Panasonic's Copper Clad Stretch for Flexible Electronics
04-10-2023 | By Robin Mitchell
PCBs have been foundational in electronics, but their rigid nature limits their use in flexible designs. Panasonic's recent development of the Copper Clad Stretch aims to address these limitations. This article explores the challenges PCBs face in flexible electronics, Panasonic's innovative solution, and its potential applications.
What challenges do PCBs present in flexible electronics?
Just like how bricks are the foundation of a home, PCBs are the foundation for all modern electronics. They have enabled engineers to create complex circuits, reduce circuit sizes, and simplify mass production processes. Before PCBs, electronics were built by hand, mounted onto large pieces of wood, and each component was individually wired. However, with the rise of flexible electronics, the rigidity of traditional PCBs based on fibreglass and epoxy has become a limitation.
So, it goes without saying that PCBs have made a massive impact on electronics and, by extension, every industry that has been touched by electronics. But for all the benefits that PCBs provide, the emergence of new markets and applications is pushing PCBs to their limits and, in some cases, demonstrating how current PCBs are simply not up to the task.
One such area where PCBs face challenges is in the flexible electronics industry, particularly when it comes to accommodating the dynamic needs of wearable devices and bendable screens. In these applications, electronic circuits must adapt to uneven and organic surfaces. While components can be made small enough to not be affected by such motion, PCBs based on fibreglass and epoxy simply cannot handle such mechanical stress.
While the existence of flexible PCBs isn't new, the majority are based on polyamide resins. But what's the issue with these resins? This means that they are not ideal for extreme flexing and stretching in wearable applications. Getting around this can be done with the use of thermoplastics such as polyurethane, but their inability to handle high temperatures makes them unsuitable for reflow soldering.
Figure 1 illustrates a comparative analysis between currently available FPC materials, including polyimide and TPU, and a prospective ULTRA flexible circuit board.
However, as the demand for more conformable circuits grows, especially in wearables, there's a clear need for materials that can offer more flexibility without compromising on other essential properties.
Panasonic unveils new copper laminate substrate for flexible applications
In response to the industry's shift towards more wearable and flexible devices, Panasonic has recently unveiled the Copper Clad Stretch (CSS). This groundbreaking substrate withstands bending, twisting, and stretching without damage and is compatible with standard reflow soldering. The CCS technology addresses the stiffness of polyimide and the heat durability issues of TPU, making it a promising solution for the next generation of flexible electronics.
Panasonic's CCS material is a unique blend of a PET protective film, uncured resin, and a polyamide-release liner. This composition allows for versatility; the resin can be fully cured for rigidity or remain uncured for flexibility. The polyamide layer ensures mechanical support during soldering processes, making CCS both bendable and stretchable, setting it apart from traditional copper clad laminates.
CCS's Role in 6G Communication and Beyond
The CCS material, with its stretchable nature, has shown immense promise in 6G communication. Researchers from Osaka University have leveraged it to craft a reconfigurable intelligent surface (RIS) for the 140GHz bands. This addresses the challenges posed by high-frequency radio waves, such as obstructions from buildings. Moreover, the ability to dynamically control the reflection direction of these waves offers solutions to challenges in non-line-of-sight environments, prevalent in high-frequency scenarios. As the 6G landscape continues to evolve, CCS's innovative properties could be pivotal in ensuring more reliable and adaptable communication systems.
However, as the demand for more conformable circuits grows, especially in wearables, there's a clear need for materials that can offer more flexibility without compromising on other essential properties.As highlighted in a report from TechBlick, "The CCS technology, with its innovative approach, addresses the stiffness of polyimide and the heat durability issues of TPU. This makes it a promising solution for the next generation of flexible electronics."
Furthermore, the CCS technology has been tested for its heat durability under typical SAC reflow conditions and showed impressive resilience. This heat resistance, combined with its pliability, makes CCS a game-changer in the realm of flexible electronics, paving the way for its adoption in wearable technologies and other innovative applications.
Finally, the new clad material developed by Panasonic was put through standard PCB processes, including pattern plating, drilling, and lamination. Again, the material held up perfectly throughout the process, and the polyamide release layer provided mechanical stability during STM processes.
At the renowned Apex 2023 event, a significant platform for the electronics manufacturing industry, Panasonic presented a technical paper that further emphasized the advancements in pliable circuit board technology. Tomohiro Fukao, the Research Manager of Panasonic's Electronic Materials Division, highlighted the transformative journey from traditionally rigid PCBs to the innovative soft, flexible substrates that Panasonic is pioneering.
What applications could be helped with the new copper clad?
Researchers suggest the new material could be used for advanced mobile antenna applications that need to direct and manipulate radio energy. Because future mobile networks will undoubtedly use high-frequency radio waves, advanced techniques for direction radio waves will become essential, and flexible PCBs that can be mechanically manipulated will be highly beneficial.
The newly developed substrate will also be highly beneficial in the creation of reliable electronics in wearable applications. As the substrate can be stretched and manipulated, it is possible to create flat circuits that are then formed around a particular three-dimensional shape and then cured. Not only does this allow for the creation of unique circuits, but it also decreases the complexity of fabricating 3D circuits.
The new copper-clad stretch material opens up a myriad of possibilities. As we navigate the early stages of wearable electronics, the commercial viability and indispensability of such materials are on the horizon.
Indeed, advancements in materials like CCS are ushering in a new era of innovative applications in the electronics domain. With the continuous evolution of these materials, the future promises even more revolutionary developments.
Specifically, in the realms of wearables and 6G communication, CCS is poised to be a cornerstone, reshaping the electronics landscape.
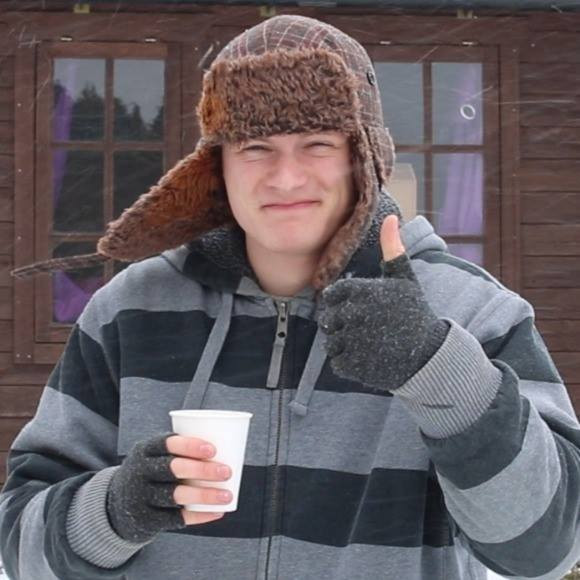