Recycling Challenges the Electronics Industry to Clean Up its Act
24-09-2018 | By Mark Patrick
The progress made in phone handsets and other forms of consumer electronics over the past two decades has led to impressive technological capabilities being realised. The processing speed available to users of iPhone X smartphones can rival that of a modern laptop computer.
Thanks to the rapid pace of development, owners of smart devices have become used to upgrading them regularly. They will swap to a new model every two years if not sooner. The question is - what happens to the old devices? Ideally, electronic hardware would be recycled, but the reality remains a long way from that utopia. Discarded electronic products often just join the growing mountains of e-waste.
More than 15 years ago, the EU introduced the Waste Electrical and Electronic Equipment (WEEE) directive in an attempt to prevent old electronics equipment, which often contains hazardous elements (such as heavy metals) going to landfill. The WEEE directive placed the responsibility for ensuring the recycling of electronics items made after 2005 on manufacturers themselves and introduced national targets for collection, recycling and recovery. The initial minimum target for recovery was 4kg per head of population each year by 2009. A 2012 revision, with a transition period of seven years, increased the target for recovery and recycling. The aim was to have 85% of all electrical and electronic waste recycled by 2016.
In a project conducted for the EU, the Countering WEEE Illegal Trade (CWIT) project found that in Europe only 35% of all the e-waste discarded in 2012 - amounting to more than 3 million tonnes - went through collection and recycling systems that complied with reporting requirements. Another 35% was recycled under non-compliant conditions and a further 1.5 million tonnes was simply exported.
Worldwide expansion in the use of electronics has seen developing nations in Africa and Asia become the chief destinations for large quantities of e-waste. A number of these countries have now taken action to try to stem the flow. China has banned the import of e-waste, while the country seeks to deal with its current mountain of discarded electronics. As the crackdown on e-waste continues, the industry will need to look much more closely at how it deals with the problem.
In most cases today, e-waste is recycled into raw materials. One common practice is to strip components from printed circuit boards (PCBs) and recycle the copper and other metals they contain. To some extent, the components themselves can also be recycled. In many cases the components are shredded in industrial recycling plants and then processed to try to recover precious metals, such as the gold that is used in bondwires and connectors, as well as copper, iron and various other elements.
A key problem in the recycling of e-waste is that most products have not been designed to be recycled easily - they were designed primarily for form, function and durability. De-soldering components from a PCB takes large amounts of energy and can be damaging to the devices themselves, as they are often only meant to survive those high temperatures during manufacture. Novel production technologies may help the situation and facilitate the easier separation of reusable components from those that need to be recycled into raw materials. For example, passive components, such as ceramic capacitors, inductors and resistors, could potentially be recovered and resold if they were easier to separate from the PCB.
To address the problem of de-soldering, the National Physical Laboratory (NPL), together with partners In2Tec and Gwent Electronic Materials developed a PCB bonding technology that allows the components to be separated simply by immersing the whole assembly in hot water. For this project, the partners designed, developed and tested a combination of polymers, deposited in layers, that can cope with thermal cycling and damp heat stressing but which ‘unzip’ after hot water immersion. According to NPL, the technology would allow as much as 90% of the original structure to be re-used. In contrast to conventional solder-based technology, the polymer-based approach lends itself to novel 3D structures on both rigid and flexible substrates - thus enabling the electronics industry to pursue new design approaches.
An alternative to recycling that involves less chemical-based processing is upcycling. Under this regime, subsystems that still work are incorporated into different products and sold to new users. In practice, such upcycling is difficult to achieve. The chief obstacle here is the rapid pace of advancements in electronics - both in terms of performance and the costs involved. It is often more cost-effective to source new subsystems for a design rather than attempting to rework existing designs - which may not be available in sufficient volume to suit their new purpose. As the cost scaling enabled by Moore’s Law slows down and may even come to a halt, upcycling might become a more viable option.
Some attempts at upcycling have succeeded on a small scale. For example, UK charity TechforTrade has been instrumental in developing a 3D printer that can be made from recycled e-waste and which uses recovered plastic waste for its feedstock. Using the Retr3d printer as a key component, TechforTrade has begun to create a global ‘Digital Blacksmiths Network’. The goal of the network is to alleviate poverty and push for economic growth through open-source product development and the provision of localised manufacturing based on 3D printing. Rather than transport goods physically, the designs are conveyed digitally and use local resources and knowhow for fabrication.
Figure 1: TechforTrade's Retr3d printer.
Localised manufacture is being used to support an upcycling initiative based on batteries recovered from electronics products. UK-based start-up Acceleron has developed a number of technologies that can be utilised to repurpose old batteries and place them into modular designs that are more suitable for recovery when the batteries are finally no longer able to hold a charge effectively.
An important aspect of Acceleron’s approach is its focus on micro-fabrication. The company says that it is becoming increasingly important to build batteries closer to where the energy is needed as supply chains shorten. As an example, the company (aided by the Shell Foundation) has helped put lithium-ion battery pack production into operation at a local level in Nairobi, Kenya. The micro-fabrication facility started running in April this year, producing 124 functional advanced lithium-ion batteries within one week from start to finish using minimal equipment and no specialist training.
Modularity and upgradeability provide ways to keep products in use and support upcycling, although in the quest for miniaturisation, the trend has to be to make electronics less easy to repair and upgrade. With a modular design, as processor or display technologies improve, each can be upgraded in turn rather than demanding that users replace a complete system with an entirely new version.
Figure 2: The Fairphone 2 smartphone handset.
One attempt to develop a greener smartphone using these principles is the Fairphone 2. Its modular design allows subsystems such as the display, cameras, battery and antennas and the processor core itself to be swapped out and upgraded over time. The manufacturer, Fairphone, claims the usable lifetime of the device is of the order of five years, rather than the one or two years of most conventional smartphone designs. Eventually, the modules will become unusable but the design approach could assist recycling efforts. Fairphone carried out a study of recycling techniques that included component shredding and disassembly before passing individual subsystems to recycling. An issue with shredding is that it tends to mix materials to a level that makes it difficult to recover some metals. The study concluded a modular design is more likely to lead to improved raw-materials recovery.
Before being acquired by Facebook in mid-2016, start-up Nascent Objects worked on a more general-purpose approach to the creation of modular electronics. The platform was founded on the basis that most consumer electronics products consist of similar modules that make it feasible to develop mix-and-match designs. Peripherals, such as cameras or speakers, can be replaced without needing to buy an entirely new product. Nascent Objects developed 15 interchangeable modules to enable customisation and upgradeability, and the option to have the older modules reused in other products. The company’s software would analyse the modules required and develop a 3D printing file to create the frame or shell.
Although the electronics industry remains at a very early stage in terms of thinking about reusability and recycling, the emergence of start-ups focused on this space and increased attention to the environmental cost of the existing approach is likely to lead to change. That will mean change not just to the recovery infrastructure, but also to the way in which electronics systems are designed - with a much greater focus on aspects such as modularity, upgradeability and reuse.
Read more electronics news related to phone technology: Wireless charging. It doesn’t really do what it says on the tin
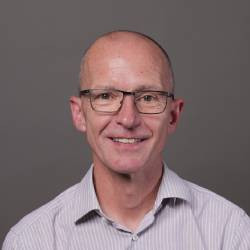