Waterproofing Magnesium Anodes for Next-Gen Energy Storage
Technical Analysis | 03-12-2024 | By Liam Critchley
The world is requiring more and more energy and the energy demands from society in a technology-driven world increase year on year. Li-ion batteries are the gold standard energy storage device for many reasons, but it’s primarily due to the combination of a good stability with a good energy density. The question remains thought, is a ‘good’ energy density going to be enough in the future when energy demands increase further?
Key Things to Know:
- Li-ion Batteries: These are the current benchmark in energy storage due to their stability and good energy density. However, their scalability for future demands is in question.
- Magnesium Batteries: Offer high theoretical energy density (3833 mAh cm-3), resistance to dendrite formation, and environmental sustainability due to magnesium's abundance.
- Challenges for Magnesium Batteries:
- Susceptible to passivation in standard electrolytes.
- Degrade in performance with minimal water contamination.
- Recent Advancements:
- Studies reveal magnesium hydride formation plays a role in passivation.
- Graphite-based waterproofing solutions have shown promise, enabling magnesium batteries to perform even in water-laden environments.
- Future Implications: Magnesium batteries, if commercialised successfully, could redefine energy storage with enhanced sustainability and performance.
That’s a question that cannot yet be answered. However, what is known is that there are many battery architectures out there that have a much higher theoretical energy density than Li-ion batteries, but for one reason or another, there have been some internal material, chemical, or electrochemical issues that have stopped them from being commercialised. You only need to look at the recent advancements made in commercialising silicon anode technology to see that change is happening; it might just take a while to manifest on large scales.
There are many options emerging for new batteries that could compete with Li-ion in the future. Some of these are widely talked about (Li-S, Solid-state, etc), whereas others are not. One that is not as widely talked about is magnesium metal batteries.
Magnesium is a promising anode material because it has a high theoretical energy capacity of 3833 mAh cm-3, a low redox potential of -2.37 V (vs a standard hydrogen electrode), is resistant to dendrite formation (something that is an issue in lithium batteries). Magnesium is also the 7th most abundant material in the Earth’s crust. There’s been a lot of discussion about using rare earth metals that are finite in the crust in batteries. With the expected volume growth for batteries in the coming years set to explode as more electric vehicles (EVs) hit the road, there is a drive to create batteries with more sustainable materials and more abundant materials.
However, while this sounds great in practice, magnesium anodes suffer from severe passivation in standard electrolytes and are particularly susceptible to performance degradation when aqueous contaminants are present, so this needs to be solved first before any talks of commercialisation can occur (just like the polysulphide shuttle in Li-S batteries, or the volumetric expansion issues in silicon anodes).
Challenges of Magnesium Metal Batteries
The passivation of magnesium anodes in standard electrolytes means that magnesium batteries today have a poor rechargeability. The presence of any water contaminants in standard non-aqueous electrolytes have shown to be the primary driver for magnesium-electrolyte interface passivation.
Trace water amounts below 20 ppm can significantly change the electrolyte solvation structure by preferably decomposing magnesium anion pairs into solvating complexes that create passivating interface layers on the surface of the anode. Additionally, water can also directly attack the magnesium in the anode to create magnesium oxide and magnesium hydroxide compounds that act as a surface passivation layer on the anode, which, over time, causes a high overpotential for magnesium plating/stripping. To overcome the issue that magnesium anodes have with water contamination (which is very small amounts), waterproofing the anode is seen as a strategy that could help the long-term stability and feasibility of magnesium metal batteries.
There have been lots of studies performed over the years looking at passivation/SEI (surface electrolyte interphase) layers in alkali and alkaline earth metal anodes. With lithium being the most prominent battery architecture, most studies have revolved around lithium passivation, with the major passivation layers being due to the formation of LiH through parasitic reactions between the metallic lithium and the electrolyte. This has also been confirmed in similar architectures using different metals, for example, the formation of NaH in sodium batteries. However, the nicheness of the magnesium battery has meant that there has not been much research so far into the formation of magnesium hydride (MgH2) as a passivation layer.
Understanding Metal Hydride Formation in Magnesium Batteries
Waterproofing the anode is seen as the best approach for magnesium batteries and is something that has been developed in a recent study. Before designing the waterproofing layer for the anode, the researchers first did some more investigations into the role of magnesium hydride in surface passivation and the impact it has on the battery.
In addition to the already-known magnesium oxide and magnesium hydroxide compounds, more directed studies into the passivation layer showed that magnesium hydride is also formed on the anode during the passivation of Mg by water. It follows a hydrogen evolution reaction (HER) after the magnesium has reacted initially with the water to form magnesium oxide and magnesium hydroxide. This process generated hydrogen gas as a reaction by-product, which then further reacts with the magnesium metal in the anode, forming magnesium hydride as well.
The formation of all three magnesium compounds on the surface of the anode was found to have a detrimental effect on the stability and interfacial dynamics of the anode. The recent study showed that all three of these compounds have a poor magnesium ion (Mg2+) absorption and transport, so their co-existence in the passivation layer prevents a reversible magnesium plating/stripping process from occurring, leading to a concentration polarisation. This then leads to high overpotentials above 2V and a rapid failure—within 1 cycle after the anode has come into contact with water. Knowing the fundamental mechanistic insights and the role that magnesium hydride plays in the passivation layer helped the researchers to build a more effective waterproofing strategy for the anode.
New Waterproofing Approach for Magnesium Anodes
Using the knowledge gained on the passivation layer, the researchers found a way to waterproof the anodes by drawing a graphite-based anti-passivation interphase over the anode with a pencil. This drawn interphase was both hydrophobic to protect the anode and water tolerant. The graphite layer was also permeable to magnesium ions (for moving in and out of the anode) to provide a high diffusivity of ions across the interface. This led to the anodes having a low overpotential and magnesium plating/stripping behaviour, even when the anode is in the presence of water—because the distribution of ion flux and the electric field at the interface was homogenised.
The addition of this graphite layer provided increased cycling stability, with the ability to cycle for more than 500 hours in symmetric cells and for over 900 hours in full cells. This cycling stability includes when the anodes were used in a simple aqueous electrolyte. The work performed in this study to understand the passivation mechanisms inside magnesium batteries and develop a simple route to circumvent the traditional issues is a good step towards making magnesium batteries a more feasible option for the future.
Reference:
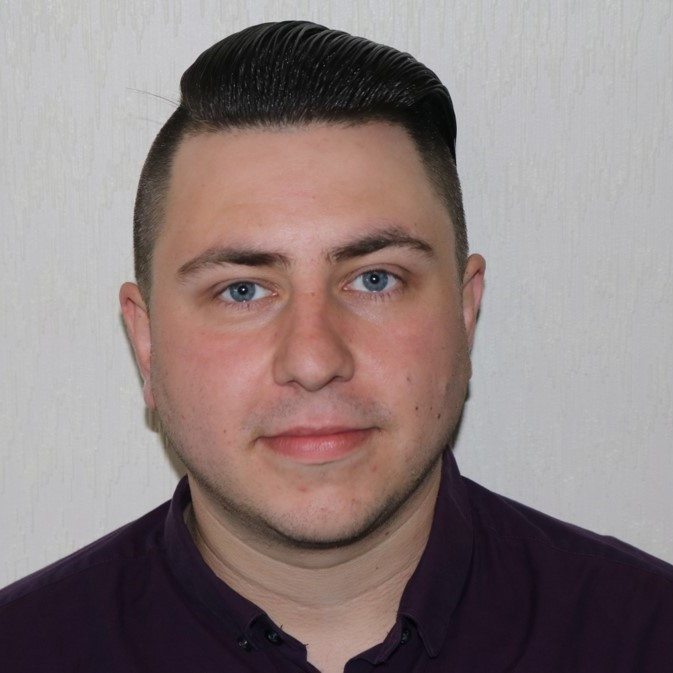