Nanogap Pressure Sensors in Capacitive HMI Technology
07-04-2025 | By Liam Critchley
Key Thing to Know:
- Flexible pressure sensors are essential for enabling fine motor control in humanoid robots, but current versions often struggle with interference from moisture, bending, and electromagnetic fields in real-world environments.
- Capacitive pressure sensors are a promising class thanks to their durability and temperature stability, but they are currently limited by external interferences like EMI and moisture, which affect accuracy and reliability.
- A new nanogap-structured capacitive sensor design reduces interference by concentrating electric fields without requiring a shielding layer, enabling high spatial resolution and reliable wireless pressure sensing.
- The technology shows promise for future HMI applications such as exoskeletons and underwater touch interfaces, though challenges remain around scalability and testing in harsh environments.
Many robotic systems are being developed today, and their capabilities are only getting better. Unlike robots of the past that have struggled with fine motor control, more recent humanoid robots have demonstrated the ability to precisely and delicately handle objects (such as an egg) due to the technological advancements in flexible pressure sensors that are added to the fingertips of robotic hands/limbs.
Robots have been demonstrating fine manipulation capabilities close to that of human capabilities and these developments have increased the expectations that humanoid robots could soon be used to perform a range of precise and physically demanding tasks in various sectors, such as the medical sector, as well tasks performed by us in everyday life.
However, humanoid robots are still restricted to controlled environments, and therefore still struggle to function in complex real-world scenarios. This is because of the current limitations of flexible pressure sensors in complex environments.
These sensors are crucial for providing tactile feedback, and in many human-machine interface (HMIs), these pressure sensors need to be resistant against external interferences―such as bending, moisture, temperature and electric fields―as well as possessing a high durability, stability and spatial resolution.
Achieving all these requirements in a single flexible pressure sensor is often a challenge, but overcoming all these limitations is going to be key for advancing HMI applications beyond their current capabilities, and there are many different types of flexible pressure sensors being developed today.
One example of these pressure sensors is the class of capacitive pressure sensors. Capacitive pressure sensors have a lot of potential for different HMI applications and in challenging handling environments―as they are already widely used in industrial applications. However, despite their commercial success in other applications, they have some critical vulnerabilities for HMI applications. These typically centre around being vulnerable to external interferences, such as moisture and electromagnetic interference (EMI). Without addressing these issues, it’s unlikely that capacitive pressure sensors will make the transition to commercial HMI applications, but a recent paper aimed to address these limitations to potentially make these sensors more commercially feasible.
Capacitive Pressure Sensors in Human-Machine Interfaces
Capacitive sensors generally have a simple structure, a high durability under extended pressure cycles, and are insensitive to temperature fluctuations. All these attributes make them promising for HMI applications. However, they still have their vulnerabilities, and even commercial capacitive sensors used in iPhones and Apple watches have these limitations.
The presence of moisture, for example, can cause ghost touches on screens due to the conductivity of water droplets. On the other hand, EMI from other devices―such as microwaves and motors―can make pressure sensing unreliable. So, even with their multiple advantages, these sensors still struggle in HMI applications that are exposed to external environments. In complex HMI applications such as humanoid robots and exoskeletons, even very small errors could result in a serious safety issue, so they need to be robust for advanced technology applications. For example, exoskeletons can malfunction in the rain if there are moisture vulnerabilities in the sensor arrays, whereas complex interferences can cause humanoid robots to drop objects that they have already grasped.
EMI shielding has been developed for capacitive pressure sensors. However, many of the sensors using EMI shielding have suffered various side effects that affect the performance of the sensor―especially by inducing parasitic capacitance between the electrodes and shielding layer that degrades the Signal-to-Noise Ratio (SNR). EMI shields can also reduce the spatial resolution of capacitive sensors as shielded sensor arrays can encounter more crosstalk between the sensors. Finally, adding shielding to the sensors increases the overall thickness of the ‘flexible’ sensor, making it harder to bend and reducing the stability under bending, affecting the performance of the sensor. So, other options beyond adding a shielding layer are required to overcome the limitations of flexible capacitive sensors.
Nanogap Structure Improves Capacitive Pressure Sensors
A new research paper has identified that fringe fields are the main cause of interference in flexible capacitive sensors. To overcome these interference fields, the researchers developed a nanogap-structured capacitive pressure sensor. The researchers reduced the gap between the electrodes to just a few hundred nanometres to suppress the fringe fields that affect other capacitive sensors―bringing EMI shielding effects without needing to add a physical shielding layer. Conventional microstructured capacitive pressure sensors have the electrodes positioned outside the handling layer, which results in large electrode gaps, but the researchers brought the electrodes within the handling layer to reduce the distance between them.
Bringing the electrodes closer concentrates the electric field, reducing fringe effects, and the result was a sensor with a reduced crosstalk between sensor cells, reliable pressure detection, a high durability above 100,000 cycles, and a high spatial resolution that is comparable to the tactile acuity of human hands―11.89 units/cm2, which is higher than the density of Merkel’s disks in the human palm at 10 units/cm². Because there is no additional layer, the structural design could be optimised to minimise bending stresses so that there was no interference due to bending.
This design was made possible using microelectromechanical systems (MEMS) fabrication processes. The researchers showcased the sensor in different wireless HMI applications, including a force touchpad system with human-level tactile acuity and an artificial pressure sensing system that can reliably detect the presence of interference (showing that it’s not affected by external interferences). The artificial pressure system detected pressures between 0-150 kPa, with a limit of detection (LOD) of 20 Pa and a 99% accuracy for detecting subtle pressures. The tests also showed that the sensor system is capable of wirelessly transmitting the pressure data to mobile devices for real-time monitoring.
The work in this study has laid some fundamental groundwork for a new type of flexible capacitive sensor that doesn’t rely on a physical layer to block out external interference. More work still needs to be done on the commercial feasibility of the sensors and whether manufacturing sensors with such a small electrode gap is feasible at scale, and more work still needs to be done on the use of the sensor in real-world applications. The researchers have also noted that a future direction could involve testing the sensors in underwater environments (and other harsh environments) to hopefully develop HMIs for smartphones that do not experience ghost touches.
Reference:
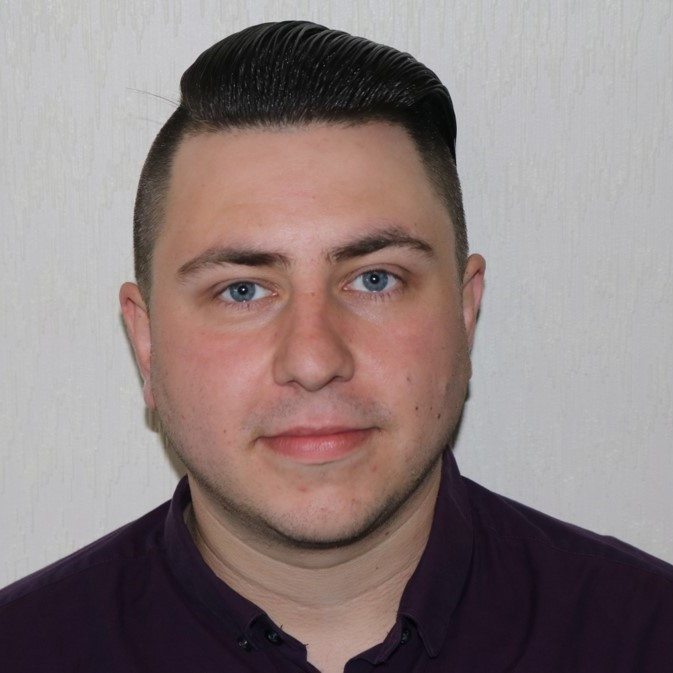