Industrial Metaverse: Is It Worth the Hype for Manufacturing?
18-11-2024 | By Tom Cash
The industrial metaverse offers thrilling opportunities alongside significant challenges for the manufacturing sector.
Siemens has made headlines with its ambitious €500M investment in a new technology campus in Erlangen, Germany. This move is a bold step toward realising the vision of an industrial metaverse, a photorealistic virtual representation of the world powered by AI. As an industrial parts supplier, Siemens aims to pioneer flexible and sustainable manufacturing technologies that redefine industrial processes, inspiring the broader industrial community to explore similar transformations.
Key Things to Know:
- Siemens' investment aims to create a real-time, AI-driven virtual manufacturing ecosystem.
- The industrial metaverse builds on existing technologies like digital twins, AR/VR, and blockchain.
- Key challenges include achieving interoperability, establishing regulatory standards, and overcoming technical barriers, as noted by the Manufacturing Leadership Council.
While the concept holds extraordinary potential, it also presents significant challenges. This article explores the computational, connectivity, and regulatory hurdles shaping the future of the industrial metaverse and how industrial equipment suppliers like Foxmere are positioned to bridge the gap between current practices and digital innovation.
The industrial metaverse expands on familiar technologies like digital twins, augmented reality, and blockchain, which have been in use for over a decade. However, Siemens’ initiative goes beyond merely replicating physical systems. By leveraging advanced manufacturing insights and the support of industrial equipment suppliers, the company aims to create a dynamic and intelligent ecosystem that transforms manufacturing processes.
Although the vision is ambitious, questions remain about whether these investments will deliver the expected outcomes.
The industrial metaverse represents a shift from entertainment-oriented virtual spaces to precise simulations of industrial equipment and processes. This transformation not only promises to optimise operations but also highlights the essential role of suppliers in ensuring seamless implementation. By visiting the Foxmere website, manufacturers can explore solutions that enhance operational efficiency and prepare for a metaverse-driven future.
Despite its potential, the industrial metaverse remains a work in progress with extraordinary possibilities yet to be fully realised.
Revisiting Familiar Technologies
Technologies such as digital twins, augmented and virtual reality (AR/VR), blockchain, and virtual commissioning have been integral to the industrial sector for over a decade. These tools enable simulations, optimise workflows, and improve operational efficiency.
Siemens’ approach, however, goes beyond merely replicating physical systems. By integrating these technologies into a dynamic and intelligent ecosystem, Siemens aims to transform manufacturing processes. This vision includes real-time adaptability, predictive insights, and the seamless interplay of AI-driven components across manufacturing systems.
Despite these advancements, the journey toward a fully realised industrial metaverse is fraught with challenges. Significant uncertainties exist regarding the integration of these technologies, scaling them across diverse industries, and achieving the ambitious goals Siemens has set. Such hurdles emphasise the need for ongoing innovation and collaboration in the industrial sector.
Understanding the Industrial Metaverse
The term "metaverse" has traditionally been associated with an entertainment-focused 3D internet, offering immersive virtual environments for gaming and social interactions. However, in the industrial context, the metaverse represents a transformative shift toward precise simulations of industrial equipment and processes.
These simulations allow industries to optimise operations without the need for real-world disruptions. For example, manufacturers can test changes to production lines in a virtual space, minimising downtime and errors. Additionally, the industrial metaverse fosters improved collaboration among teams, enabling remote workers and frontline employees to engage in interactive training sessions within virtual environments.
Despite its extraordinary potential, the industrial metaverse remains a work in progress. As technologies evolve and industries adapt, the promise of a fully integrated, AI-powered virtual ecosystem grows closer to reality, though significant challenges still need to be addressed.
The Interoperability Challenge
One of the most significant hurdles in realising the industrial metaverse lies in data integration. Even at the plant level, industries face challenges in connecting disparate systems, often relying on patchwork solutions to achieve limited interoperability. The introduction of metaverse technologies further compounds this complexity, requiring a seamless integration of advanced tools and platforms across varied industrial ecosystems.
Interoperability is crucial for the metaverse to function as intended. It enables the seamless exchange of data between systems, people, and processes, allowing for real-time collaboration and decision-making. Without standardised data formats and integration protocols, these connections remain fragmented, limiting the metaverse's potential impact.
A practical example of interoperability in action can be seen in predictive maintenance. By leveraging AI and digital twins, industries can analyse sensor data from physical equipment and its virtual counterpart to predict potential issues. This system can then schedule maintenance automatically, reducing downtime and preventing costly disruptions. Achieving this level of efficiency requires robust, interoperable frameworks that connect every element within the industrial metaverse.
Regulatory Changes
The development of the industrial metaverse hinges on the establishment of robust standards. Unlike the early days of the internet, which benefited from foundational frameworks like HTML and TCP/IP, the metaverse currently lacks a unified set of protocols to guide its growth. This absence of standards presents significant challenges in achieving seamless integration and interoperability across platforms and technologies.
European regulatory efforts are already addressing some of these issues. Initiatives such as the Digital Services Act (DSA) and the Digital Markets Act (DMA) aim to promote fair competition and prevent anticompetitive practices among digital platforms. These regulations indirectly benefit the industrial metaverse by encouraging data sharing and interoperability across diverse systems and services.
Looking ahead, the industrial metaverse will require regulatory frameworks that ensure safety, fairness, and universal compatibility. Such standards will not only facilitate smoother integration of technologies but also foster trust and collaboration among stakeholders, paving the way for a more connected and efficient industrial future.
Role of Open Source in Collaboration
Open source plays a pivotal role in fostering innovation within the industrial metaverse. By making source code publicly available, open-source initiatives encourage collaborative development and the integration of cutting-edge technologies such as AI, blockchain, and spatial computing. This approach empowers developers and organisations to build upon existing frameworks, introducing new features and rapidly adapting to emerging technological needs.
The benefits of open source extend beyond innovation. It facilitates standardisation, providing a common foundation upon which diverse stakeholders can collaborate. This, in turn, accelerates the evolution of metaverse technologies, ensuring they remain adaptable and aligned with industry demands.
To unlock the full potential of the industrial metaverse, it is essential to promote open-source collaboration across all stakeholders, including technology developers, manufacturers, and regulatory bodies. By pooling resources and expertise, the metaverse community can drive forward solutions that benefit the entire ecosystem, fostering a future where interoperability and innovation thrive.
Adopting an open-source approach can enhance the industrial metaverse by promoting interoperability and facilitating data sharing across diverse platforms and services.
Practical Steps for Manufacturers
As the industrial metaverse evolves, manufacturers must focus on immediate priorities to remain competitive. Upgrading existing processes and integrating digital technologies are essential steps toward building a foundation for future innovations. This transformation requires strategic planning and partnerships with trusted suppliers who can deliver the necessary tools and components.
Foxmere plays a crucial role in this transition by providing high-quality programmable logic controllers (PLCs) and other industrial parts. These components are essential for manufacturers looking to digitise their operations, enabling seamless data collection and management across systems.
By sourcing parts from Foxmere, manufacturers can begin bridging the gap between physical and digital realms. This not only enhances operational efficiency but also lays the groundwork for adopting advanced metaverse technologies, ensuring a smoother transition into a digitally interconnected industrial landscape.
Conclusion
The industrial metaverse holds transformative potential, promising to transform manufacturing and industrial processes. However, its full realisation remains a long-term goal, with significant challenges in interoperability, regulatory frameworks, and technological integration still to be addressed.
Manufacturers can prepare for this future by focusing on optimising their current systems and embracing incremental digital advancements. By taking these steps, they can build a strong foundation that supports a seamless transition into the metaverse era.
For assistance with digital technologies or sourcing industrial parts, Foxmere is here to help. Contact our team today to explore how we can support your journey toward a digitally interconnected future.
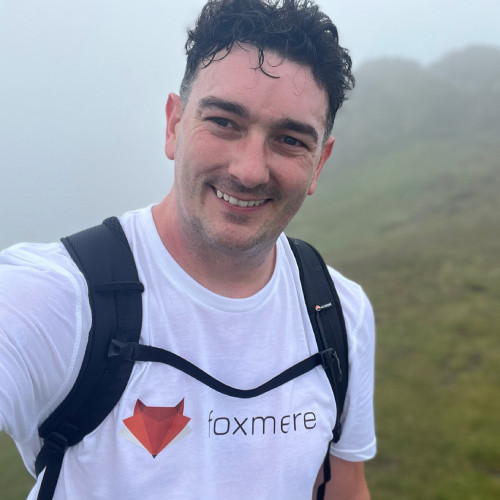