Waterproof Ultraflexible Organic PVs: Solar Tech Breakthrough
08-03-2024 | By Liam Critchley
Key Things to Know:
- Innovative Waterproofing: Recent advancements have led to the development of waterproof and ultraflexible organic photovoltaics (OPVs), enhancing wearable electronics by integrating energy-harvesting capabilities that withstand water exposure.
- Challenges Overcome: Overcoming water damage in flexible electronics has been a significant challenge. The introduction of an in-situ grown hole-transporting layer (HTL) has proven key to enhancing device durability without sacrificing flexibility or efficiency.
- Enhanced Durability: The use of a thin, 1-micron encapsulation layer has shown to maintain mechanical properties and efficiency, even under strain and after exposure to water, marking a significant step forward in wearable device design.
- High Performance: Achieving a power conversion efficiency (PCE) of 14.3% under one sun illumination, the study demonstrates that high efficiency and waterproofing can coexist in flexible organic solar cells, paving the way for more resilient wearable technologies.
The interest in flexible solar cells for wearable devices has been growing in recent years. Organic solar cells that have a high degree of stretchability and are lightweight are continuously being developed for a range of wearable and flexible solar cell applications (flexible solar cells that are not wearable are finding themselves on the sides of buildings, for example)—such as being used to power wearable devices and on-skin electronics.
Recent advancements in ultraflexible organic photovoltaics (OPVs) have opened new avenues for integrating energy-harvesting capabilities into everyday life. The development of waterproof and ultraflexible OPVs, as demonstrated in a groundbreaking study, highlights the potential for these devices to be seamlessly incorporated into wearable electronics without the risk of water damage. This innovation not only enhances the durability of wearable devices but also broadens the scope of their application, ensuring reliable performance in various environmental conditions.
However, water is the bane of many electronic devices, especially devices where the fabrication layers have gaps that can allow water to percolate through the device and cause damage and system failure. Waterproofing flexible organic solar cells has been a challenge if the mechanical flexibility and conformability of the device is to be preserved.
Fig. 1: Analysis of the Structure, Characteristics, and Mechanisms Behind Waterproof OPVs.
Below is a visual representation of the groundbreaking advancements in waterproof and ultraflexible organic photovoltaics (OPVs) as featured in the recent study. Figure 1 illustrates the innovative design and performance of these OPVs, highlighting their exceptional waterproof capabilities and the effectiveness of the annealing process in improving device efficiency. This figure includes a photograph of the OPVs floating on water, demonstrating their durability and resilience, alongside schematic diagrams and performance metrics that underscore the technological breakthroughs achieved. The enhancements in interface adhesion and the meticulous annealing treatment are key factors in achieving such high levels of performance and reliability in flexible solar cell applications.
a Image showcasing the ultraflexible and waterproof organic photovoltaics (OPVs) as they float on water, alongside a diagram detailing the structural design of these waterproof devices. A scale indicator is set at 1 cm for size reference. b Graphs displaying the J–V (current-voltage) properties of the devices following annealing processes conducted for 0 hours, 12 hours, and 24 hours at an ambient temperature of 85°C. c A depiction of the External Quantum Efficiency (EQE) progression for the OPVs over varying durations of annealing at 85°C. d Oxygen (O) element concentration profiles obtained through Dynamic Secondary Ion Mass Spectrometry (D-SIMS) analysis, comparing initial and post-annealing samples. e Diagrams illustrating the energy levels of the samples after the annealing process. (Click to enlarge)
Detailed Analysis and Breakthroughs in OPV Technology
Addressing the critical challenge of waterproofing while preserving the mechanical flexibility and conformability of organic solar cells, researchers have made a significant breakthrough. The key to this advancement lies in the development of an in-situ grown hole-transporting layer (HTL). Unlike conventional HTLs that are sensitive to water and contribute to device degradation, this innovative approach strengthens the interface adhesion between the active layer and the anode, dramatically enhancing the device's resistance to water.
This method involves the direct deposition of silver on the active layers, followed by a precise annealing process in air at 85°C for 24 hours. The result is a solar cell that not only maintains its efficiency and flexibility but also exhibits remarkable waterproof characteristics. Such an in-situ grown HTL represents a pivotal shift in the design of flexible solar cells, offering a robust solution to one of the most persistent issues in the field of wearable electronics.
Water is a big factor in the degradation of flexible electronics—especially those which are exposed to the elements regularly. However, while water condensation can occur on the device due to rain and regions with high humidity (if the solar cells are placed outside), it can also occur indoors as well. Wearable devices that are used indoors are susceptible to water penetration from everyday activities, such as washing hands. Given the presence of water in everyday situations and the susceptibility of many wearable devices to water and moisture, it is seen as a critical design parameter when creating flexible energy harvesting devices for said wearable devices.
Conventional Ways of Waterproofing Flexible Solar Cells
As waterproofing solar cells is a key factor in the performance of the device, a number of routes have been taken over the years to improve the resistance to water in flexible and wearable solar cells. One way of waterproofing flexible solar cells has been to encase them in thick encapsulation layers, anywhere from tens of microns up to 500 microns thick. These approaches have enabled the solar cells to retain up to 95% of their initial power conversion efficiency (PCE), even when submerged in water for 2 hours.
However, this is not really a practical approach for flexible electronics because to achieve water protection via this route sacrifices the mechanical flexibility and conformability of the device itself—rendering them useless for their intended purpose. New designs are being sought for flexible solar cells to make them more waterproof without the trade-off in mechanical functionality. It’s thought that adding a hole transporting layer (HTL) could be the key to bringing intrinsic waterproofness to flexible solar cells.
The challenge of achieving waterproofness in flexible solar cells without compromising their mechanical flexibility and conformability has been a significant hurdle in the field of wearable electronics. Traditional methods, relying on thick or rigid encapsulation layers, often result in devices that are less adaptable to the dynamic nature of wearable technology. The pursuit of innovative solutions, such as the in-situ growth of hole-transporting layers, represents a pivotal shift towards creating devices that offer both high performance and resilience against environmental factors.
Researchers Create an Inherently Waterproof Design
Researchers have now tested the HTL hypothesis by creating an inherently waterproof and ultra-flexible organic solar cell which uses an in-situ grown HTL layer. Many HTL layers are sensitive to water and would cause further degradation in the presence of water. However, the HTL created by the researchers was able to strengthen the interface adhesion between the active layer and the anode within the device.
To achieve a much higher degree of water resistance, a silver electrode HTL layer was deposited on top of the active layers and thermally annealed. Compared to other HTL layers that tend to be sequentially deposited, the in-situ HTL in this study had a higher thermodynamic adhesion between the layers, which meant that the device naturally had a much higher degree of waterproofness—as it was a lot more difficult for water to get between the different fabricated layers of the device.
The overall thickness of the photovoltaic component of the device was only 3 microns thick, so it still had a very high flexibility, stretchability, and conformability, and none of these properties were sacrificed to bring about the added waterproofing benefits.
Assessing Waterproof Performance Under Extreme Conditions
The researchers tested the waterproofness of the device through various tests. In a water immersion test, the solar cell only showed an 11% PCE drop in efficiency after being submerged in water for 4 hours. Even with a highly humid environment or torrential rain, it’s unlikely that any solar cell is going to be subjected to such harsh conditions for prolonged periods of time, so it is a low drop in PCE considering the amount of water it was exposed to.
The water submersion tests were also performed at different temperatures—0 °C, 20 °C, and 40 °C—and it was found that the waterproof performance was not affected by changes in temperature. This is useful for wearables that will be used in inside and outside environments, where there could be sudden changes in temperature depending on the activity of the user.
The ability of waterproof and ultraflexible OPVs to maintain their performance across a range of temperatures underscores their suitability for diverse applications. From outdoor activities exposed to the elements to indoor environments where temperature fluctuations are common, these advanced solar cells ensure that energy harvesting remains efficient and reliable. This temperature resilience enhances the versatility of wearable devices, making them more adaptable to the varying conditions of daily use.
The researchers also performed the same water submersion test after encapsulating the device with a 1-micron thick parylene encapsulation layer, and this encapsulated device showed a PCE of 92% after 4 hours of submersion. With the encapsulation layer, the device was also subjected to a machine-washing test, where the encapsulated device was subjected to two washing machine cycles, each of which lasted 66 minutes. After the test, the devices only showed a 10% PCE degradation, retaining 90% of their original PCE.
Enhancing Durability with Encapsulation: A Test of Resilience
A key question was how well the mechanical properties would be retained by using a thin 1-micron encapsulation layer compared to previous devices, which had used much thicker encapsulation layers? To answer this, the researchers performed a strain test underwater. The device retained 96% of its initial PCE under 30% strain after 300 cycles of stretching–compressing in water, showing that waterproofing could be obtained without sacrificing mechanical performance.
The integration of a thin, 1-micron encapsulation layer in the design of ultraflexible OPVs marks a significant advancement in the quest for waterproof wearable electronics. This innovative approach not only preserves the mechanical integrity of the devices but also offers a practical solution to the longstanding issue of water sensitivity in flexible electronics. By achieving a balance between waterproofness and mechanical performance, researchers are paving the way for the next generation of wearable technology that can withstand the rigours of everyday use.
The PCEs of organic solar cells tend to be a lot lower than their inorganic counterparts, and many waterproof cells sacrifice some level of efficiency to be more water resistant. By inherently creating a more waterproof device, the researchers managed to achieve a PCE of 14.3% under one sun illumination, which is a good PCE for this type of device. While the PCE was good in itself, the main benefit of this study was the ability to show that waterproofing a flexible organic solar cell doesn’t have to come at the expense of mechanical flexibility. Such strategies could be widely employed to make more wearable solar cells waterproof and functional for different wearable devices.
Conclusion
The study's findings highlight a promising direction for the future of wearable technology, where the inherent waterproofness of flexible solar cells can be achieved without compromising their efficiency or flexibility. This breakthrough has the potential to revolutionise the design and application of wearable devices, making them more resilient and versatile. As the field continues to evolve, the adoption of such advanced materials and manufacturing techniques will play a crucial role in meeting the growing demand for reliable and durable wearable electronics.
Reference:
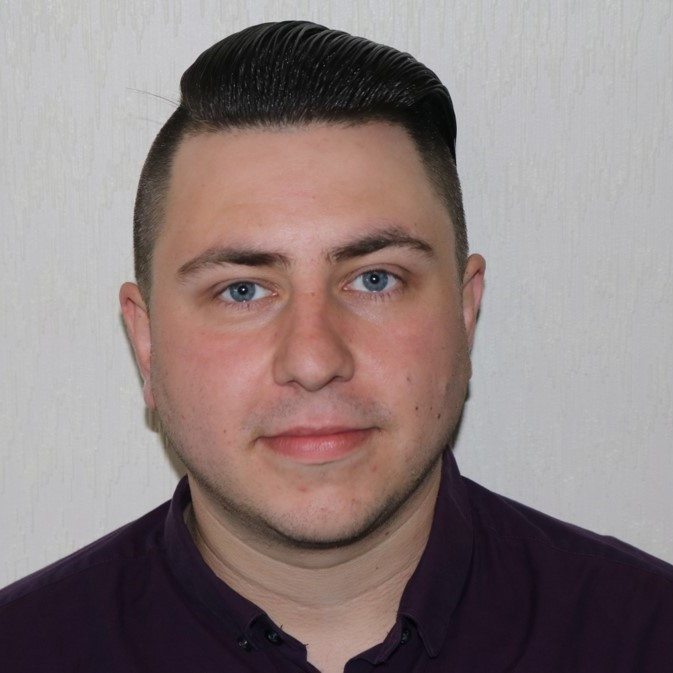