Safety Reinforced Layer Mitigates Thermal Runaway Risks
Technical Analysis | 20-11-2024 | By Liam Critchley
Li-ion batteries have surged in commercial use in recent years and are now the main battery architecture for powering portable electronics, EVs and renewable energy storage systems, and the market continues to expand year on year—with an estimate that the annual growth is around 30%, with an expected $400 billion and 4.7 TWh market size by 2030. With more technologies becoming electrified, there is a bigger need for larger capacity and higher power batteries.
Key Things to Know:
- Li-ion batteries dominate portable electronics, EVs, and renewable energy storage markets.
- Annual market growth is approximately 30%, with a projected $400 billion value by 2030.
- Increasing demand for high-capacity and high-power batteries due to electrification trends.
- Safety concerns include thermal runaway, which can lead to fires and explosions.
- Innovative safety measures aim to mitigate risks while maintaining performance.
However, despite the commercial success of Li-ion batteries, there have been many safety concerns over the years, particularly around thermal runaway that rapidly heats up (rapid temperature spikes) the inside of the battery, causing it to potentially leak chemicals, catch fire or even explode.
Safety features that can cut off the current when a battery is about to short circuit can reduce the risk of thermal runaway and prevent thermal runaway from propagating through a battery cell (and potentially into a larger battery stack). There’s now a drive to integrate new safety features that can prevent thermal runaway and other defects to stop Li-ion batteries from catching fire.
Safety Management Features for Li-ion Batteries
Li-ion batteries are already equipped with external safety features, including cell-to-cell fire extinguishers, pressure-limited valves and the use of thermally insulating materials. Cell-to-pack or cell-to-chassis designs also help to improve the safety of individual cells in battery stacks.
There are also strategies in place for compensating for the large temperature discrepancy inside and outside of the battery during the initial stages of a battery fire. One strategy is to modify the electrolytes and separator materials with thermo-responsive polymers (to provide thermo-responsive properties) to suppress ionic conduction. The second is to use positive thermal coefficient (PTC) materials to interrupt the electronic conduction when heated by transitioning from a conductive material to an insulator.
The PTC approach is particularly favourable for cutting off the battery once it hits a certain temperature. The approaches to date in manufacturing PTCs has created materials that are not compatible with standard battery manufacturing processes, or PTCs that have affected the power density and energy storage capabilities of the battery. Researchers have been looking into more commercially suitable PTC material for Li-ion batteries.
Safety Reinforced Layer (SRL) to Protect Li-ion Batteries
Researchers have created a material known as a safety reinforced layer (SRL) that enables Li-ion batteries to immediately shut down in the event of an internal short circuit or rapidly elevating internal temperature to reduce the chance of the battery overheating, catching fire and exploding.
The SRL was made using a molecularly engineered polythiophene (PTh) material doped with carbon additives. It was found to interrupt the current flow when the internal temperature of the battery hit 100 °C. This is due to the side chains in the conductive polymer undergoing a transition at this temperature to make the SRL insulating—with a fourfold increase in the resistance after the transition. Unlike many other SRLs, the doping/de-doping kinetics of the polymer ensured that the SRL maintained a high conductivity during standard battery operation.
The SRL membrane only constitutes 0.5% of the total cathode weight so it doesn’t affect the energy/power density of the battery. The process is also commercially scalable and commercially compatible with battery manufacturing. The researchers used a 500 L reaction to produce the polymer and roll-to-roll (R2R) coating system that deposited the polymer on to 1700 mm-wide current collectors. The R2R method has a capacity of up to 5 km per day, which is enough for almost 60,000 3-Ah pouch cells.
SRL Underwent Rigorous Impact Testing
Impacts are a common cause of battery fires, so as well as making sure that general operations wouldn’t cause the battery to catch fire, the researchers also tested how well the SRL-enhanced batteries managed to stop fires compared to conventional Li-ion batteries without the SRL through a number of impact tests.
Impact tests showed that the SRL reduced battery explosion from 63% to 10%—a 53% decrease by just using the SRL. During the nail penetration test, the researchers found that the battery underwent a sudden voltage drop but rapidly recovered its open circuit voltage. However, batteries without the SRL undergoing the same test had a complete voltage drop to 0V and did not recover. This shows that the SRL blocked the overflow of current to stop the shorted battery from undergoing more exothermic reactions. This has been attributed to the de-doping mechanism of the PTh in the SRL, which shuts down the local current flow and prevents internal overheating.
The batteries were also physically smashed with a heavy weight to cause a short circuit in the battery. In these scenarios, the batteries containing the SRL were found to interrupt the current flow to prevent fires and explosions. As well as there being differences in physical damage between the SRL batteries and non-SRL batteries, the researchers also found that there were notable differences in copper content on the cathode surface.
In the bare, non-SRL cells, a significant amount of copper migrated from the anode to the cathode. On the other hand, no copper migrated from the anode to the cathode in the SRL cells. Copper diffusion is known to occur in cells that have undergone over-discharge. In the impact test, intense short-circuiting leads to an over-discharge, followed by copper diffusion. The lack of copper on the cathode showed that the SRL layer prevented over-discharging during the impact tests.
The researchers have made material-level and system-level advancement to not only help make Li-ion batteries safer in multiple scenarios where the batteries could potentially undergo thermal runaway, but they have also tackled the challenges that over-safety measures have had by developing a scalable approach that can be used with battery manufacturing methods without sacrificing the power/energy density of the battery.
Reference:
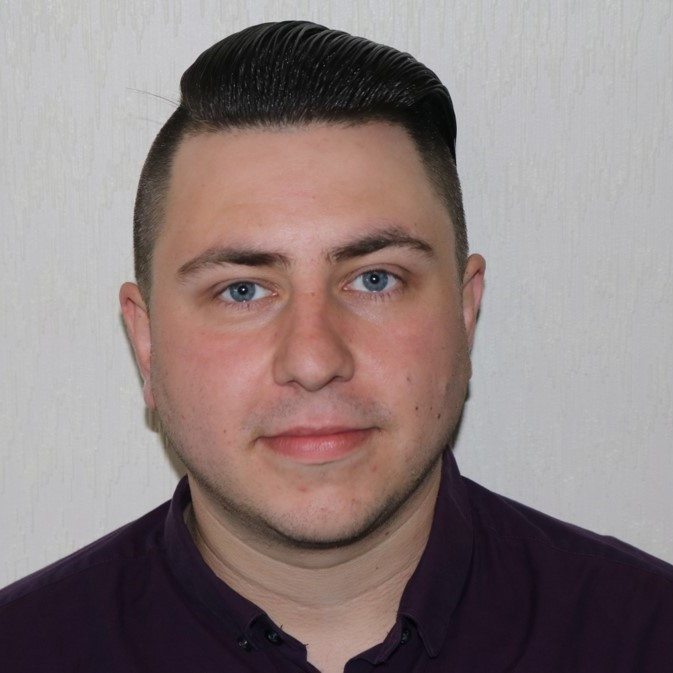