Power Electronics in EVs: Key Roles and Challenges
11-06-2024 | By Robin Mitchell
Table of Contents:
- Introduction
- The Electrification of Automotives
- The Rise and Challenges of Electric Vehicles
- Challenges of Electric Vehicles
- Technological and Efficiency Challenges of EVs
- Power Management in Modern EVs
- Power Delivery in Modern EVs
- Power Control in Modern EVs
- Power Conversion in Modern EVs
- Efficiency Challenges for Power Electronics in EVs
- Weight Challenges for Power Electronics in EVs
- Heat Challenges for Power Electronics in EVs
- Vibration Challenges for Power Electronics in EVs
- Future of Power Electronics in EVs
- Conclusion
- References
Introduction
Power electronics are critical for the conversion and conditioning of electrical energy, and are found in almost all circuits, whether it’s a smartphone or a high-voltage rectifier. However, one industry in particular, EVs, are especially dependent on power electronics due to their electric nature. In this continuing adventure into the field of power electronics, we will explore how power electronics are used in EVs, what challenges they face, and where they may lead in the future.
For a comprehensive understanding of what power electronics entail, refer to What is Power Electronics?.
The Electrification of Automotives
As the world continues to navigate the many challenges presented by climate change, transportation remains one of the most critical sectors to tackle due to the sheer amount of greenhouse gas emissions derived from it. Since the turn of the 20th century, the vast majority of vehicles have rolled off production lines with internal combustion engines (ICE) thanks to their convenience, versatility, and ease of manufacture. Even though newer ICE vehicles incorporate various electronic systems, they still largely consist of mechanical parts, making them easy to repair and maintain. To learn more about the evolution of power electronics, you can read The History of Power Electronics.
However, the reliance on fossil fuels has introduced numerous issues that are far from convenient. For instance, vehicles that utilise petrol as a fuel source emit carbon dioxide, a greenhouse gas that contributes to the climate crisis. Furthermore, the abundance of fossil fuels and how they are obtained creates geopolitical tension between nations, especially when considering that some nations are heavily dependent on others for oil. Finally, the health impacts from vehicle emissions are well documented, contributing to poor air quality in urban areas, thereby worsening the quality of life for millions of people.
As such, the idea of electric vehicles (EVs) has taken the world by storm as they offer a potential solution to the problems presented by ICE vehicles. Instead of utilising fossil fuels, EVs turn to electric power which not only provides smoother acceleration but also quieter operation. If EVs are charged from renewable energy sources, they can be carbon neutral, thereby eliminating their CO2 footprint.
The Rise and Challenges of Electric Vehicles
While there are still numerous challenges that EVs face (ranging from charging times to limited range), developments in both technology and infrastructure are gradually seeing ICE vehicles replaced with their electric counterparts. For example, the gradual electrification of everything is helping to increase the demand for EVs, while countless developments in battery technologies are enabling EVs to have greater ranges.
Despite the positive message that EVs portray, they are far from being as green as once thought. For one, the manufacturing of EVs is an energy-intensive process, requiring vast amounts of electricity to produce the many tons of materials needed, whether it's nickel for the batteries or rare earth minerals for the permanent magnets in the motors. If this electricity is derived from fossil fuels, the CO2 emissions from EVs can be significantly greater than those of ICE vehicles over their lifetime.
Overall, EVs offer a potential solution to the climate crises caused by transportation, but the many challenges faced by EVs will prevent them from becoming the dominant form of transportation in the near future. Unless EVs can be produced at a significantly lower cost than ICE vehicles, only those who can afford to charge them at home will be able to take advantage of their benefits. Unless charging points become as common as petrol stations, EVs will continue to be a niche market. And unless the many technological challenges faced by EVs can be solved, their range will remain limited, making them unsuitable for long journeys.
Challenges of Electric Vehicles
The integration of electric vehicles (EVs) has undoubtedly brought about a multitude of challenges, most of which were unforeseen by those who advocated for their use as a replacement for fossil fuel-based vehicles. For instance, the very idea of a vehicle having a limited range is something that has been tolerated since the first steam-powered carriages made their debut on the roads. However, unlike their predecessors, modern EVs are unable to quickly recharge, making them impractical for long journeys or those that require a fast turnaround at refuelling stations.
While it is perfectly possible to install more charge points across car parks and streets, it should be understood that such locations will unlikely ever be as numerous as petrol stations. This is because petrol stations offer a fast refuelling experience, with cars able to drive in, fill up, and be on their way in a matter of minutes. By contrast, EV chargers take hours to provide a full charge, meaning that EVs require far more planning and preparation. To make matters worse, most car manufacturers have their own proprietary charging ports, meaning that not all chargers are equal, further complicating the lives of EV owners.
Adding to the frustration, EVs face numerous technological challenges with regards to their internal components. For example, early EVs suffered from the use of electromechanical relays, which were never designed for automotive environments. As such, these components had a habit of failing catastrophically, something which can be disastrous for both the driver and other road users. While modern EVs have far more advanced systems, reliability is still an issue, with some manufacturers having to recall thousands of vehicles due to faulty software or poorly designed batteries.
Technological and Efficiency Challenges of EVs
Efficiency is another factor that EVs struggle with, and this is particularly problematic for those that rely on electricity derived from fossil fuels. While it is well understood that EVs have a far better environmental impact than ICE vehicles, the high energy consumption of EVs can make them expensive for those who drive long distances (especially when considering that modern energy prices have skyrocketed compared to fuel). To make matters worse, when considering that all components of an EV need to become electric, the burden on the battery is immense, with AC, heating, and power all drawing on the same energy source.
Finally, with regards to the environment, it is often stated that EVs are the solution to a more eco-friendly future, but this may be far from the truth. While their use does reduce CO2 emissions if that energy is sourced from renewable sources, the mining of lithium and other critical materials has a devastating impact on the environment. This has resulted in mining companies destroying vast quantities of land, displacing indigenous populations, and introducing toxic compounds into the environment.
Power Management in Modern EVs
As electric vehicles navigate the automotive environment, they are faced with a multitude of hurdles that significantly impact their performance and longevity. While the transition from traditional fossil-fuel vehicles to electric vehicles promises a cleaner and more sustainable future, the inherent characteristics of batteries and the dynamic nature of the automotive environment pose unique challenges that engineers need to address effectively.
Maintaining the correct voltage and current levels is crucial for both battery health and vehicle operation. Power electronics play a vital role in achieving this by regulating the flow of energy from the battery to the motors and ensuring that both the battery and motors operate within their designated parameters. However, simply providing power is not enough; the power needs to be carefully shaped to eliminate strong transients that can damage the motors or other components. Additionally, large instantaneous voltage spikes can cause sparking and welding of electromechanical contacts, highlighting the importance of accurate and rapid voltage control.
Balancing the voltage and current becomes even more complex when considering that modern vehicles use modular designs with multiple batteries connected in series and parallel. In the case of lithium-ion batteries, balancing is critical as any cell that is charged or discharged unevenly can cause damage. Power electronics with intelligent balancing capabilities are essential to ensure that each cell is charged and discharged equally, thereby extending the life of the batteries and ensuring optimal performance.
When it comes to charging, electric vehicles face another set of challenges that require sophisticated power electronics. Not all charging stations offer the same charging currents or voltages, and vehicles need to be able to accept a wide range of charging configurations. Power electronics with intelligent communication capabilities can enable vehicles to communicate with charging stations to determine the optimal charging conditions, ensuring that the battery is charged as expected by the manufacturer while minimising the impact on the environment.
Lithium NMC battery pack for electric vehicles, showcasing high-voltage energy storage for automotive applications.
Power Delivery in Modern EVs
In modern EVs, delivering power from the battery to the motors is no small feat as EVs require high-performance power delivery systems to maximise their range, improve their acceleration, and maximise power delivery to the motors. While past EVs have used hydraulically controlled systems when controlling power systems, modern EVs use electric systems for controlling the motors as well as connecting and disconnecting the motors from the main electrical system during regenerative braking. At the heart of this power delivery system are power delivery components that are responsible for getting power from the battery to the motors, and designing this stage of the system carefully is critical to the overall performance of the vehicle.
High-power relays and transistors are the two main candidates for power delivery components due to their ability to handle large amounts of power. For systems that require an absolute mechanical disconnect between the batteries and motors during regenerative braking, high-power relays are the clear choice. Solid-state transistors are far easier to integrate into high-speed systems, provide better thermal characteristics, have a lower mass, and can switch at far higher speeds. As such, solid-state transistors are the preferred choice for motor control in EVs.
Power Control in Modern EVs
When it comes to the control of motors in modern EVs, power electronics play a central role due to the use of high voltages and large currents involved. For example, motors cannot directly connect to the high-voltage batteries used in EVs as this would result in a very inefficient system with large amounts of energy lost as heat (and that motor coils would likely be destroyed by the high voltage). Instead, EVs utilise step-down power converters to reduce the voltage from the batteries to something that is appropriate for the motor itself.
But even then, motors in EVs cannot be directly connected to such power converters as power delivery to the motor needs to be carefully controlled. For example, slow acceleration of an EV requires the power system to deliver a small amount of power to the motors, while high acceleration and high torque requires the motor to be given as much power as possible. If the power to the motor is not controlled properly, the motor may experience overcurrent, overheating, or permanent damage.
It is for these reasons why EVs utilise power electronic systems that consist of special transistors and controllers that are capable of high-frequency switching, reducing energy losses in the motor, and providing the motor with the exact amount of power it requires when it requires it.
In addition to controlling the amount of power that the motor receives, power electronics in EVs also play a critical role in regenerative braking whereby the motor is used to brake the vehicle. Simply put, by connecting the motor to an internal battery charger, it becomes possible for the cars motion to charge the onboard battery, thereby slowing down the vehicle and increasing its range. For a deeper dive into the functioning of power electronics, see How Power Electronics Work.
Power Conversion in Modern EVs
When it comes to electric vehicles, the use of power electronics goes beyond just traction motors and battery management; EVs also require power electronics when it comes to low-voltage systems, also known as auxiliaries. These low-voltage systems include features such as heated seats, mirrors, and climate control that are an important aspect of the driving experience, but unlike the motors and battery, these systems operate at much lower voltages, commonly in the 12V to 48V range.
To interface with these low-voltage systems, a high-voltage battery and DC bus are not suitable, and so EVs utilise DC/DC converters to reduce the voltage from the battery to a lower level. For example, an EV with a 400V DC battery may utilise a DC/DC converter to produce a 12V bus for controlling accessories, and another DC/DC converter may be used to produce a 48V bus for the electric motor. As such, DC/DC converters play a critical role in EVs as they allow for the high-voltage battery to be safely insulated while still providing power to low-voltage systems.
Efficiency Challenges for Power Electronics in EVs
As the demand for electric vehicles continues to increase, researchers and engineers are faced with numerous challenges, and when it comes to power electronics in EVs, by far one of the most important factors is efficiency. Having an efficient system not only reduces the amount of energy needed, thereby lowering energy costs, but also allows for smaller batteries to be used while simultaneously increasing the range of the vehicle.
Improving the efficiency of power electronics in EVs can be achieved in a multitude of ways. To start, reducing the resistance of components used in EVs can help to minimise losses during energy transfer. This can be especially important for cables used to transmit power to the wheels of the vehicle, as large currents flow often flow through them, resulting in wasted energy (via cable heating). Another option for improving efficiency is to switch over to new technologies that have lower efficiencies than those currently being used. For example, silicon carbide (SiC) devices have significantly lower losses compared to silicon devices, thereby making them an attractive option for future designs.
Furthermore, making the most of switch-mode technology can also contribute to improved efficiency. Linear regulators, which can be used to regulate power for microcontrollers and other sensitive digital logic systems, typically have very low efficiencies of around 50-70%. By contrast, switch-mode regulators can easily have an efficiency of around 95%, thereby making them a better option for controlling voltages. However, switch-mode regulators are also more complex, thereby making them harder to design for, and can be extremely noisy (with regards to EMI), which can have a negative effect on the performance of key components such as digital circuits.
Increasing the delivered voltage across the vehicle is another option for improving efficiency. Currently, most EVs operate at voltages of around 300V, but there is no reason why this voltage has to be restricted to this range. By increasing the voltage to, for example, 400V, the current drawn from the battery can be reduced, thereby reducing losses in cables and other components. However, using such high voltages introduces serious risks during maintenance operations, thus, requiring the installation of special safety systems.
Weight Challenges for Power Electronics in EVs
When it comes to commercial products, the weight of components is often given little to no concern, as any weight savings are negligible compared to the overall weight of the product. However, when developing technology for use in electric vehicles, the story is very different, as every gram of unneeded weight results in a shorter range for the vehicle, and therefore requires more frequent charging. While small components such as resistors and capacitors barely contribute to the overall weight of an EV, large components such as power controllers and heatsinks do indeed carry a significant weight burden.
For example, devices that produce large amounts of heat as a result of energy loss require heatsinks of sufficient size, and these can be heavy. Having a few grams of extra weight on a power component can potentially see a reduction in range, and for a product whose range is a major selling point, this can be a deal breaker for potential customers.
Redundancy is another factor that contributes to the overall weight of EV components, as many critical components are often fitted with redundant systems so that if one fails, another can take its place. While this is ideal for reliability, it does mean that more components are being used overall, and this waste contributes to a greater weight burden.
Finally, large electromechanical parts such as motors and gearboxes are extremely heavy, which is why solid-state devices are so desperately sought after. If EVs can be relied upon to have solid-state batteries and motors, then their range will be far greater, and will even be able to carry more weight overall.
Heat Challenges for Power Electronics in EVs
With the massive amounts of energy being handled by electric vehicles, heat is now a major concern for engineers trying to cram as much power as possible into a relatively small space. For example, in cold weather, outside air can easily be circulated over power components to warm up the interior of the vehicle, but in hot weather, trying to keep power electronics cool can be a daunting task.
While passive cooling methods such as heatsinks can be used to reduce the temperature of components, their use comes with a multitude of issues. For one, heatsinks add significant weight to the overall design, something which doesn’t do EVs any favours when trying to improve their range.
Another challenge that engineers face is finding the perfect balance between component density and heat dissipation. If components are placed too close together, heat dissipation can be negatively affected, thereby reducing the overall efficiency of the system. Thus, spreading components out too much can improve heat dissipation, but at the cost of reduced density and increased weight. Finding that balance is a delicate act that requires careful planning and consideration.
Finally, when it comes to the automotive industry, components are expected to undergo thousands of thermal cycles during the lifespan of a vehicle, from extreme heat to freezing cold temperatures. Such thermal cycles can induce thermal stresses in components and the surrounding PCB, eventually leading to cracks and damage. Because standard commercial off-the-shelf components are unable to handle such conditions, engineers are given fewer options when selecting components.
Vibration Challenges for Power Electronics in EVs
Strong vibration from the wheels and road is a fact of life for EVs, and is caused by a combination of the road conditions, the vehicles speed, and the design of the wheels themselves. For the vast majority of parts, vibration is either a minor concern or doesn’t affect performance at all (such as the case with processors). For power electronics, however, vibration can be a major source of headaches for engineers as most power electronics in automotive applications are electromechanical.
While vibration alone won’t typically cause damage to solid-state devices, it can induce momentary disconnections between contacts in electromechanical parts. If these moments of disconnection are severe enough, it can be especially dangerous for devices that rely on a stable DC source (such as controllers). To make matters worse, as vibration over time can damage parts, it is possible for a device to suddenly fail during operation, especially if the vibration damages the internal structure of the part.
Trying to solve the vibration issue is not easy, as every part that is vibrated needs to be carefully designed and tested. Some parts that do exhibit a degree of flexibility are rarely able to flex significantly, and even if they can, the solder joints used to keep them attached to a substrate can easily crack. In the case of power electronics, this means that parts need to be securely mounted while simultaneously allowing for a degree of flexing, all while keeping solder joints strong and intact.
One solution is to mount parts as close to the centre of the vehicle as possible as this results in less vibration. However, this may not always be possible for components that need to be at the extremes of the vehicle, such as lights, wipers, and motors.
Another option is for engineers to use shock-absorbing materials to try and reduce the effects of vibration. For example, parts can be mounted into special vibration-dampening enclosures that use mounts and springs to absorb most of the vibration. While this works well for small parts, trying to dampen the vibration of large parts (such as a motor) is extremely difficult, and can be a costly solution.
Future of Power Electronics in EVs
As the world continues to strive for increased efficiency and performance in electric vehicles, power electronics play a pivotal role in the development of high-voltage systems capable of delivering large amounts of instantaneous power. While traditional silicon devices have dominated the industry due to its abundance and usability, solid-state devices are the future of power electronics in EVs due to their lack of moving parts, ability to operate at high frequencies, and easier of integration.
Solid-state devices, such as those made from Silicon Carbide (SiC), are already making strides in the industry thanks to their high operating voltage, superb heat tolerance, and low channel resistance. However, SiC is expensive per device, making engineers hesitant to adopt, and its expensive nature makes replacing devices during maintenance an extra burden on manufacturers. Furthermore, SiC cannot be used in the same way as traditional silicon devices, meaning that they are not a drop in replacement, requiring special drivers. But unlike silicon devices, the better capabilities of SiC means that fewer devices are required, resulting in a reduction in both weight and cost for the same performance.
While SiC presents engineers with numerous advantages, GaN is another potential candidate for the EV industry, offering high voltage and fast switching capabilities. Like SiC, GaN is ideal for switched mode applications, such as motor controllers, thanks to its ability to handle large currents and withstand high voltages. However, GaN still suffers from some limitations, including the inability to get p-type devices, thus restricting its capabilities.
Looking ahead, it is likely that a combination of SiC and GaN will prevail in the EV industry, with SiC providing the foundation for GaN to excel. As technology continues to advance, it is likely that new start-ups will emerge to find solutions for replacing SiC with GaN, thereby eliminating its expensive nature, and finally giving GaN the opportunity to shine. Overall, solid-state devices are the future of EVs, and while SiC may be the bridge between the past and the future, GaN will be the one to take the EV industry by storm.
Conclusion
Power electronics in EVs refers to the use of electronic components to control the flow of electrical power from the source to the motor, and everything in between. While power electronics may seem like a simple concept, the truth is far from simple. Unlike small devices such as phone chargers and computers, EV power electronics are required to handle far more power, hence the need for larger devices.
Trying to develop small and light power electronics for EVs is essential if the aim is to create vehicles with extended ranges, high acceleration, and large battery options. Considering that EVs are already large and heavy, adding too much extra weight can quickly reduce their usability, and considering that batteries are energy-intensive, every watt counts.
Looking forward, there is no doubt that SiC and GaN will dominate the power electronics industry in EVs thanks to their higher breakdown voltages, smaller footprint, and higher efficiency. But until then, engineers will continue to struggle with the weight of the beast that is power electronics in EVs.
Overall, power electronics in EVs is a topic that rarely gets discussed, but when considering the importance of power electronics, it should always be at the top of the conversation.
References:
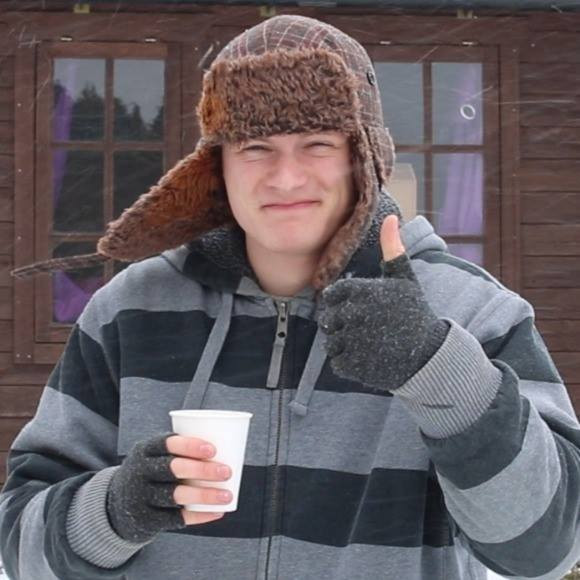