New Transistor Design Promises Faster Speeds and Durability
Insights | 23-10-2024 | By Robin Mitchell
An ultrathin material with properties that "already meet or surpass industry standards" enables ultra-fast switching and exceptional durability. (Source MIT)
As researchers continue to find new ways of making modern devices smaller, a team from MIT has developed a new transistor that is not only fast but is incredibly tough and far smaller than anything currently on the market.
Key Things to Know:
- Innovative Transistor Design: MIT researchers have developed a new type of transistor using ultrathin ferroelectric materials, offering faster switching speeds and greater durability than current industry standards.
- Enhanced Durability: These transistors can endure over 100 billion switching cycles without degradation, making them highly suitable for memory storage and other high-endurance applications.
- Energy Efficiency: The new transistor design operates at ultra-low voltages, significantly reducing power consumption, which could lead to more energy-efficient electronic devices in the future.
- Challenges Ahead: While promising, the technology faces scalability hurdles in production, requiring further research to integrate these advanced transistors into mainstream manufacturing processes.
What challenges do traditional transistors face, what did the MIT researchers develop, and could it replace current technologies?
What challenges do traditional transistors face?
Transistors, the backbone of modern electronics, have transformed the way we compute, communicate, and control power in countless devices across the globe. From the smallest smartphones to the largest supercomputers, transistors are integral components that perform the crucial function of switching electronic signals and amplifying power. However, the journey to make transistors smaller, faster, and more efficient is fraught with significant scientific and engineering challenges.
Miniaturisation Challenges
The relentless pursuit of miniaturisation, primarily driven by Moore's Law, which predicts the doubling of transistors on a microchip approximately every two years, has led to incredible advancements in computational capabilities. However, this downscaling brings to the forefront a host of issues related to the physical and operational limits of materials used in transistor design. For instance, as transistors shrink, the gate—the part of the transistor that controls the flow of current—also becomes smaller. When these gates approach the size of just a few nanometers, controlling the current becomes increasingly difficult due to quantum effects such as electron tunnelling, where electrons pass through the gate even when it is closed.
Additionally, the efficiency of transistors is compromised as they are miniaturised. The smaller the components, the greater the resistance and leakage of current, which in turn generates heat. This heat is not only a byproduct but a critical barrier to further miniaturisation and efficiency improvements, as excessive heat can lead to device failure.
Materials currently used in commercial transistor manufacturing also impose limitations. For example, the channel—the pathway through which current flows—and the gate widths are constrained to dimensions that are still hundreds of atoms thick. This limitation stems from the physical properties of the materials and the current technological capabilities in fabrication processes.
Material Limitations
Operating voltages of transistors present another challenge. Lower voltage operation is desirable for reducing power consumption and heat generation, but reducing voltage too much can lead to unreliable transistor performance and increased error rates in computations.
Over time, transistors can degrade due to various factors, such as heat, electrical stress, and material fatigue. This degradation affects not only the performance of the transistors but also the reliability of the devices in which they are used. As devices become smaller, the impact of degradation becomes more pronounced, limiting the potential for further size reduction in computational devices.
Memory technology, which relies heavily on transistors, also faces significant hurdles. Static Random-Access Memory (SRAM) struggles with achieving high memory density, which is crucial for advancing computational capabilities. Dynamic Random-Access Memory (DRAM) requires complex operations to maintain data integrity, adding to the power consumption and operational challenges. Flash memory, while beneficial for non-volatile storage, suffers from limited write cycles, which impacts its longevity and reliability.
MIT researchers create tough sliding mechanical transistors
In a groundbreaking development at the Massachusetts Institute of Technology, researchers have engineered a new type of transistor that could transform the electronics industry. The team, led by MIT physicists Pablo Jarillo-Herrero and Raymond Ashoori, utilised an ultrathin ferroelectric material, which has demonstrated capabilities that surpass current industry standards in several key areas.
Advancements in Sliding Ferroelectric Materials
Recent advancements in sliding ferroelectric materials, particularly the work on bilayer boron nitride, have demonstrated extraordinary resilience in terms of endurance and fatigue resistance. Research has shown that these materials can undergo 100 billion switching cycles without degradation, highlighting their potential for use in high-endurance memory applications. The absence of material fatigue in sliding ferroelectrics is a key factor contributing to this durability, making them highly attractive for energy-efficient, long-lasting devices in emerging memory technologies.
This innovative material, comprising atomically thin layers of boron nitride, allows for rapid switching between positive and negative charges—critical for encoding digital information. Remarkably, this transistor can operate at speeds measured in nanoseconds, a billionth of a second, showcasing its potential for enhancing processing speeds dramatically.
Furthermore, the use of ferroelectric field-effect transistors (FeFETs) based on sliding ferroelectrics like boron nitride presents opportunities for ultrafast switching speeds. Studies indicate that these transistors can switch polarisation at the nanosecond level while maintaining high endurance across billions of cycles. This capability is particularly beneficial for nonvolatile memory systems, offering a robust and energy-efficient alternative to traditional memory technologies.
Durability and Longevity of Sliding Ferroelectrics
Moreover, the durability of this new transistor is exceptional. It has successfully endured over 100 billion switches without any signs of degradation, a testament to its robust design and the unique properties of the ferroelectric material used. This endurance is pivotal for applications where long-term reliability is crucial, such as in-memory storage and computing systems.
This exceptional endurance is primarily attributed to the unique sliding mechanism within the bilayer structure of the material. Unlike conventional ferroelectrics that suffer from wear and degradation due to defects during repeated switching, sliding ferroelectrics avoid this by facilitating a smooth interlayer movement. This results in significantly improved durability, positioning this technology as a viable solution for high-performance memory and data storage applications.
Energy Efficiency and Low Voltage Operation
The thinness of the material—measured in mere billionths of a meter—not only contributes to its efficiency but also reduces the voltage required for operation. This could lead to more energy-efficient electronic devices, potentially lowering power consumption dramatically across various applications.
Additionally, the energy efficiency of these sliding ferroelectric transistors is further enhanced by their ability to operate at ultra-low voltages. The reduced voltage requirements stem from the atomically thin structure of the boron nitride layers, which allow for efficient switching without the need for excessive power input. This could pave the way for the development of next-generation electronic devices that are both faster and consume significantly less energy than current silicon-based technologies.
Collaborative Research and Interdisciplinary Approaches
The research, detailed in a recent issue of Science, has been a collaborative effort across multiple institutions and disciplines, highlighting the importance of interdisciplinary approaches in advancing technological innovations. The co-first authors of the study, Kenji Yasuda and Evan Zalys-Geller, along with a team from Harvard University and the National Institute for Materials Science in Japan, have been instrumental in characterising and testing the new material.
Despite the promising results, the team acknowledges several challenges ahead, particularly in terms of manufacturing scalability. The current production method of the ferroelectric material is complex and not yet suitable for large-scale manufacturing. However, ongoing efforts by various research groups aim to refine these processes, paving the way for broader application of this technology.
Despite these promising advancements, scaling the production of such advanced materials remains a challenge. Current fabrication techniques are limited to small-scale demonstrations, which hinders the immediate transition to commercialisation. However, ongoing research in materials science and nanotechnology aims to address these scalability issues by exploring wafer-scale production methods that could potentially integrate these novel transistors into mainstream semiconductor manufacturing processes.
This breakthrough has the potential not only to enhance existing electronic devices but also to enable new types of devices that were previously not feasible, marking a significant step forward in the field of electronics engineering. As research continues, the future applications of this transistor technology could be vast, impacting everything from consumer electronics to advanced computing systems.
Could this new transistor truly transform the electronics industry?
Despite this new transistor offering several enhanced features, including smaller size and higher operating speeds, which could significantly enhance the capabilities of electronic devices, the practical application and widespread adoption of this technology face significant hurdles.
One of the primary challenges in replacing the current silicon-based technology with any new material or device, such as the MIT team's transistor, is the issue of scalability. Silicon transistors are incredibly well-integrated into the manufacturing processes of today's semiconductor industry. These processes are optimised for mass production, capable of reliably producing billions of transistors on a single silicon wafer. This level of production scalability is crucial for meeting the global demand for electronic devices and for maintaining cost efficiency.
The new transistor, while superior in certain aspects, must demonstrate that it can be produced not just in small batches in laboratory settings but on the scale of billions as current silicon technology allows. The ability to scale production efficiently affects everything from the cost of the transistors to the feasibility of incorporating them into existing manufacturing systems without requiring prohibitively expensive overhauls.
Durability and Reliability Concerns
Furthermore, the current silicon-based technologies have a proven track record for durability and long-term reliability. Manufacturers and consumers alike rely on this established performance history, which a new technology must match or exceed before it can be considered a viable replacement. This involves rigorous testing over extended periods under various environmental conditions to ensure the new transistors can operate reliably in real-world applications.
However, it is important to note that the emergence of such innovative technologies often leads to new applications and can open up new markets. If the scalability issues can be addressed, the MIT team's transistor could potentially lead to electronic devices that are faster, more power-efficient, and capable of handling more complex tasks than current technologies allow. This could be particularly impactful in fields that require high-performance computing capabilities, such as artificial intelligence, big data analysis, and complex simulation tasks.
In conclusion
While the future of this new transistor technology is not yet determined, its potential is undeniable. The semiconductor industry must watch closely to see if these new devices can indeed be scaled up to wafer sizes and integrated into the existing frameworks of electronic device production. Only time will tell whether this new technology will move beyond the laboratory and into the consumer marketplace. For now, the industry adopts a cautious but hopeful perspective, waiting to see how these new developments unfold.
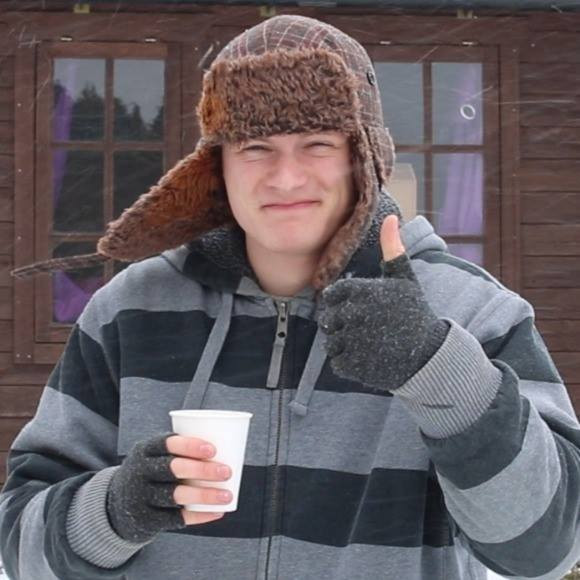