Collaborative robots (Cobots) move into the human workspace
02-10-2018 | By Nnamdi Anyadike
The market for collaborative robots, so-called ‘cobots’ that work alongside human operators, is expanding fast and looks set to render the future industrial workplace unrecognisable in the coming years. Universal Robots, the Danish producer of robotic arms and a major player in collaborative robotics, expects the cobot market to exceed $4 billion by 2023. Loup Ventures meanwhile, the US based venture capital firm, predicts that global robotics spending will reach $13 billion in 2025. By then, cobots are expected to rise from their current 3% share of all robot sales to reach 34%.
So what exactly is driving this growth? Industrial robots have long become ubiquitous in the industrial workplace. Cobots though are much more sophisticated than these earlier ‘first generation’ robots and come equipped with extra built-in safety features and sensors. This allows them to assist in fine motor tasks like welding that must be done in situ. It also allows them to transport cargo without risk of injuring their human ‘colleagues.’
According to a recent B2B industry report, the highest CAGR is expected for cobots with a payload capacity above 10 kg. This is mainly attributed to the expected demand for high-payload-capacity in industries such as automotive, furniture and equipment, and metals and machining. However, the market, which is dominated by a few players including Universal Robots, FANUC Corporation (Japan), KUKA AG (Germany), and MABI AG (Switzerland), is still in its infancy and growth will come from a very low base.
In September 2018, Universal Robots announced the sale of its 25,000th cobot to Kay Manufacturing, thereby cementing its 60% market share. Universal Robots has entered into collaboration with Soft Robotics Inc., based in Cambridge, Massachusetts. This company manufactures soft end effectors for robots that require more dexterity. As part of their alliance, Soft Robotics has developed the first plug-and-play customisable gripper system for Universal Robots.
Commenting Anders Bo Rasmussen, Senior Product Manager at Universal Robots said, "Our goal is to make Universal Robots easy for our customers to implement in any industry, for any application. Soft Robotics shares this same philosophy, and bringing Soft Robotics technology to Universal Robots is a great solution for our customers looking to automate processes that require manipulation of items with the same dexterity as a human hand." The alliance follows similar technology partnership, including a three-way merger that has brought together: Perception Robotics (US); OptoForce (Hungary); and OnRobot (Denmark).
In other developments, Vanderlande the Netherlands provider of logistic process automation has developed a cobot in partnership the Finnish assembly company Würth Oy and its logistics software partner, Leanware Oy. The Cobot is operating as part of a pilot project at Würth’s logistics centre in Riihimäki, north of Helsinki.
In a statement Terry Verkuijlen, VP of Warehousing and Parcel at Vanderlande said, "This pilot will provide us with valuable insights into the evolution of robotics. Thanks to the logistical know-how in Finland and the close partnership with Würth, Riihimäki provided an ideal environment to bring SIR [Smart Item Robotics] to life. Of course, development is still in its infancy and we need to proactively monitor the situation and work closely with Würth and Leanware to further optimize SIR capabilities."
SIR has been integrated into Würth's daily operations, along with ‘ADAPTO’, Vanderlande's flexible storage/retrieval and transport system. The entire process is controlled by the same Leanware system interface that is also used for other processes in the Riihimäki logistics centre. Terhi Vesala, Logistics Manager at Würth explained, "First of all, we check which type of products the Cobot is suitable for, how the picking process improves and how the work can best be divided. In short, we want to see what this robot can actually do."
But as Charles Towers-Clark writing in Forbes points out robots working alongside humans can still present their own unique set of dangers. In 1981, a maintenance engineer working in a Kawasaki plant was crushed to death by a robot’s hydraulic arm. And more recently in 2015, a robot in a Volkswagen plant ‘mistook’ a worker for a component and crushed him against a metal plate. The US Occupational Safety and Health Administration identified 27 fatalities associated with robots from 1984 to 2013.
Nonetheless, recent advances in safety mechanisms are managing to allay some of these fears. Safety features include, “the requiring of manual authorisation in certain situations, sophisticated sensors to identify humans in the vicinity, and strict instructions to err on the side of caution are now commonplace, allowing robotics companies to slowly but surely persuade us that cobots aren’t so bad,” says Forbes. The future industrial workforce will expect nothing less.
Read more electronics news related to collaborative robot technology: Cobots – Bridging the AI Gap for Industrial Automation
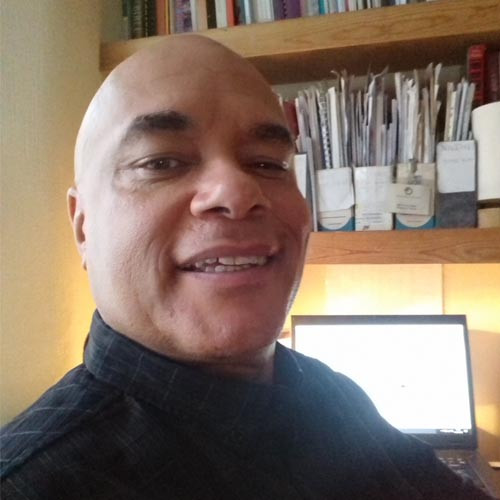