Graphene can help electric vehicles clean up their dirty act?
19-03-2018 | By Paul Whytock
The global battery industry's reliance on lithium cannot go on unabated. Alternatives must be found or, at the very least, lithium batteries must raise their game environmentally.
And the answer may well lie in graphene, the thinnest material known to man. This one atom thick carbon lattice is 200 times stronger than steel and is recognised as a very good conductor of electricity.
There are numerous research projects currently investigating how graphene could enhance the performance of lithium-based batteries by substantially lengthening their life, improving charging rates and reducing operating temperatures.
Given the environmental negatives of lithium anything that lengthens battery life is a good thing and of particular value when the quantity of lithium that will be consumed by electric vehicles ( EVs) now and in the future is considered.
In fairness to EVs however, they do have an atmospheric pollution advantage over fossil fueled vehicles and it is this positive environmental aspect that has so many people convinced they are the green machines our planet urgently needs.
Environmental Threat
So what’s the problem with Lithium-based batteries? In a nutshell the environmental threat relates to the materials they use, how those materials are mined and subsequently processed, the way electricity is generated to power them and the end–of–life questions raised about the inability to recycle them, although in reality it's not so much an inability as something that is not yet financially feasible. The technology and processes to recycle lithium batteries do exist but it's still cheaper to mine new lithium rather than recycle, despite the negative environmental impact.
But powering EVs is not just about lithium. Cobalt and nickel are elements of lithium batteries and these are two hazardous materials.
Battery manufacturers use close to 50% of planet Earth's cobalt production, a required metal for Lithium-ion cells. The problem is that mining nickel-rich ores and their subsequent crushing and transportation can generate large quantities of dust that contains large amounts of potentially toxic metals, including nickel itself, cobalt and chromium.
Of that 50% of cobalt approximately 20% is mined by hand and according to American Centers for Disease Control and Prevention long-term exposure to cobalt-containing hard metal dust or fumes can result in a serious lung condition called hard metal lung disease. Inhalation of cobalt particles can also cause respiratory sensitisation, asthma, decreased pulmonary function and shortness of breath.
And if that's not enough, nickel has been listed by the National Toxicology Program as being potentially carcinogenic.
Child Labour
Given that much cobalt is mined by hand, electric vehicle companies are still not thought to be doing enough to stop human rights abuses entering their cobalt supply chains, despite the fact that an Amnesty International investigation two years ago exposed how batteries could be linked to child labour in the Democratic Republic of Congo.
As for lithium supplies these can be found in salt flats and holes are bored into these flats and water pumped into them to bring brine to the surface where it evaporates. The resulting lithium carbonate is then put through a chemical process to extract the lithium. The problem here is that these processes use chemicals that are toxic and leach back into the soil, which not only pollutes the water systems but also areas of the surrounding geography.
So how can graphene help alleviate lithium battery's environmental negatives?
Research by SAIT (Samsung Advanced Institute of Technology) has shown that it can substantially lengthen the life of lithium batteries and also dramatically increase charging rates. Currently, Samsung's research has naturally enough concentrated on how graphene could improve lithium batteries for smart phones. But the technology could in the future be licensed for use by manufacturers of electric vehicle batteries.
High Stability
The research shows that graphene exhibits high stability, thermal conductivity and can act as a semiconductor. In this case, SAIT used silica to process graphene into graphene balls (pictured) that were used as a protective layer on the battery’s anode and cathode terminals and this provided lithium batteries with more capacity and faster charging speed.

Something of additional interest to Samsung is graphene balls allowed the battery to operate at a lower temperature which improves safety which no doubt met with strong approval from Samsung given previous problems with Galaxy Note 7 batteries.
But its not only Samsung's graphene project that's suggesting that material could greatly improve lithium performance.
Spanish company Graphenano has developed a battery based on a graphene and polymer structure which it believes could provide an EV with a range of close on 500 miles, although exactly what size, weight and type of EV was not clearly specified. The company says that because of its graphene construction the battery is capable of charging approximately 30 times faster than a lithium-ion battery.
And of course still ticking away in the battery background is the Fiskar Corporation which planned to use graphene-based batteries in its new car. The company has unfortunately dropped that plan for the moment but it has said that its research into solid-state graphene battery cells will continue.
There is little doubt that graphene could help EVs to raise their environmental game and the importance of that is reflected in figures projecting the number of EVs that will be needing lithium-based batteries in the future.
Although data on what will be the worldwide EV population by 2025 varies, a fair average estimate suggests there will be approximately 55 million; and that's a lot of lithium batteries. Anything that extends the life of lithium batteries or possibly makes lithium obsolete has to be a good thing.
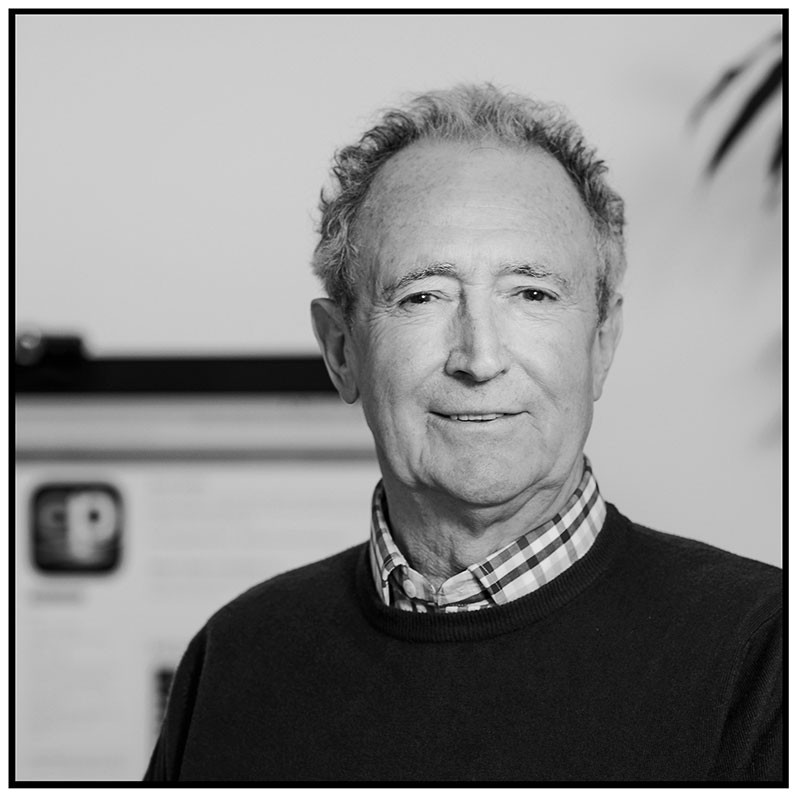