IIoT Deployment for Manufacturing: Key Strategies Explained
Insights | 26-11-2024 | By Gary Elinoff
Key Takeaways about Deployment Strategies for IIoT Manufacturing Systems:
- IoT, IIoT and the Internet all refer to the same worldwide computer network.
- Greenfield vs. Brownfield refers to all new systems as compared to systems built over what’s already established and in play.
- IIoT systems largely eliminate preventive maintenance.
- IIoT system designers must consider security as a primary concern.
Introduction
As defined by Amazon[1], The term IoT, or Internet of Things, refers to the collective network of connected devices and the technology that facilitates communication between devices and the cloud, as well as between the devices themselves. Thanks to the advent of inexpensive computer chips and high bandwidth telecommunication, we now have billions of devices connected to the internet.
A quick note: the terms IoT (Internet of Things) and IIoT (Industrial Internet of Things) are used interchangeably nowadays, so don’t let the apparent inconsistency fool you! It’s all the same internet, the very same as the network over which you’re now reading this story.
The scope of this article will be to outline the steps to be taken by industrial designers to ensure successful deployment of IIoT systems, from initial planning and design to implementation and scaling. It will provide practical tips for avoiding common pitfalls and ensuring a smooth deployment process.
Planning an IoT System
As described by Spyrosoft[2], “There are certain applications such as fleet tracking, remote machinery monitoring or logistics, where the IoT technology excels. However, in certain products, the IoT mechanisms are introduced just for the sake of implementing them.” So, to avoid wasting time and money, the very first step is to define very clearly what you want to do, and if an IoT based system will benefit the bottom line and/or to achieve other institutional goals.
Once it’s been decided that an IoT-based system has been decided on, there are some critical mistakes that must be avoided:
- Unclear Requirements. There must be a clear understanding of what the IoT deployment is expected to accomplish. There is also the scalability issue - will the system be able to easily expand when monitoring expands from a few hundred points to a few thousand or more?
- Bad Estimates. Have electrical power, computing power and RAM requirements been realistically estimated?
- Where will data be processed? Will it be at the machine site or in a remote data center? To learn more about processing data and making decisions locally and not at remote data centers, see What Edge Computing? The Future of Real-Time Data Processing is.
- As the system matures and expands, provisions have been made for easy firmware and software upgrades.
Spyrosoft also describes what it calls the 4 layers of IoT architecture.
- Sensors, Controllers, and IoT Devices. Sensors measure vital indications of machine health, such as heat, vibration or electrical current. IoT devices convert the readings into digital representations, and later, controllers can be used to cut off fluid flow or turn off current flow if the situation warrants it.
- Network Layer. Converting all those sensor reading representations into common formats for transport over the IoT to electronic decision-making data engines.
- Applications and Data Processing Layer. This layer, often powered by AI, is where decisions concerning the health of the device or system are made. Signals are then sent back down to the controllers if it is determined that changes need to be effected.
- Cloud or Data Centre. This is where information is stored for further analysis. The company suggests cloud-based solutions such as Microsoft Azure Cloud and Amazon Web Services.
But, as we’ll soon see, designers don’t always have the luxury of building a new system from the ground up.
Legacy Systems – The Brownfield Case
The situation we described in the previous section is one in which the designers have free rein, as there is no pre-existing situation that must be built around – this is an IoT Greenfield. But very often, engineers must deal with a very significant legacy infrastructure, such as a Brownfield upgrade.
As Indmall[3] points out, “Deploying Industrial IoT (IIoT) in legacy industrial automation systems presents several challenges”. Compatibility is an issue, as older systems may not have been designed with connectivity or modern standards in mind. Issues include hardware interfaces, communication protocols, and data formats.
The company suggests a “phased implementation” when updating older infrastructure, using the attachment of an IIoT-enabled sensor to an extant conveyor belt as an example. They also cite the role of middleware in “converting proprietary protocols of legacy machines into standard formats that modern IIoT devices can understand.”
Edge computing, as described earlier, may be especially relevant for upgrading legacy systems. That’s because the plethora of sensors that are part and parcel of modern IoT systems generate a titanic amount of data on a moment by moment basis, and this deluge may well be beyond the capacity of a legacy system’s communications capacity. Edge computing allows for local decision making, lessening the need to send data to decision engines possibly located thousands of miles away.
Siemens Updates a Legacy System. Siemens[4] described its Low Voltage Motor factory in Guadalajara, Mexico is being built around a series of CNC machines, unconnected to each other or to any computer network. Production time, machine availability and quality data had to be computed manually. Historical data, essential to measuring progress, was weak.
The solution was the company’s Insight Hub, which facilitated the electronic connection of each unique, legacy CNC machine, enabling a real time dashboard based system, allowing for quick analysis and decision making. As a result of this new incorporation, machining time was improved by 8% within six months, overall efficiency was improved and product changeover time was significantly reduced.
Security
IBM[5] describes Information Technology (IT) as dealing with digital information, and Operational Technology (OT) as more concerned with physical devices. Old school OT production lines were very often self-contained, with very little of no connection to the outside world other than through the human engineers and analysts who manage it. But with the IoT, vast amounts of critical data is transmitted over the internet.
The company notes that “The integration of OT and IT systems has increased the vulnerability of OT environments to cyberthreats.” Potentially, trade secrets or even national security information is vulnerable to competitors or even national enemies. Worse still is the possibility of sabotage. That’s why security, not a big factor in previous implementations of factory system control, has now become a paramount concern.
One of the most important aspect of IoT security is segmentation, with involves isolating critical OT systems from less secure IT security networks, reducing the risk of cross-contamination. That way, if a breach does occur, it can only affect an isolated portion of the system, leaving the rest safe and secure.
Beyond segmentation, IBM suggests the following practices to maintain IoT security:
- Define an overall cybersecurity governance structure and man it with a cross-functional team.
- Establish an OT security strategy with specific policies and procedures.
- Establish security training for everyone with access to any part of the system.
- A risk management framework is needed to continuously access risks, and a principal risk is outdated security firmware on older system components.
- Access control to make sure that only people who need access have access.
- Always be on guard for signs of compromise and develop a plan for a quick response.
Challenges and Opportunities
The use of IoT factory systems will largely end preventive maintenance, where employees armed with screwdrivers, wrenches, and big hammers prowl the factory floor, looking for problems that may never occur. It will be replaced with predictive maintenance, where an IoT-based system will employ past data to predict future problems.
This will call for a new type of employee, one that will not be as hard to find as some think. That’s because today’s twenty-somethings were weaned on smartphones and computer games – they see the world as defined by computer screens and respond to what they see and hear on their keyboards.
These new kids on the block, both male and female, may not be as mechanically sophisticated as their fathers were. But they’re as comfortable with computer systems as their forefathers were with horses and plows. They may not know it yet, but they’ll fit right in in the new modern factory environment.
Wrapping Up
When considering an IIoT-based manufacturing control system, whether greenfield or brownfield, careful planning from the very beginning is essential.
One aspect to applying the IIoT to a legacy system is very much like cleaning out a house – it’s hard to decide what to keep and what to discard, as some subsets that functioned brilliantly for years are just too far out of date to be a part of a modern system.
One of the main advantages of IIoT systems is that time consuming, wasteful preventive maintenance is largely eliminated, replaced with predictive maintenance. The new regime will call for far fewer factory floor employees, but those employed must be computer savvy – just the spot for today’s computer obsessed youth.
The need for sophisticated computer security, not a big factor in legacy systems, is paramount for newer IoT applications.
References
Internet of Things) (Internet of Things)?
- What is IoT (Internet of Things)? Amazon Web Services
- IoT architecture: 4 stages of building a sustainable IoT system. Spyrosoft
- What Are The Challenges Of Deploying IIoT In Legacy Industrial Automation Systems? IndMALL
- Leveraging real-time KPIs to increase overall machine efficiency. Siemens
- What is OT security? IBM
Glossary of Terms
- Brownfield IoT System. An IoT system built over an already extant infrastructure.
- Greenfield IoT System. As opposed to a Brownfield IoT System, a Greenfield IoT System is built from the ground up to function on and with the IoT.
- Segmentation. Dividing a network into multiple segments so one security intrusion doesn’t compromise the whole system.
- Preventive Maintenance vs. Predictive Maintenance. Looking for problems that may not exist as opposed to responding to likely problems predicted by computer analysis.
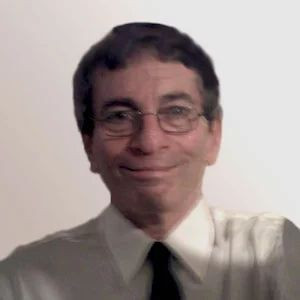