Thermoelectric Cooling for Microprocessor Hotspots Explained
Technical Analysis | 08-07-2024 | By Liam Critchley
As the performance demands of computing and other modern-day technologies become greater, the size of transistors in silicon chips has decreased in accordance with Moore's law. The higher number of transistors per area on microprocessor chips is now starting to significantly increase the heat generated per unit volume, and the performance of many microprocessors is limited by localised hot spots—which tend to be generated due to integrated circuit elements that work at high frequencies, such as the clock generator.
Key Things to Know
- Advanced thermoelectric cooling solutions are being developed to address the increasing heat generation in modern microprocessors.
- Researchers are using frequency domain thermal reflectance (FDTR) to measure and optimise cooling performance at the micro-scale level.
- Highly p-doped silicon is proving effective in enhancing both passive and active cooling, offering a dual approach to managing thermal loads.
- Future research will focus on integrating these thermoelectric devices into real-world microprocessor environments to evaluate their practical performance.
Challenges in Heat Dissipation for Microprocessors
There are now challenges within the electronics and technology sectors due to the need to dissipate larger amounts of heat to maintain a low operating temperature. Primarily, this is due to overheating, which reduces circuit performance and increases the amount of power that is leaked. If persistent heat/too high heat is present, then it can also cause transistors to break down. Circuitry components such as clock generators and arithmetic logic units (ALU) can generate average high-frequency heat fluxes on the order of 1 kW cm-2. However, in peak conditions, these heat fluxes can be five times larger than normal, generating localised hotspots on the microprocessor.
Currently, a lot of cooling systems centre around passive cooling. Passive cooling uses natural heat convection, conduction and dissipation mechanisms using heat spreaders, heat pipes, heat sinks or thermal interface materials (TIM) to maintain optimal operating temperatures. On the other hand, active cooling uses the energy from an external device to transfer the heat away from the chip. While active cooling requires more technological advancement and cost than passive cooling, the rate of fluid flow (air or liquid) is much higher during heat convection and increases the rate of heat removal—so it is seen as a more robust solution for the increasing heat being generated by advanced modern-day devices.
There is currently a need for targeted levels of cooling for localised hotspots. Different passive solutions have been developed that aim to target local hot spots through thermoelectric materials such as Bi2Te3. These materials have a high thermoelectric figure of merit with a low thermal conductivity to prevent the amount of heat from being driven back to the hot regions from the cold regions. However, these materials are not suitable for active cooling because the thermoelectric effects work in parallel to heat diffusion, so materials with high thermal conductivity are required for active cooling approaches—meaning that new cooling materials need to be found.
One option that has been proffered lately by researchers from Carnegie Mellon University in the U.S. is to use locally embedded thermoelectric devices (TEDs) to perform active cooling, where the thermoelectric effects of the material also enhance passive cooling using the Fourier law to remove heat from the hot spots to cooler regions. They're seen as a potential solution to the localised heat challenges of modern-day devices because they provide site-specific localised cooling, which can be actively controlled by applying an electrical current.
Researchers Turn to Active Cooling
Recent studies have shown that the use of frequency-encoded RF tags in thermoelectric devices can significantly improve the precision of temperature control at localised hot spots. This technique minimises the need for bulky cooling equipment and enhances the overall efficiency of microprocessor cooling systems.
Researchers have now developed an active thermoelectric cooling solution that helps to mitigate the transient heating of hotspots to improve temperature stability and have validated it using analytical tools. In this approach, the researchers developed an analytical model for cooling hotspots using an AC-powered TED that is driven at the same frequency as the local surface heating hotspots. They then applied this model to a silicon-based device.
This model incorporates advanced materials like highly p-doped silicon, known for its excellent thermal conductivity and low electrical resistivity. These properties make it ideal for managing the high heat fluxes associated with microprocessor hotspots, ensuring more effective cooling and thermal stability.
Analytical Tools for Measuring Localised Heating
To determine the localised heating temperature and how to combat it, the researchers built a model using an analytical tool called frequency domain thermal reflectance (FDTR) that took measurements of an actively cooled silicon thermoelectric device—with a pump laser replicating the hot spots that arise on microprocessors. A probe laser was then used to measure the temperature response based on the surface reflectance of the TED.
FDTR technology allows for precise measurement of temperature variations at micro-scale levels, providing critical data that can be used to optimise the cooling performance of thermoelectric devices. This approach ensures that the cooling mechanisms are both effective and efficient under varying operational conditions.
To validate the model for real-world devices, the researchers fabricated a micro-pillar TED from highly p-doped silicon. This material was chosen due to its compatibility with silicon chips, its high thermal conductivity for passive cooling, and its ability to generate high heat flux Peltier cooling without inducing Joule heating effects—this is due to having a high Seebeck coefficient (the magnitude of an induced thermoelectric voltage in response to a temperature difference) and low electrical resistivity.
The integration of p-doped silicon in thermoelectric devices offers a dual benefit: it enhances the passive cooling capacity while also enabling efficient active cooling. This dual approach is crucial for maintaining optimal temperatures in high-performance computing environments where thermal loads can vary significantly.
Optimising AC Electrical Input
During the experimental validation of their model on the silicon TED, the researchers managed to cancel the hot spot temperature up to an amplitude of 2.35 K at a heat flux amplitude of 18.5 kW cm-2 and frequency of 10 kHz. The active cooling performance could help to manifest a high-power efficiency on the silicon-based TED using both passive cooling and active cooling when the hot side of the TED is comparable to hotspots that manifest on microprocessors.
This experimental validation underscores the potential of thermoelectric devices to manage high heat fluxes effectively, offering a scalable solution for the cooling challenges faced by modern microprocessors. Such innovations are crucial for supporting the continued advancement of computing technology.
Visualising Thermoelectric Cooling Efficiency
To provide a clear visual understanding of the thermoelectric cooling process and its efficiency in managing high heat fluxes, Figure 2 from the referenced research paper offers valuable insights. This figure illustrates the design and thermal performance of the p-Si micro-TED, which is central to the cooling solutions discussed in this article.
Figure 2 from the research paper provides a comprehensive visual representation of the p-Si micro-TED setup and its thermal performance. This figure includes a schematic of the micro-TED, the FDTR measurement setup, and the experimental results that validate the model's predictions. By examining this figure, readers can gain a better understanding of how the micro-TED functions and the effectiveness of the thermoelectric cooling approach.
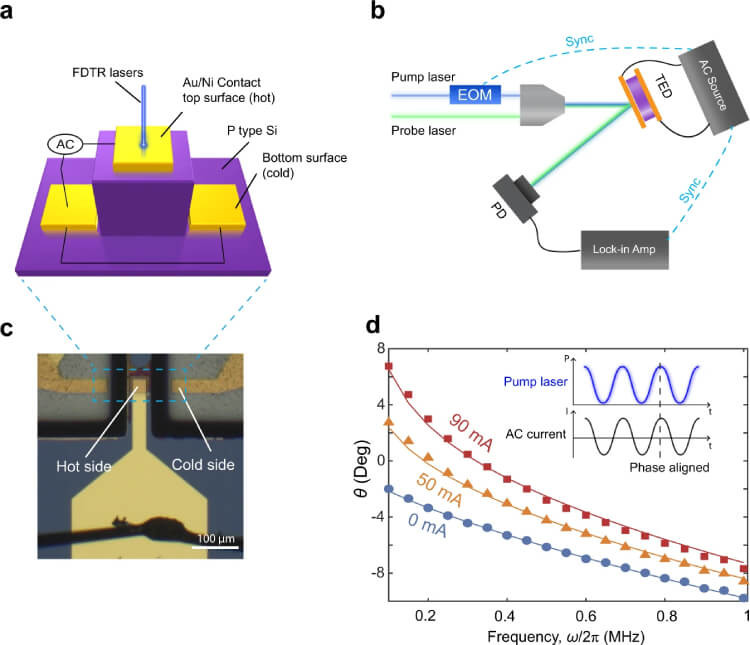
Future Directions and Real-World Applications
The researchers have created a model for tailoring the cooling efficiency of their silicon-based TED by changing the AC input to the TED. The models have been validated with a physical device, but they have only so far used laser pumps to simulate hot spots. It's been stated that this approach, and these new silicon TEDs, could be used to build new cooling systems to cancel the transient heat variations on different circuit elements within integrated circuits, but the next stage of this development is to see how well this works in actual practice using microprocessors in real-world settings.
Future research will focus on integrating these thermoelectric devices into actual microprocessor environments to evaluate their performance under real-world conditions. This step is essential to transition from experimental models to practical applications that can be deployed in consumer and industrial electronics.
Conclusion
In conclusion, as the demand for higher performance in computing and modern-day technologies continues to escalate, the challenge of managing localised heat generation in microprocessors becomes increasingly critical. The advent of advanced integrated circuit elements operating at high frequencies has exacerbated the issue, creating significant thermal hotspots that impede performance and threaten the longevity of electronic components.
The ongoing transition from passive to active cooling solutions represents a pivotal development in addressing these thermal challenges. Researchers' innovative use of thermoelectric devices (TEDs) for localised, active cooling demonstrates a promising avenue for mitigating the effects of transient heating. By leveraging the thermoelectric effects to enhance passive cooling and employing advanced analytical models to tune the AC electrical input, substantial progress has been made in stabilising and even eliminating temperature excursions.
The experimental validation of these models using silicon-based TEDs highlights the feasibility of integrating such solutions into real-world applications. Although initial results are promising, further research is essential to refine these cooling systems for widespread deployment in microprocessors and other critical electronic devices.
Ultimately, the successful implementation of active cooling technologies will play a crucial role in maintaining the performance and reliability of next-generation electronics. Continued exploration and innovation in this field are imperative to meet the growing thermal management demands of an increasingly digital world.
Reference:
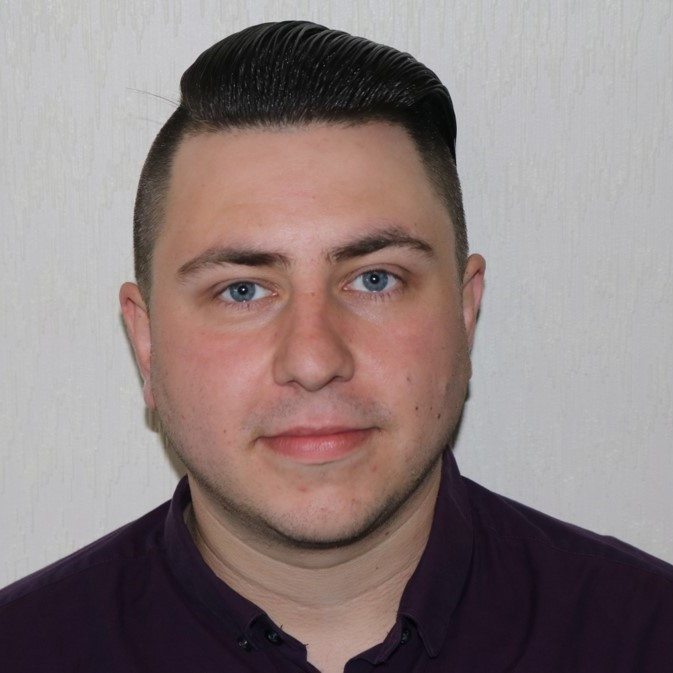