, our formula doesn’t result in the copper coming out of the solution and sticking to the nozzle of the printer, something which would hinder large prints," the researchers noted[2].
The gel is capable of holding its structure during the printing process, and as water evaporates from the gel, it hardens to become a solid 3D structure.
However, the researchers also discovered another feature behind their gel which allows for 4D printing, controllable and predictable shrinkage with time. As models dry, a small amount of shrinkage occurs, and in the case of cylindrical objects, the sides will contract more than the top and bottom. But if the model is placed in a heated environment to speed up drying, the resulting structural deformation is highly predictable. As such, printed objects can be manipulated after the fact, allowing for complex designs. Selectively drying areas also allow engineers to control how the shape behaves postproduction.
How can this gel be used in the field of electronics?
The rise of printed electronics will undoubtedly see a shift in the electronics industry due to the numerous benefits that printed parts present. For example, components printed onto flexible substrates allow for electronics to be integrated into clothes and packaging while having a limited effect on the application. Printed electronics also allow for complex designs, such as antennae integrated into product packing, without the need for additional manufacturing steps.
But in the case of this new metallic gel, the electronics engineering field could see major benefits in the form of combined printer heads whereby conductors are printed inside a 3D case to eliminate the need for wires and cables. For example, an enclosure that needs to connect a display to a PCB could print wires inside the enclosure itself, thereby eliminating the need for delicate flat ribbon cables. This would also simplify the manufacturing process, potentially allowing for the production process to be fully automated.
Such printable materials could also be beneficial in the creation of 3D circuits that involve circuits constructed in all three dimensions, not just the plane across a PCB. The result of such a design would be an increase in component density, thereby allowing for substantially more complex designs.
Overall, what the researchers have developed is truly exciting for the field of 3D printing and electronics. If the gel can be commercialised, it may not be long before we see it deployed in commercial 3D printing systems and, possibly, domestic units.
References
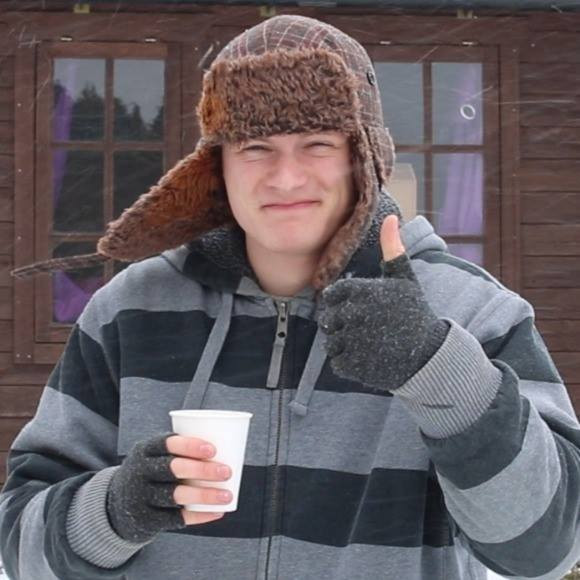