As automation marches on hardware will be key
14-11-2017 | By Mark Patrick
While automation has been with us since the 1970s, recent progress made in artificial intelligence (AI), and machine learning have helped it pick up the pace. In the coming years, more and more jobs will be automated, from the factory floor, to our roadways, and even within the service industry. Economic and political discussions aside, the technology behind this new automation is fascinating and its potential scope almost limitless.
Package Sorting Robots
With autonomous cars, delivery drones and robot burger flippers almost - but not quite here, it's easy to think that real world obstacles are doing a good job of keeping the next wave of automation at bay for now. Although, in fact, autonomous robots are already making big waves today.
Nowhere is this illustrated more clearly than in this cute, yet vaguely threatening, video of an army of little orange robots sorting hundreds of packages in a warehouse. A worker loads a package on top of each these little robotic workers, they then automatically read the location information, move to the position on the sorting floor that has been detailed and pop their package into the correct chute. Unlike human workers, these little orange robots don't need breaks or food. They work perfectly without making mistakes, and are even self-charging, meaning they can work around the clock.
Besides package sorting robots, HIKVision (the company that manufactures the little orange workers) also makes larger autonomously operated ground vehicles, which can support much greater loads. Pallet sorting, part movement, and even smart parking robots are available. In this particular case, the robot takes the form of a mobile platform which literally lifts a car and moves it into position.
The remarkable thing about these new robots, from logistics through manufacturing to parking, is not just that they do their jobs without complaint, or at a lower cost level, but that they do it better than it has ever been done before. The package sorting robots are small, and move accurately enough that less floor space is required in a sorting facility. The smart parking robots, since they can lift and rotate a car in place, use parking areas far more efficiently than human drivers and allow more cars to be parked in a given area. These processes thus become more efficient and more cost effective.
Automation Technology
To appreciate the technology behind the package sorting robots, we need to take a look at what has come before. Automated guided vehicles (AGVs) for factory and warehouse settings have been in use since the 50's, helping to facilitate material movement. For navigation purposes, AGVs used physical guides to position themselves on fixed routes. Taking different forms, these physical guides had to be built or prepared, such as wires installed into floors, strips of tape, or stickers placed on walls. Such arrangements didn’t take into account the possibility of a box or a tool accidentally being placed over one of these paths (or even an injured member of staff lying there).
Modern AGVs, like the HIKVision robots, don't need to rely on physical guides. Instead, they utilise inertial sensors (like those in smartphones), along with advanced machine vision techniques (similar to those being seen in autonomous cars). By employing inertial navigation and sensors, plus advanced image processing, these robots are able to independently traverse the environment in which they are located with only the assistance of natural features. Furthermore, they can react dynamically to any obstacles present, rather than blindly following predetermined paths without any ability to deal with unexpected changes that might occur.
Inertial Navigation
The miniaturisation of MEMS sensor devices has meant that today's smartphones, drones and AGVs can incorporate sophisticated sensing systems, which allow them to position themselves without any external guidance. The most advanced inertial sensors today are 9-axis sensors, which feature 3-axis gyroscope, accelerometer and compass functions. This enables the accurate tracking of speed, distance travelled and orientation without predetermined references being required.Machine Vision
Via machine vision techniques, robots can navigate their way through the world much closer to the way we do, by visually identifying obstacles and determining viable paths around them. The most basic machine vision techniques used in navigation involve image processing filters - for edge detection or floor finding. More advanced examples leverage deep learning techniques such as convolutional neural networks (the same as those employed in autonomous driving). These neural networks allow robots to learn to recognize objects over time, leading to better pathfinding and decision making.
Machine vision is a relatively processing intensive technique, which is why it has not been implemented until recently. It is the advent of powerful SoCs that has made machine vision a reality for AGVs (and other autonomous vehicles). These affordable, integrated chips are energy efficient enough to be used in battery operated applications (such as aerial drones), yet also capable of supporting the influx of data involved. The latest high end SoCs, such as the Apollo Lake series from Intel, even have powerful, integrated GPUs that can deal with advanced real-time image processing.
Sensors
Even the most advanced machine vision techniques are still not perfect. Autonomous cars and AGVs alike still need to rely on sensors to provide fail-safe obstacle avoidance. Ultrasonic, infrared and physical contact sensors are used to cross-check their understanding of their environment, in order to make sure robots don't bump into each other, or obstacles.Wireless Connectivity
Besides advanced, autonomous navigation and obstacle avoidance, today's AGVs are also distinguished by wireless connectivity. Through Wi-Fi connectivity, AGVs can connect to a management interface - where they can be monitored by staff or automated software to optimize traffic flow. Connected to logistics planning software, they can be deployed as needed, or scaled down to save on electricity. In addition, their paths or tasks can be altered, so as to adapt to changing requirements within the enterprise.
Future Possibilities
The advances made in machine vision and AI, in conjunction with powerful embedded systems, sensors and wireless modules, are bringing the benefits of automation to more and more industry sectors. From automatic package sorting robots, to automated parking and package delivery, the combination of AI with the latest SoC-based hardware platforms is driving a new level of automation that's never been seen before by the logistics, manufacturing and even service industries.
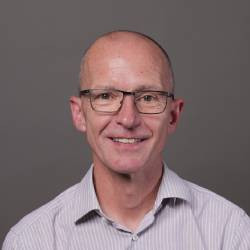