How to Decide: Surface Mount or Through-Hole Technology?
15-04-2024 | By PCBWAY
Key Things to Know:
- Technology Overview: Understand the fundamental differences between Surface Mount Technology (SMT) and Through-Hole Technology (THT) and how they impact the assembly of electronic components on PCBs.
- Production Efficiency: Explore how SMT can enhance production speed by up to 25% and reduce costs by 30%, making it a preferable option for mass production scenarios.
- Design Considerations: Learn about the importance of choosing the right PCB technology based on component size, density, and the mechanical stability required for your application.
- Cost Implications: Delve into the cost differences between SMT and THT, understanding why each might be more cost-effective depending on your project's scale and complexity.
When it comes to assembling electronic components onto Printed Circuit Boards (PCBs), one of the fundamental decisions engineers and designers face is choosing between Surface Mount Technology (SMT) and Through-Hole Technology (THT). Each method offers its own set of advantages and considerations, and selecting the right approach can significantly impact the performance, cost, and manufacturability of a product. In this article, we delve into the key factors to consider when deciding between SMT and THT.
Recent trends in electronics manufacturing show a significant shift towards Surface Mount Technology (SMT) due to its efficiency in scaling production. A case study by PCBWay revealed that switching to SMT led to a 25% increase in production speed and a 30% reduction in costs for a consumer electronics project, illustrating the critical economic impact of this technology choice.
Understanding SMT and THT
Surface Mount Technology (SMT) involves mounting electronic components directly onto the surface of the PCB, where they are soldered in place using solder paste and a reflow soldering process. This method eliminates the need for component leads to pass through holes in the PCB, allowing for smaller, more compact designs and increased component density.
It's important to note that SMT allows for a higher number of components per unit area, enhancing the functionality of devices without increasing their size. This compact arrangement is pivotal for modern high-tech devices such as smartphones and tablets, where space efficiency is paramount.
On the other hand, Through-Hole Technology (THT) involves inserting component leads through holes drilled into the PCB and soldering them onto the opposite side of the board. This method provides mechanical stability and reliability, particularly for components subjected to mechanical stress or high currents.
This robust mechanical connection makes THT indispensable for products that must endure harsh environments. For example, industrial and automotive sectors predominantly use THT to ensure long-term reliability under extreme conditions.
Key Considerations
The choice between SMT and THT not only affects the physical attributes and potential applications of the PCB but also influences other critical factors such as production timelines and overall project costs. It is crucial for designers to balance these considerations with the functional requirements of the electronic device. For instance, SMT might be the preferred option in consumer electronics where the demand for compact size and high-density circuitry is high, whereas THT might be favored in industrial applications where durability and ease of repair are priorities. Understanding these nuances can help in making an informed decision that aligns with both technical needs and business strategies.
Component Size and Density
SMT excels in applications where space is limited, as it allows for smaller, more densely packed components. THT may be preferable for larger components or applications where component size is not a limiting factor.
Assembly Process
SMT assembly is typically faster and more automated, making it suitable for high-volume production. THT assembly may require manual soldering of through-hole components, leading to longer assembly times and higher labour costs.
While SMT can significantly reduce the physical footprint of circuits, it sometimes requires additional considerations such as thermal management due to the close packing of components. This aspect is particularly crucial in high-power electronics where thermal efficiency can influence system reliability.
Mechanical Stability
THT offers greater mechanical strength and durability, making it suitable for applications subjected to vibration, shock, or thermal cycling. SMT components, being surface-mounted, may be more susceptible to mechanical stress and may require additional reinforcement or conformal coating for added durability.
Moreover, for products subjected to regular mechanical vibrations such as in automotive or aerospace applications, THT provides unmatched durability that SMT might not be able to match without supplementary structural supports.
Signal Integrity
SMT components have shorter electrical paths, reducing parasitic capacitance and inductance and improving high-frequency signal integrity. THT components may introduce more parasitic effects, particularly for high-speed digital or RF applications, but proper design techniques can mitigate these effects.
Additionally, the shorter leads in SMT components reduce not only the signal path but also the overall noise levels, which is crucial for maintaining the integrity of high-speed signals in advanced communication devices.
Cost
SMT assembly generally requires fewer materials and less manual labour, resulting in lower manufacturing costs for high-volume production. THT assembly may be more cost-effective for low-volume or prototype runs, as it may not require specialised equipment or processes.
When deciding between SMT and THT for a particular application, it's essential to carefully evaluate the specific requirements and constraints of the project. Consider factors such as space limitations, component size and density, assembly volume, environmental conditions, and budgetary constraints.
Additionally, consulting with experienced PCB designers and manufacturers can provide valuable insights and guidance in selecting the most suitable assembly method for your needs. Conducting thorough testing and validation of the chosen approach is also crucial to ensure the reliability and performance of the final product.
For those looking to explore the possibilities of PCB manufacturing and assembly, PCBWay offers a comprehensive range of services tailored to meet various needs. With state-of-the-art facilities and a team of experienced professionals, PCBWay is committed to delivering high-quality PCBs with quick turnaround times at competitive prices.
Whether you require SMT or THT assembly, PCBWay has the expertise and resources to bring your designs to life. From prototype development to mass production, PCBWay provides end-to-end solutions to help you realise your projects efficiently and cost-effectively.
In conclusion
The choice between Surface Mount Technology (SMT) and Through-Hole Technology (THT) is a critical decision in the design and manufacturing of electronic products. Each method offers unique advantages and considerations, and selecting the right approach requires careful analysis of factors such as component size, assembly process, mechanical stability, signal integrity, and cost. By understanding the strengths and limitations of SMT and THT and considering the specific requirements of your project, you can make an informed decision that optimises performance, reliability, and cost-effectiveness with the support of PCBWay's expertise and services.
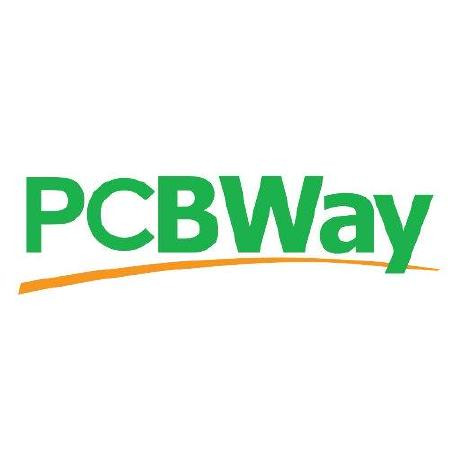