The shape of things to come. How 3D printing will rocket in 2016
08-01-2016 | By Paul Whytock
As we launch into a new year of technology the Internet is already getting its fair share of pundits proclaiming what will be the top electronic technologies of 2016.
In an attempt to either educate us or, for those corporately attached experts, to wax lyrical about their own technologies, the current trend is to make sure the blurb is presented as "the top five whatevers."
But dedicated followers of the five-ism Internet content trend might be interested to read about recent analysis of over 12,000 items of cyber content that suggests lists of 10 get much more attention.
Don't worry, I not going to burden you with my suggested top ten electronics products for 2016.
I could crack on about the surge in advanced machine learning where deep neural networks have the ability to think for themselves or the Internet of Medical Things that will revolutionise remote medical care.
And right up there with those two applications are developments in low-power wireless wide area networking and adaptive security architecture that will undoubtedly enhance the security of cloud-based systems.
But the electronics application which I think will have colossal growth this year is 3D printing. This has already shown just how phenomenally innovative it can be in providing complex products for use in anything from space exploration to ground-breaking medical procedures.
So given these existing achievements many would say that 3D printing is well and truly here and is a proven technology. And they would be right.
But it will be advances in the actual printing materials that will allow 3D printing to continue making vast market inroads this year. Current materials include nickel alloys, conductive ink, carbon fibre, glass, electronics, pharmaceuticals and biological materials. But how about this recent material breakthrough? Scientists from the University of Groningen in the Netherlands have created a 3D printed plastic that can kill 99% of bacteria that touches it. This could have a very positive impact on medical, dental and food production procedures.
The scientists involved used dental resin polymers like the ones artificial teeth implants are manufactured from and embedded antimicrobial quaternary ammonium salts inside the polymers. The salts are positively charged which causes negatively charged bacterial membranes to burst and die. Very clever stuff, although we could find ourselves surrounded by people with sparkling Hollywood smiles. Very scary.
But 3D printing, or additive layer manufacturing as it is often referred to, doesn't just exist for small objects like teeth. Rolls Royce used the technology to create a 150cm diameter by 50cm thick bearing for one of its jet engines.
Looking at electronics and 3D printing, a material that has been described as 1,000 times more conductive than commercially available materials currently on the market has been created by scientists at A*STAR's Institute of Materials Research and Engineering. They have invented a new type of thermoplastic thread that can be used in 3D printers to create functional circuits. The inventors have already employed this material to print prototypes such as USB connectors, three-dimensional circuits and wearable flexible sensors.
The resistivity of this thermoplastic material is in the range of 0.5-1.0Wcm and it is made by combining polypropylene carbon powder and then using this mixture to create filaments. A major advantage of this material is that strength and heat resistance are considerably higher than existing conductive filaments and can therefore cope with the high temperatures and physical stress involved in 3D printing.
So these breakthroughs in 3D printing materials certainly give credence to market predictions suggesting that close to 6 million 3D printers will be sold world wide in 2016. But my view is that figure could end up being a lot higher.
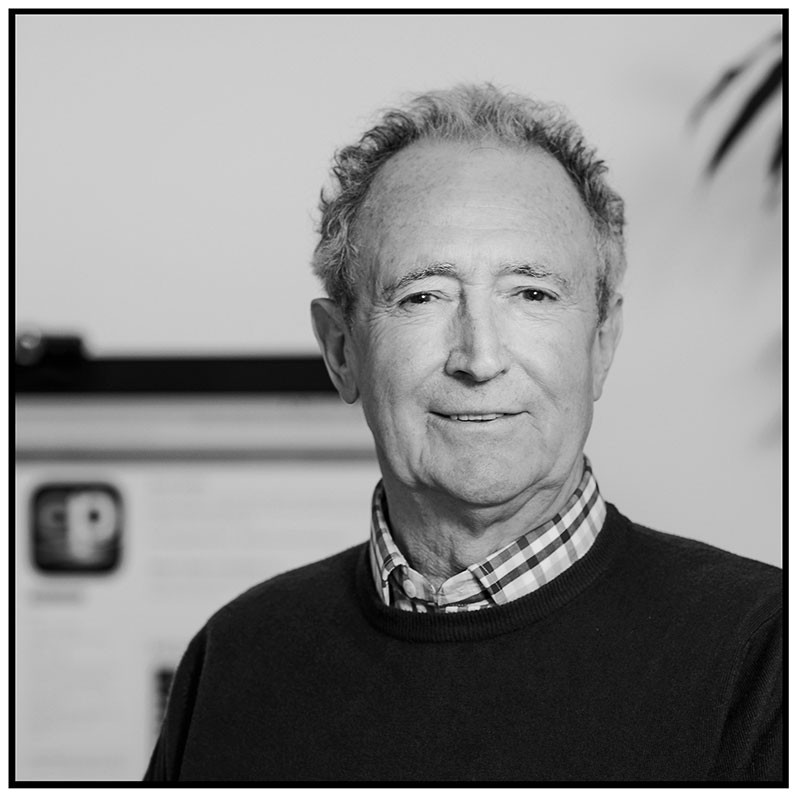