Tin Whiskers in Space Electronics: Causes, Effects, and Mitigation Strategies
Technical Analysis | 31-01-2025 | By Jack Pollard
This article was written by Daniel Theis - Technical Manager at Rhopoint Components.
The removal of lead from electronic components has been an ongoing process since the late 1990s, driven by environmental and health concerns. Subsequently, regulations formalising the process were introduced, such as the Restriction of Hazardous Substances Directive (RoHS), which restricted the use of six hazardous substances, including lead, in electrical and electronic equipment sold in the EU, and the WEEE Directive, which covers waste management and recycling of electronic devices.
Fig 1 – High Density PCB
The electronics industry has largely moved to using lead-free solder alloys, such as tin-silver-copper (SAC), bismuth-tin, or tin-copper, and coating materials such as nickel-gold or palladium. Manufacturing processes have had to be changed to accommodate lead-free materials, as lead-free solders have higher melting points.
The Risk of Tin Whiskers in Electronic Systems
Lead-free soldering is now commonplace but introduces some reliability issues, such as increased brittleness and the risk of tin whiskers. Tin whiskers are hair-like metallic filaments that grow from tin-rich surfaces, creating risks including short circuits that lead to equipment failure.
While not seen as a particular problem for earth-bound commercial and industrial applications, where they can grow at rates of 0.03–9 mm per year depending on stress and environmental conditions, studies suggest whiskers may grow faster in space due to vacuum conditions, radiation-induced stress, and thermal cycling.
Fig 2 – Example Tin Whisker
Image used with the permission of IFA (Institute for Occupational Safety and Health of the German Social Accident Insurance)
Mitigating Tin Whisker Growth
Tin whiskers pose a significant issue in high-reliability systems such as aerospace, medical, and defence electronics, where they can cause equipment failures due to intermittent or permanent short circuits between contacts or PCB tracks.
Various techniques can reduce the risk of tin whiskers, including:
- Improving the plating process or annealing to reduce internal stress.
- Introducing alloying additives in the solder to inhibit whisker growth.
- Applying a conformal coating to block whisker development.
However, none of these procedures completely eliminate the risk, making it necessary for high-reliability electronics to undergo rigorous testing and validation.
Why Lead Solder is Still Used in Space Electronics
The long history and demonstrated reliability of lead-based solder make it a continued choice for critical electronic systems, particularly in space, defence, and medical applications.
Key advantages of lead solder include:
- Suppresses tin whisker formation, reducing the risk of electrical failures.
- Withstands extreme temperature fluctuations better than lead-free alternatives.
- Less sensitive to radiation-induced degradation in space environments.
- Minimal outgassing properties in a vacuum, reducing contamination risk.
- More resistant to stress fractures and cracking, ensuring long-term reliability.
While development of lead-free alternatives is ongoing, lead solder remains the standard for mission-critical space applications where failure is not an option.
Fig 3 – Example Tin Whisker
Image used with the permission of IFA (Institute for Occupational Safety and Health of the German Social Accident Insurance)
The Role of High-Reliability Components in LEO Satellites
The exponential growth of Low Earth Orbit (LEO) satellites is increasing demand for reliable electronic systems. Projects such as SpaceX’s Starlink, with plans to launch approximately 42,000 satellites, highlight the rapid expansion of the LEO satellite market.
Since satellites cannot be repaired or serviced after launch, system reliability is paramount. Every component must be qualified for space environments to prevent failures that could result in financial losses and disrupted services.
Ensuring a Secure Supply Chain for Space Electronics
Companies manufacturing space-qualified electronic systems must not only source appropriate components but also stay informed about changes in manufacturing processes.
Managing the entire bill of materials (BOM) is a major logistical challenge, requiring close monitoring of:
- New product developments in electronic components.
- Changes in industry standards and regulations.
- Obsolescence and supply chain risks.
The Value of Specialist Distributors
Working with a specialist distributor helps OEMs secure reliable, qualified components from a single trusted source. Distributors provide:
- Access to the latest market intelligence about new materials, product innovations, and regulatory changes.
- A streamlined supply chain, reducing production delays.
- Support for custom component designs and COTS (Commercial Off-The-Shelf) alternatives where applicable.
Rhopoint Components: Supporting High-Reliability Electronics
Rhopoint Components is an authorised partner for over 25 industry-leading manufacturers, offering:
- A broad range of stocked electronic components and fully customised solutions.
- Technical and logistical expertise for complex projects.
- Efficient UK-based sales and distribution operations to support global customers.
To explore Rhopoint Components' extensive range of space-qualified electronic components, visit www.rhoointcomponents.com.
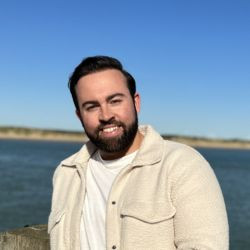