Automation robotics playing key role in the packaging industry
19-12-2018 | By Nnamdi Anyadike
The packaging industry has long favoured automation. However, a recent study from Quest TechnoMarketing, the German based specialist in market research and marketing for automation, shows that the intensity of automation technology in the packaging sector is now increasing at an accelerated rate. By 2020 and beyond, the market share of all electronic drive technology on packaging machines, including the use of robots, servos, DC drives and linear drives such as torque motors will have grown almost beyond recognition.
Malte Schlüter, a global key account director at Mitsubishi Electric, has identified four main trends that are currently influencing the packaging industry and will go on to shape the future. These include: collaborative robots; robots without protective barriers; artificial intelligence and data mining. The demand for collaborative robots (cobots) for direct use next to humans without protective equipment is well underway. But as Schlüter says, "This is not about displacing classic industrial robots, but about supplementing them and adding advances in automation - especially in the co-packing sector."
Equipped with a vision system, cobots can relieve people of monotonous, tiring and physically stressful tasks. “Mitsubishi Electric is currently developing a new collaborative robot with features including: no risk of injury from crushing edges and a surface that is easy to clean and prevents dirt traps - while still achieving the same repeat accuracy of ±0.02 mm as our industrial robots. The prototypes are still under testing, but they have already been presented to a wider audience at international shows." He says.
Meanwhile, there is a growing demand for robots that can operate without recourse to safety solutions such as fences, barriers, cages and cells. These safety precautions have the drawback of occupying valuable production space and prevent a meaningful cooperation with workers. Currently, optical safety systems are used to monitor defined zones around the robot. However, instead of a single area being secured with light barriers and laser scanners, ‘entire rooms’ are increasingly being monitored with camera systems. And in the future, vision systems equipped with artificial intelligence (AI) will provide robots with the ability to react appropriately when people enter the workspace by adjusting their work speed.
Mitsubishi Electric is already actively working with its partners to develop practical solutions to this issue. It has also begun to market its new MELFA FR robot series, available with AI functions. This series enables quality defects in packaged products and replaces these with flawless products during the process - even within individual packaging units.
In data mining, Mitsubishi Electric is developing a new cutting edge computing technology called MELIPC. It will be fully commercialized in 2019 and will be used for traceability and consumer information in the packaged food sector. The system will be capable of proving compliance with the cold chain or attaching origin information to food packaging that can be called up via a QR code.
In other developments, the Los Angeles based protein snack bar company has managed to double its production from 150 bars/min to 300/min – with a potential to reach 425 bars/min - through the installation of a new automated packaging line from Bosch Packaging Technology. The key benefits of the automated packaging line include: expanded capacity; enhanced flexibility and consistent results.
And in November, Neopost Shipping, the UK based supplier of shipping software, smart parcel lockers and automated packaging machines, launched its CVP-500 automated packaging solution (APS). The solution is capable of ‘auto-boxing’ multiple or single items at speeds of up to 450 packages per hour. Just one operator is required to produce the high-volume packing throughput that uses 3D imaging of each unique order to determine the minimum box size required. Neopost Shipping has already installed its first application of two CVP-500 machines in the UK and has applications across nine counties.
This year, Proco Machinery Inc., the US manufacturer of automation systems for the blow moulding industry, showcased its cobot systems including the ‘Half-Cube Palletizer system’ and the ‘Robo Packer’ case packer for the packaging industry at industry events. Siva Krish, Vice President of Sales for Proco said that both new products are attracting “broad interest” in the packaging market. He claims that the Half-Cube Palletizer System delivers a 50% cost reduction compared to conventional automation solutions. Proco has already sold a few Half-Cube Palletizer systems to some leading US custom blow moulders of PET containers.
The ‘Robo Packer’ case packer works interactively with co-workers. It requires no special guarding and only needs minimal training for teaching new tasks. It is ideally suited for pick and place, assembly, and packaging applications and it can be supplied with any one of three different robotic arm payloads depending on the application.
Yet despite their inroads, robots summarises Schlüter, “are still far from replacing all manual work in the packaging industry. As fully integrated, intelligent 'colleagues', they will though help to make tasks more comfortable and efficient. This is no longer a dream of the future, because we have the corresponding technology right now - and it is economic to use".
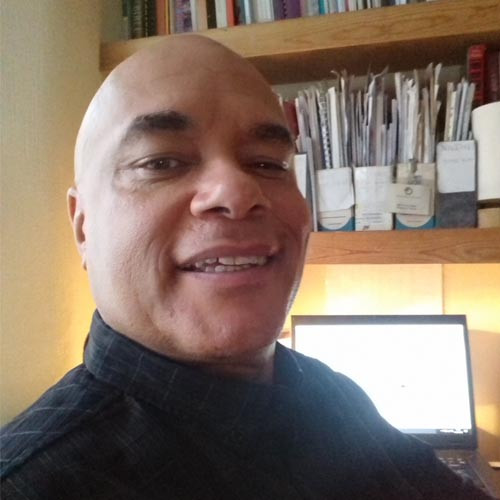