Advanced 3D Printing for Stretchable Microfluidic Electronics
Insights | 25-06-2024 | By Robin Mitchell
3D printing has often been hailed as the manufacturing method of the future, being easy to deploy, work with countless materials, and most importantly, produce almost any 3D shape that one can imagine. However, one idea that engineers are particularly interested in is the idea of integrating electronic components directly into the 3D printing process, allowing for the creation of advanced 3D structures with processing capabilities. Now, researchers have recently demonstrated a new 3D printing technique that can allow microchannels for liquid metals to flow, thereby allowing for complex electronic circuits to be produced. What challenges does 3D printing face with regard to printing electronic components? What did the researchers demonstrate, and could this technology help enable future 3D-printed electronics?
Key Things to Know:
- Researchers have developed a new 3D printing technique that integrates liquid metal into microchannels, creating flexible and stretchable microfluidic electronics.
- This innovative method eliminates the need for post-processing steps, ensuring structural integrity and enhancing electrical performance.
- Applications of this technology include wearable devices, skin-attachable NFC tags, and wireless light-emitting devices, demonstrating its potential in healthcare and flexible electronics.
- The new technique offers a scalable and cost-effective solution for mass production, benefiting industries that rely on rapid prototyping and custom electronic components.
Challenges in Integrating Electronic Components into 3D-Printed Objects
The field of 3D printing has undergone a transformative shift, evolving from an initial niche of prototyping and low-volume production to becoming a mainstream manufacturing technology. The advancements in 3D printing have enabled the cost-effective fabrication of complex solid objects, ushering in a new era of innovation in various industries. However, despite the numerous benefits offered by 3D printing, integrating electronic components into 3D-printed objects presents a significant challenge, hindering the widespread adoption of this technology.
One such challenge faced by 3D printed electronics is the need for high-temperatures when extruding materials, such as plastic and metal compounds. Such temperature requirement can affect the integration of thermally sensitive materials, such as organic semiconductors, compromising the performance and flexibility of 3D-printed electronics. Furthermore, the high temperatures involved in the process also impact the printing precision, leading to reduced resolution and accuracy in the final product.
Another challenge that 3D printed electronics can face is the need to combine multiple materials in a single print. Even though this has been solved with the use of multiple nozzles and filament changers, the delicate nature of semiconductor materials used in such printing processes means that any contamination with other materials can affect their performance.
Promising Solutions and Innovations in 3D Printing Inks
One solution that has shown great promise is the development of solvent-based inks, as these reduce the pressure requirements while widening the range of printable materials. However, the trade-off with such inks is reduced solubility, leading to solid inorganic particles that can clog the tiny channels, impeding the continuous operation of miniature printer heads (something which is essential for shrinking electronic components).
The integration of electronics into 3D-printed objects also presents challenges with regard to performance and reliability. The printed components lack the precision and accuracy of commercial components, leading to reduced electrical conductivity, lower device reliability, and limited scalability for mass production. The inherent mechanical properties of the printed materials, such as tensile strength and elasticity, impact the durability and long-term performance of the final product, raising concerns about the viability of 3D-printed electronics in real-world applications.
Overall, the challenges associated with integrating electronic components into 3D-printed objects pose a significant hurdle in the widespread adoption of this technology. Despite the advancements in 3D printing technologies, the limitations of traditional microfluidic fabrication methods and the need for high-temperature processes, solvent-based inks, and precision printing processes continue to impede the large-scale production of reliable and cost-effective 3D-printed electronics.
Innovative Advances in Microfluidics: Integrating Electronics with 3D Printing Technology
Recently, the field of microfluidics has witnessed a significant advancement with the development of a new 3D printing technique that integrates electronics into microchannels, paving the way for the creation of flexible and stretchable microfluidic devices. Researchers from the Soft Fluidics Lab at the Singapore University of Technology and Design (SUTD) have achieved this breakthrough, overcoming key challenges in the field of 3D printing and microfluidics, thereby expanding the possibilities for microfluidic devices and their applications.
In their research, Yamagishi et al. (2023) have introduced a novel approach that directly prints 3D microchannel networks using liquid-metal-based inks. This method eliminates the need for post-processing steps, which are typically required to integrate electronic elements. By leveraging this technique, they have successfully fabricated flexible and stretchable electronics, which hold promise for a wide range of applications, including wearable devices and implantable sensors.
Innovative Direct Ink Writing (DIW) Techniques in Microfluidics
Typical manufacturing methods for creating microfluid channels utilise photopolymerization techniques, such as stereolithography apparatus (SLA) and digital light processing (DLP). While photopolymerization enables the creation of complex microchannels, challenges arise during the integration of electronic components and the printing of elastomeric hollow structures. The key challenge for the researchers was finding an ink that balances softness for component embedding and robustness for structural integrity, as existing 3D printing technologies face difficulties in directly printing multilayered microchannels without supporting materials or post-processing.
The innovative use of liquid metal in microchannels allows for the creation of highly conductive paths within flexible substrates. According to the study by Yamagishi et al., this technique not only ensures the structural integrity of the printed microchannels but also enhances the electrical performance of the integrated circuits. This advancement is particularly significant for the development of wearable technology, where flexibility and conductivity are crucial.
Enhancing Conductivity and Structural Integrity with Liquid Metal
To address such challenges, the researchers optimised the settings for direct ink writing (DIW) 3D printing to create support-free hollow structures for silicone sealant. This enabled the fabrication of interconnected multilayered microchannels with through-holes between layers, a critical feature for electronic devices such as antennas for wireless communication. The team also took advantage of gradually curing resins to embed and immobilize small electronic elements, such as RFID tags and LED chips, within the 3D-printed microchannels. The self-alignment of these components with microchannels allowed for the self-assembly of components and electric wirings when liquid metal was infused into the channel.
By incorporating liquid metal into the 3D printing process, researchers have successfully created microchannels that facilitate electrical connections between conductive networks and embedded electronic components. This innovative approach has led to the development of advanced microfluidic electronics that are both flexible and stretchable.
Flexible and stretchable microfluidic electronics, including skin-attachable NFC tags and wireless light-emitting devices, made possible by liquid metal injection. Credit: SUTD
This breakthrough demonstrates the potential of combining microfluidics with advanced 3D printing technologies to create multifunctional devices. For instance, the flexible wireless light-emitting devices produced in this study highlight the capability of this technique to integrate complex electronic functionalities into compact and adaptable forms. This innovation could pave the way for new types of flexible displays and biomedical devices.
Applications and Implications of 3D-Printed Multifunctional Devices
The researchers demonstrated the potential of their technology by creating a skin-attachable RFID tag and a flexible wireless light-emitting device with a compact footprint. The team's approach also has implications for the automation of manufacturing processes, as the 3D printing method can be scaled up easily and offers a low-cost solution for mass production.
Moreover, the ability to directly print 3D microchannel networks using DIW technology can significantly streamline the production process. This method reduces the reliance on traditional manufacturing steps, thus lowering production costs and increasing scalability. As a result, industries that rely on rapid prototyping and custom electronic components stand to benefit greatly from these advancements.
Automating Fabrication Processes with 3D Printing Technologies
The introduction of 3D printing technologies has significantly transformed the manufacturing industry by enabling the rapid prototyping of complex designs, reducing material waste, and offering unparalleled flexibility in material choice. Furthermore, what the researchers have demonstrated (creating microfluid channels that can be used in electronic circuits), also shows that 3D printed devices can indeed incorporate complex electronic circuits.
The potential applications of the researchers' technology are vast, including rapid prototyping, disposable electronics, highly customised electronics, and fully integrated designs. Furthermore, such technologies could even be beneficial in future space missions, whereby crew only need to bring raw materials and a printer, allowing them to build parts as needed (i.e. no need to bring large quantities of spares whose weight could otherwise be better utilised).
The team's demonstration of a skin-attachable RFID tag and a flexible wireless light-emitting device with a compact footprint also demonstrates the technology's capabilities and suggests a wide range of future applications, including wearables and healthcare. When considering that the researchers were able to demonstrate the low-cost nature and scalability of the process, it could very well enable the production of low-cost systems in the future, thus reducing the cost of medical care.
Overall, the researchers' breakthrough has the potential to transform how electronics are manufactured, paving the way for the advancement of flexible and stretchable technologies. The automation of the fabrication process using 3D printing technologies could lead to the rapid prototyping of cost-effective, lightweight, and high-performance electronics.
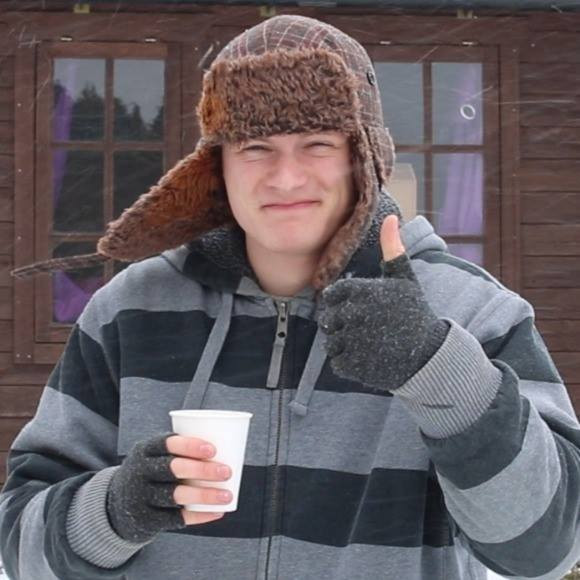