MIT researchers create 3D printed sensor for satellites at a fraction of the cost
02-08-2022 | By Robin Mitchell
It is well known that one of the most expensive fields of engineering is aerospace, and specifically, anything that goes into space. Recognising the challenges faced by low-cost space systems, MIT researchers have recently developed a 3D printing process that can create sensors at a fraction of the cost of existing solutions while still offering the same performance. What challenges does spaceflight present to engineers, what did the researchers demonstrate, and how could 3D printing technologies help to lower the economic barriers faced by spaceflight?
Why is spaceflight so expensive?
Next to antimatter and printer ink, components used in spaceflight are some of the most expensive products in the world. It is not uncommon for microcontrollers with significantly less power than an off-the-shelf STM32 blue pill that typically costs $4 to sell for well over $10K. Despite these extraordinarily high prices, the budgets that satellites and rockets have is well into the millions which makes the sale price of $10K seem insignificant. But why are such components so expensive, and what makes them so different to standard commercial parts?
The simple answer to this question is reliability. Getting to space is no small feat, and most rockets are single-use (even SpaceX’s so-called reusable rockets are only partially reusable) meaning that the cost to send anything into space is astronomical (pardon the pun). On top of that, rockets have a reputation of unexpectedly failing and always resulting in the destruction of the payload. As such, a rocket reaching orbit and delivering its payload is not only expensive but also risky.
Therefore, any satellite that does indeed reach orbit must be absolutely sure to work the first time with no issues otherwise it would represent a massive economic loss in rocket launch fees, equipment, and engineering time. Additionally, space is an extremely hostile environment filled with cosmic radiation, solar radiation, and extreme temperature gradients. As such, any component on a satellite will be bombarded with all kinds of hell for an extended period of time with no chance of physical maintenance.
To ensure that components sent into space function reliably, they have to be stress tested to extreme conditions as well as have extended operating testing of many years. It is for these reasons that many aerospace systems are based on technology from twenty years ago as only they will have had years of testing with an absolute guarantee to work. Thus, an 8-bit microcontroller from 1995 makes for a better choice than an STM32 blue pill if the 8-bit microcontroller has proven to function without error for 25 years.
Finally, parts that have this level of reliability will undoubtedly be expensive to produce and test. Furthermore, the demand for such parts is extremely small (compared to the commercial market), and thus the cost of manufacturing for each part is extraordinarily expensive.
MIT Researchers Create 3D Printed Sensor Usable for Satellites
Recognising the challenges faced by satellite manufacturers, MIT researchers recently demonstrated a new manufacturing process using 3D printing technologies to create a 3D printed plasma sensor. The sensor, called a Retarding Potential Analyser (RPA), is used by satellites to monitor the chemical composition and ion distribution ion in the Earth’s upper atmosphere, but such sensors are extremely expensive and take weeks of manufacturing in clean rooms.
However, MIT researchers demonstrated that such sensors can be manufactured using a 3D printer and laser cutter in a fraction of the time (days compared to weeks). Additionally, the cost of the 3D printed sensors was in the tens of dollars range which is significantly cheaper than the current solutions being offered. Finally, the researchers also demonstrated how the performance of their 3D printed sensors is able to compete with mainstream devices. While this doesn’t mean that the sensors are able to withstand the same g-forces or show the same degree of reliability, it does present economical options for satellite manufacturers.
The researchers pointed out that their technologies could be targeted at CubeSats that specifically focus on low-cost satellite platforms. Furthermore, the combination of fast manufacturing and low price could drive the industry towards digital manufacturing technologies that reduce the dependency on clean rooms and third-party manufacturers.
“Additive manufacturing can make a big difference in the future of space hardware. Some people think that when you 3D-print something, you have to concede less performance. But we’ve shown that is not always the case. Sometimes there is nothing to trade off,” - Luis Fernando Velásquez-García, principal scientist in MIT’s Microsystems Technology Laboratories (MTL) and senior author of a paper presenting the plasma sensors.
How could 3D printing technologies change the space industry?
There is no doubt that 3D printing technologies can help reduce the cost of the space industry in general. For example, instead of trying to make rockets reusable, it might be more economical to create parts that are intentionally one-time-use but can be cheaply printed and reinstalled. The use of 3D printed parts can also open up engineers to creating their own sensors from scratch without having to rely on a third-party manufacturer that may charge extraordinarily large amounts to create custom designs.
But what makes the 3D printing industry exciting is its potential use in space. Future space missions will contain a large number of complex parts, and bringing multiple spares for every single part is not going to be practical. As such, future missions could instead bring raw materials and additive manufacturing systems (such as 3D printers) that can print parts as they are needed.
Overall, what the MIT researchers have demonstrated is truly exciting for the field of aerospace technologies and continues to demonstrate the power of 3D printing technologies.
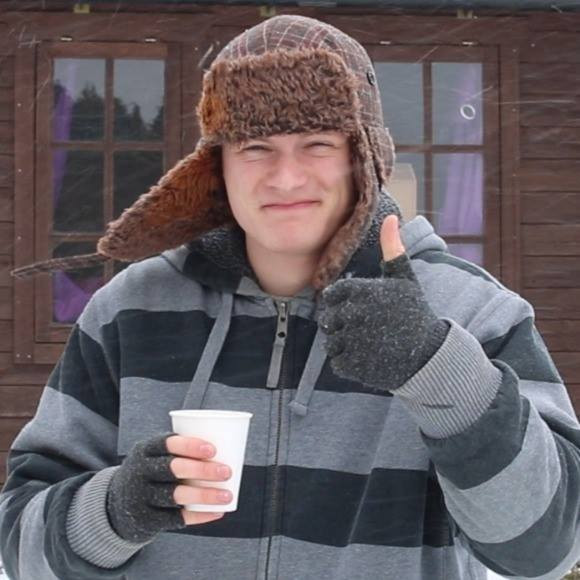