How Poor Cable Selection Destroyed a Rocket
28-11-2020 | By Robin Mitchell
Recently, a European Vega rocket carrying a Spanish built satellite was preparing to separate its upper-stage when disaster struck. What was the cause of the failed rocket, why is cable selection so important, and what does this mistake teach engineers on such projects?
How a Rocket Failed as a Result of Poor Cable Selection
Around midnight UTC, a Vega rocket was primed and ready for a launch in a space launch facility in South America. The payload was the SEOSat-Ingenio satellite which was going to be Spain’s first optical imagine satellite. The SEOSat-Ingenio had an expected mission life of 7 years taking high-resolution photos of the Earth for various applications including disaster monitoring.
However, no one would have guessed that the mission life would have been just over 7 minutes. During the final stage separation procedure, the control computer was giving commands to the thruster to point in one direction, but the rocket was rotating in the opposite direction. Shortly after, the rocket re-entered the Earth’s atmosphere, and the result was the destruction of the payload whose remains were scattered across the Atlantic Ocean.
We have seen many times in the past how rockets can fail as a result of trivial causes. For example, one Russian rocket failed as a result of its internal orientation sensors being installed upside down, thus making the rocket think it was the wrong way up. The cause of the failure in the Vegas rocket was also another trivial matter that may leave some readers shocked; a cable pair between the thrust controls and the main controller were installed backwards! Thus, any command to turn the thruster results in the opposite movement.
If a cable carries with it a polarity, why would the designers of the system not utilise a cable that also carried polarity? Cable connectors are incredibly cheap, and choosing a cable that can only be fitted in one orientation would surely be the obvious choice? On top of that, how did diagnostics not detect that the thruster was moving in the opposite direction to the desired motion?
Why is cable selection so important?
It goes without saying that choosing the correct cable for the job is incredibly important, and the result of poor cable choice can be disastrous as was demonstrated by the Vega rocket. However, there are many factors to consider when choosing cables for a design, but the most important are generally voltage, current, EMI, temperature, and mechanical.
The first step when choosing a cable is to recognise the environment that cable will be in. Will it be corrosive? Will it experience wide temperature swings? Will it be under mechanical stress and strain? From there, the cable type and family can be decided. For example, cables that will be in extreme temperature environments may require thick insulation that can handle such temperatures. In contrast, environments with vibrations may require multi-stranded cables to prevent breakage.
The second step to choosing a cable is to recognise the signal type, and any requirements those signals have. For example, if the cable is being used to transmit USB, then the cable may require a twisted pair to improve noise performance. If the cable is vulnerable to stray EM radiation (i.e. EMI), then the cable may require to be shielded. Cables that are expected to carry large databases will need to be kept short, and cables that polarity should use a cable and connector that only allow for installation in one orientation.
The third step to choosing a cable is to understand the electrical requirements of the signals, and thus choose a cable to match. However, a rule of thumb in engineering is to double the requirements to account for variations and potential upgrades in the future. For example, a cable that is expected to carry 100V should be chosen to carry 200V. When considering electrical characteristics, cables should be devalued when used in environments that can affect its performance, such as ambient temperature and the ability for the cable to dissipate heat.
What does this mistake teach engineers?
While the Vegas rocket failure teaches the importance of proper cable selection, it could be said that what is more worrying about this incident is that something as critical as the rocket thruster correction system was able to operate in reverse. When each stage is built, one would assume that software diagnostics could be run to show how the hardware will operate. Of course, the rocket itself cannot be tested by burning fuel, but the vector control system can certainly be operated and checked.
The biggest mistake that any engineer can take from this incident is to simply add a new item to a checklist of things that need to be checked before each flight. The lesson that should be taken from here is that stupid mistakes can happen. As a result, diagnostic and testing systems should be able to provide physical and artificial sensory information to check if the rocket responds correctly. For example, the upper stage could easily be suspended in a facility, fed altitude information, and see which way it tries to point the thruster. Such a test would also demonstrate how the entire control system will behave; not a simulation but an actual result of being fed real information.
Read More
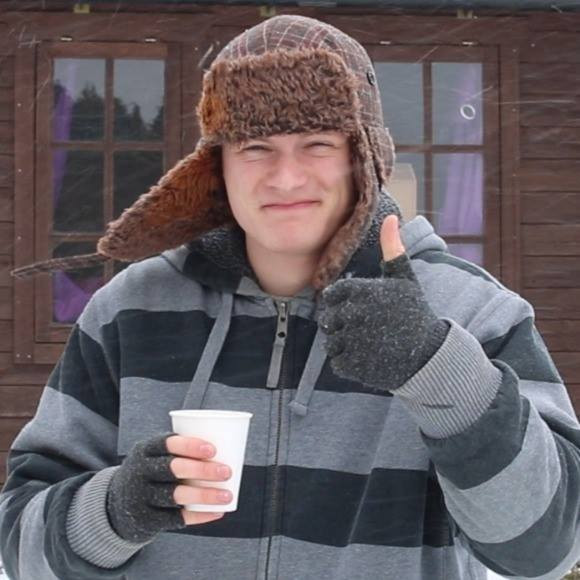