AI-enabled sensors developed for precision cutting tools
29-11-2021 | By Robin Mitchell
Recently, researchers from the University of Bath have been awarded £1.5m to develop precision tools for the machining industry to utilise sensing technologies. What challenges does the precision machining industry currently face, what will the researchers develop, and what other developments could such sensing technology lead to?
Why precision tools are problematic?
When it comes to machining, large portions of the industry require sub-millimetre precision, which is relatively easy to achieve. The use of stepper motors with gear ratios and micro-stepping allows for very fine control, while homing sensors can ensure that tools always return to a well-defined home. However, some industries require incredibly tight tolerances, which are simply not possible to achieve with everyday off-the-shelf parts and equipment. One example would be equipment found in the aerospace industry which may require parts needing precision in the microns.
In these cases, the tools and equipment used to produce such parts must be well maintained and frequently tested to ensure their repeatability and accuracy. Tooling machines must frequently change out tooling bits involved with drilling and cutting as wear and tear will result in a loss of precision in the final product. But the frequent replacing of cutting tools can be very expensive considering that only precision cutting tools can be used. This cost factor is made worse when considering that cutting tools are often discarded well before their end-of-life.
Precision parts are expensive to produce by their very nature, but throwing away perfectly usable cutting tools only adds to this cost. Reducing the cost of tooling can allow for more precision parts to be manufactured, reducing the cost of precision parts. But how does a machine operator determine if a cutting bit is still acceptable to use?
Researchers granted funds for developing smart tools
Recently, researchers from the University of Bath have been awarded £1.5m to research and develop precision tools with intelligence built directly into them. According to the researchers, as much as 4% of manufacturing costs in the aerospace industry come from replacing tools early, and integrating sensors into such tools could help to eliminate this cost entirely. Manufacturing large parts (such as landing gear) while retaining precision increases costs exponentially to make matters more complex. An industry that spends over $34bn a year on cutting tools could see significant savings worldwide.
As the research has only just started, there is no telling how the researchers will achieve the goal of incorporating advanced sensing capabilities into cutting bits. Some cutting tools already incorporate sensors, but what is currently unavailable is data models and algorithms (such as those powered by AI) that can read the data from a cutting tool and make an informed decision on the current condition of the tool. Furthermore, the researchers are looking to develop a range of sensors aimed at machining that will improve quality while minimising cost implications.
What other developments could tool sensing technologies see?
Tools that have inbuilt sensors could be used for far more than just determining the current condition of the tool. Vibration data detected in the tool could be used for determining the condition of the machine that is using the tool, while accelerometers could be used to determine if the tool is correctly centred.
Combining sensor data from a cutting tool with AI also provides predictive capabilities which can make more accurate determinations as to the condition of the bit and when it should be replaced. During use, constant monitoring by AI can provide a real-time indication of bit condition, eliminating the need for bit replacement based on time.
Data from the cutting tool can also be fed back into the machine to determine its true position, improving its precision. Most cutting systems are dependent on the use of encoders on-axis to determine where the position of the head is, but a cutting head with sensors would be able to determine its position relative to a workpiece from reactionary forces as it makes contact.
Cutting tools can be stationary (such as those found in lathes), but most cutting tools are rotary when used with multi-axis milling machines. As such, integrating sensors into these bits will require advanced engineering techniques, including power transmission to the sensor found in the bit, information linking between the bit and the machine in real-time, and the ability for any electronics inside the bit to withstand large g forces. Potentially, the sensors may be attached to the machine and utilise data acquired to determine the bit status. Either way, precision machining could soon become cheaper if researchers can achieve practical smart cutting tools.
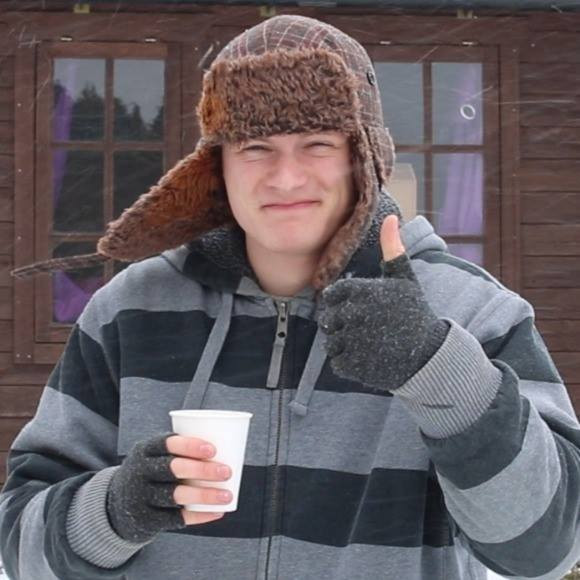