What is Power Electronics: A Comprehensive Guide
06-02-2024 | By Jack Pollard
3D-rendered robotic arm assembling solid-state battery cells
Table of Contents:
- Introduction to Power Electronics
- Definition and Basic Concept
- Historical Development and Evolution
- Key Components of Power Electronics
- Efficiency and Size Considerations
- Heat Dissipation and Thermal Management
- Applications in Various Systems
- Voltage and Frequency Regulation
- Conversion Techniques
- Protection and Safety Mechanisms
- Future Trends and Innovations
- Conclusion
Introduction to Power Electronics
Power electronics is fundamental to modern technology, deeply embedded in a myriad of applications that shape our daily experiences. This specialised area, blending electrical engineering with advanced technology, is crucial in efficiently controlling and converting electric power. From the smallest household devices to large industrial machinery, power electronics ensures that these systems operate optimally, harnessing and manipulating electrical energy to meet diverse needs.
This article will explore the core principles, key components, and the latest advancements in the field of power electronics. We'll examine its impact on various industries and the challenges and opportunities it presents in our rapidly advancing technological world. This overview aims not just to inform but to illuminate the significance of power electronics in our increasingly electrified society.
Definition and Basic Concept
Power electronics is defined as the branch of electrical engineering that deals with the control and conversion of electrical power using solid-state electronics. At its core, it involves managing the flow of electrical energy from the source to the load in an efficient, reliable, and compact manner. This field is distinguished by its focus on handling higher power levels compared to general electronics, which typically deal with lower power signals.
At the heart of power electronics are three key principles: solid-state electronics, power conversion, and control. Solid-state electronics refer to the use of semiconductor devices like diodes, transistors, and thyristors to control and switch electrical energy. Power conversion involves changing electrical power from one form to another, such as AC to DC, DC to AC, or changing the voltage and current levels. Control in power electronics is about regulating the output to meet specific requirements, which can include aspects like voltage regulation, power factor correction, and smoothing of power delivery.
These principles enable power electronics to efficiently manage and convert electrical energy in a wide range of applications, making it a critical technology in the modern world. As we continue to push the boundaries of what's possible in power management and conversion, power electronics stands at the forefront, driving innovation and efficiency in everything from consumer electronics to industrial systems.
Historical Development and Evolution
Close-up view of a coil encircled by copper wire on a white printed circuit board, an essential component of a switch-mode power supply's electromagnetic induction choke.
The journey of power electronics is a fascinating tale of innovation and evolution, stretching from the early 20th century to the present day. This timeline of key developments has seen the field progress from primitive rectifiers to the sophisticated Insulated Gate Bipolar Transistors (IGBTs) and Metal-Oxide-Semiconductor Field-Effect Transistors (MOSFETs) of today.
In the early 1900s, the foundation of power electronics was laid with the advent of rectifiers, devices used to convert alternating current (AC) to direct current (DC). These early rectifiers, made from vacuum tube diodes and later selenium plates, were pivotal in the initial stages of power conversion technology.
The mid-20th century witnessed a significant leap with the introduction of silicon-based semiconductor devices. The creation of the thyristor, or silicon-controlled rectifier (SCR), in the 1950s marked a turning point. This allowed for more efficient and controllable power conversion, paving the way for a range of applications, from motor drives to power transmission.
The 1970s and 1980s saw the emergence of power MOSFETs and IGBTs, which revolutionised power electronics with their superior efficiency, faster switching speeds, and greater reliability. These components became the backbone of modern power electronic systems, enabling compact, energy-efficient designs.
One pivotal moment in the history of power electronics was the development of the variable frequency drive (VFD). This technology, which controls the speed of an electric motor by varying the frequency and voltage of its power supply, has had a profound impact on energy savings and operational efficiency in industrial applications.
Another significant advancement was the integration of digital control technologies in the 1990s. The incorporation of microcontrollers and digital signal processors (DSPs) allowed for more precise and adaptable control schemes, further enhancing the efficiency and capabilities of power electronic systems.
The evolution of power electronics has been closely tied to technological advancements in materials science, semiconductor technology, and control theory. The shift from silicon to wide-bandgap materials like silicon carbide (SiC) and gallium nitride (GaN) in recent years has opened new horizons. These materials offer higher efficiency, greater power density, and the ability to operate at higher temperatures and voltages, expanding the capabilities and applications of power electronics into areas like renewable energy systems, electric vehicles, and smart grids.
As we look back at the historical development of power electronics, it's clear that each technological breakthrough has not only enhanced the performance of power electronic systems but also expanded their application scope, playing a crucial role in the advancement of a wide array of industries and technologies.
Key Components of Power Electronics
The field of power electronics is built upon several key components, each playing a vital role in the control and conversion of electrical power. These components have evolved significantly over time, adapting to the changing needs of various applications.
Semiconductors (Diodes, Transistors):
Semiconductors are the building blocks of power electronics, with diodes and transistors being the most fundamental components.
-
Diodes: Diodes allow current to flow in one direction only and are essential for rectification processes. They have evolved from vacuum tube diodes to semiconductor diodes, including Silicon, Germanium, and more recently, Silicon Carbide (SiC) and Gallium Nitride (GaN) diodes. Each advancement has offered improvements in efficiency, speed, and thermal performance. For instance, SiC diodes are widely used in high-voltage applications due to their ability to operate at higher temperatures and voltages with greater efficiency.
-
Transistors: Transistors, including Bipolar Junction Transistors (BJTs), Field-Effect Transistors (FETs), MOSFETs, and IGBTs, function as switches or amplifiers in power electronic circuits. The evolution from BJTs to MOSFETs and IGBTs marked a significant improvement in power handling capabilities and switching speeds. MOSFETs, for example, are preferred in low to medium power applications due to their high switching speed and efficiency, while IGBTs are favoured in high power applications for their high current and voltage handling capabilities.
Converters (AC to DC, DC to AC, DC to DC, AC to AC):
Converters are critical in changing the form of electrical power to suit different applications.
-
AC to DC (Rectifiers): Rectifiers convert alternating current (AC) to direct current (DC). They range from simple single-phase diode bridges to complex three-phase controlled rectifiers, used in applications like battery charging and DC motor drives.
-
DC to AC (Inverters): Inverters convert DC to AC and are crucial in applications like solar power systems and electric vehicles. Modern inverters not only convert power but also adjust frequency and voltage to match grid requirements or specific load demands.
-
DC to DC (DC Converters): These converters change the level of DC voltage and are used in applications like power supplies for electronic devices, where different components require different voltage levels.
-
AC to AC (AC Converters): AC converters, including cycloconverters and matrix converters, change the frequency and voltage of AC power. They are used in applications like variable-speed AC motor drives.
Controllers and Regulators:
Controllers and regulators are essential for managing the performance of power electronic systems.
-
Controllers: These components manage the operation of converters and inverters, ensuring that the output meets the desired criteria. They range from simple analog circuits to sophisticated digital controllers using microprocessors or DSPs. Controllers are crucial in applications like motor drives, where precise control of speed and torque is required.
-
Regulators: Voltage and current regulators maintain the output of power electronic systems at a constant level, despite variations in load or input voltage. They are fundamental in power supplies and battery chargers to protect sensitive electronic components from voltage fluctuations.
In summary, the components of power electronics - semiconductors, converters, controllers, and regulators - have evolved significantly, driven by advancements in materials science, semiconductor technology, and digital control techniques. Their continuous development has expanded the capabilities of power electronic systems, enabling more efficient, reliable, and compact solutions for a wide range of applications.
Efficiency and Size Considerations
Efficiency in power electronics is not just a desirable attribute; it's a critical factor that significantly impacts energy consumption and system performance. This section delves into why efficiency is paramount in power electronic systems and explores the ongoing challenges and solutions in miniaturising these devices.
Importance of Efficiency:
-
Energy Consumption: The efficiency of power electronic devices directly affects the amount of electrical energy converted into heat. Higher efficiency means less energy is wasted as heat, leading to reduced energy consumption. This is particularly crucial in applications like renewable energy systems and electric vehicles, where maximising energy utilisation is key.
-
System Performance: Efficient power conversion ensures optimal performance of the end-use equipment. For instance, in an electric vehicle, more efficient power electronics can translate to longer battery life and extended driving range.
-
Thermal Management: High efficiency alleviates thermal management challenges. Power electronic devices generate heat during operation, and excessive heat can lead to reliability issues and reduced lifespan. Efficient devices generate less heat, simplifying cooling requirements and enhancing overall reliability.
Challenges in Miniaturization:
Miniaturising power electronic devices while maintaining or improving their efficiency is a significant engineering challenge. Smaller devices are desired for their compactness, which is essential in space-constrained applications like mobile devices and aerospace.
-
Heat Dissipation: As devices shrink, the heat generated per unit area increases, making thermal management more challenging. Efficient heat dissipation mechanisms are crucial to prevent overheating in miniaturised devices.
-
Material Limitations: The physical properties of materials used in semiconductors impose limits on miniaturisation. Innovations in materials like SiC and GaN have been pivotal in overcoming some of these limitations, offering better performance at smaller sizes.
-
Manufacturing Complexity: Producing smaller power electronic components often involves more complex manufacturing processes, which can increase costs and affect scalability.
Case Studies in Efficiency Improvements:
Renewable Energy Systems: In solar inverters, advancements in power electronics have led to higher conversion efficiencies, enabling more solar energy to be converted into usable electrical power. Modern inverters achieve efficiencies upwards of 98%, significantly improving the viability of solar installations.
- Electric Vehicles: The development of compact, high-efficiency power electronic systems in electric vehicles has been instrumental in increasing their range and performance. For example, the use of advanced SiC-based power electronics in some electric vehicles has led to improvements in efficiency, contributing to longer battery life and extended range.
- Consumer Electronics: The miniaturisation of power supplies for consumer electronics, like laptops and smartphones, has seen significant advancements. Modern power adapters are not only smaller but also much more efficient, reducing energy wastage and improving user convenience.
In conclusion, efficiency and size are interdependent considerations in the design and development of power electronic systems. Striking the right balance between these two factors is key to meeting the demands of modern applications, from portable electronics to large-scale industrial systems. The ongoing research and development in materials, design, and manufacturing techniques continue to push the boundaries of what is possible in power electronics, aiming for smaller, more efficient, and more reliable systems.
Heat Dissipation and Thermal Management
Effective thermal management is a critical aspect of power electronics, especially as devices become more powerful and compact. This section provides a comprehensive overview of thermal management techniques, including recent advancements, and presents case studies demonstrating these techniques in high-power applications.
Close-up view of thermal paste application on an AMD FX 8350 processor.
Thermal Management Techniques:
-
Heat Sinks and Cooling Systems: Traditional heat sinks, made from materials with high thermal conductivity like aluminium or copper, are widely used to dissipate heat in power electronic devices. Advances in heat sink design, including optimised fin structures and liquid cooling systems, have significantly improved heat dissipation efficiency.
-
Thermal Interface Materials (TIMs): TIMs, such as thermal pastes, pads, and epoxies, are used to improve the thermal contact between the heat source (e.g., semiconductor device) and the heat sink. Recent developments in TIMs focus on materials with higher thermal conductivity and longer operational life.
-
Advanced Cooling Techniques: Techniques like phase-change cooling, where a fluid absorbs heat and changes phase (from liquid to gas), offer efficient cooling for high-power applications. Microchannel cooling, where tiny channels are etched into a substrate to allow fluid flow, provides effective heat dissipation in a compact form factor.
-
Integration of Cooling into Device Design: Modern power electronic devices are increasingly designed with integrated cooling solutions. For example, embedding cooling channels directly into the substrate or the semiconductor package allows for more direct and efficient heat removal.
Case Studies in Thermal Management:
Electric Vehicle Power Electronics: In electric vehicles (EVs), power electronic components like inverters and converters handle high power levels, generating significant heat. Advanced cooling systems, often involving liquid coolants, are used to maintain optimal operating temperatures. For instance, some EV models use integrated cooling plates that are thermally connected to the power electronic components, ensuring efficient heat dissipation.
- Industrial Motor Drives: High-power industrial motor drives require robust thermal management to handle the heat generated by power semiconductors. Case studies have shown the effectiveness of liquid cooling systems in these applications, where coolant is circulated through heat exchangers directly attached to the power modules. This approach allows for higher power density and improved reliability.
- Renewable Energy Systems: In solar inverters and wind turbine converters, managing heat is crucial for performance and longevity. Advanced air-cooling and liquid-cooling techniques are employed to manage the thermal load. For example, some high-capacity solar inverters use sophisticated air-cooling systems with smartly designed airflow paths and heat sinks to maintain optimal temperatures.
In summary, thermal management in power electronics is a multifaceted challenge that requires a combination of materials, design, and advanced cooling technologies. As power densities increase and devices become smaller, the importance of efficient heat dissipation becomes even more critical. The ongoing innovations in thermal management techniques are essential for the continued advancement and reliability of power electronic systems in various high-power applications.
Applications in Various Systems
Power electronics find their applications in a broad spectrum of fields, each presenting unique challenges and innovations. This detailed exploration covers high-power applications, consumer electronics, renewable energy systems, and electric vehicles, highlighting their current state and future trends.
High-Power Applications:
Grid Management: Power electronics play a crucial role in modern grid management, facilitating efficient transmission and distribution of electricity. They are key in implementing solutions like FACTS (Flexible AC Transmission Systems) and HVDC (High Voltage Direct Current) systems, which enhance grid stability and capacity. The challenge lies in managing the high power levels and ensuring system reliability under diverse grid conditions.
Industrial Machinery: In industrial settings, power electronics are essential for operating heavy machinery, including motor drives and automation systems. The primary challenge is to ensure these systems are both energy-efficient and robust enough to withstand harsh industrial environments. Solutions like advanced motor drives and soft starters have been developed to address these needs, offering greater control and reducing mechanical stress on the machinery.
Consumer Electronics:
Smartphones and Laptops: In the realm of consumer electronics, power electronics are integral to the design and function of devices like smartphones and laptops. They manage power delivery and battery charging, balancing the need for fast charging with battery longevity. The challenge is miniaturisation, as these devices require increasingly smaller and more efficient power components.
Cardboard boxes filled with household appliances and electronics on warehouse shelves, illustrating the concept of online shopping and delivery. 3D illustration.
Renewable Energy Systems:
Solar Inverters and Wind Turbine Converters: Power electronics are vital in renewable energy systems, particularly in solar inverters and wind turbine converters. They convert the variable power generated from renewable sources into a stable form that can be fed into the electrical grid or used directly. The ongoing challenge is to improve efficiency and reliability, especially as these systems scale up. Future trends include the integration of smart and adaptive control systems that can respond dynamically to changing environmental conditions and grid demands.
3D-rendered image of a battery energy storage system, featuring multiple side-by-side lithium battery modules designed for storing renewable energy for later use.
Electric Vehicles and Battery Management:
Electric Vehicles (EVs): In electric vehicles, power electronics are central to managing the flow of power between the battery, motor, and other electrical systems. They ensure efficient use of the battery's energy and contribute to the vehicle's overall performance and range. The main challenge is optimising the balance between power density, efficiency, and thermal management.
Battery Management Systems (BMS): BMS in EVs are sophisticated systems designed to manage the battery pack's state of charge and health. They play a critical role in ensuring the safety, longevity, and performance of the battery. The focus is on developing more advanced BMS that can accurately predict battery life, optimise charging cycles, and integrate seamlessly with the vehicle's overall power system.
In summary, power electronics are fundamental across various systems, each with its specific requirements and challenges. From enhancing the efficiency and stability of power grids and industrial machinery to enabling the widespread adoption of renewable energy and electric vehicles, power electronics are at the heart of modern technological advancements. As these fields continue to evolve, power electronics will play an increasingly vital role in driving innovation and addressing the world's growing energy needs.
Voltage and Frequency Regulation
Voltage and frequency regulation are critical aspects of power electronics, especially in alternating current (AC) systems. This section provides a detailed explanation of these concepts, focusing on techniques and challenges in voltage regulation for small devices.
A measuring device, complete with a circuit diagram and measuring tips, laid out on a table.
Voltage Regulation in AC Systems:
-
Purpose: Voltage regulation in AC systems is essential to ensure a stable voltage supply despite fluctuations in load or input voltage. Stable voltage is crucial for the proper functioning and longevity of electrical and electronic equipment.
-
Techniques: Common techniques for voltage regulation include the use of transformers with tap changers, voltage regulators, and advanced power electronic devices like thyristors and IGBTs. Automatic Voltage Regulators (AVRs) are widely used in applications ranging from household electronics to industrial machinery. They automatically adjust the voltage to the desired level, compensating for any fluctuations in the input supply.
-
Challenges: The primary challenge in voltage regulation is maintaining a consistent output voltage level despite variations in load and input conditions. This becomes increasingly complex in systems with highly variable loads or in scenarios where the power supply is intermittent or unstable.
Frequency Regulation in AC Systems:
-
Purpose: Frequency regulation is vital to maintain the stability of the power system. In AC systems, frequency is directly related to the rotational speed of generators. Maintaining a constant frequency ensures the smooth operation of all equipment connected to the grid.
-
Techniques: Frequency is regulated at the generation stage, where governors on generators adjust the input mechanical power to maintain a steady rotational speed and hence a stable frequency. Inverter-based resources in renewable energy systems also contribute to frequency regulation through advanced control strategies.
-
Challenges: The integration of renewable energy sources, which can be intermittent and variable, poses a significant challenge to frequency regulation. Balancing supply and demand while accommodating these renewable sources requires sophisticated control and forecasting techniques.
Voltage Regulation for Small Devices:
-
Techniques: In small devices, voltage regulation is typically achieved using linear regulators or switching regulators. Linear regulators, while simpler and less noisy, are less efficient as they dissipate excess voltage as heat. Switching regulators, on the other hand, offer higher efficiency by rapidly switching the input voltage on and off and controlling the duty cycle to achieve the desired output voltage.
-
Challenges: The main challenge in small devices is miniaturisation while maintaining efficiency and managing heat dissipation. As devices become smaller and more power-dense, effective thermal management becomes crucial. Additionally, maintaining regulation accuracy in the face of varying load conditions and battery voltage levels is a key concern.
In conclusion, voltage and frequency regulation are fundamental to the functionality and efficiency of AC systems, from large-scale power grids to small electronic devices. The ongoing development of more sophisticated and efficient regulation techniques is crucial to meet the demands of an increasingly electrified and technologically advanced society.
Conversion Techniques
Power electronics heavily relies on various conversion techniques to manipulate electrical energy to suit different applications. This section provides an in-depth analysis of key conversion techniques, including rectifiers, inverters, and buck/boost converters, supplemented with case studies and examples of each technique in use.
Hand holding an orange-plated computer heatsink with PC internals in a blurry background.
Rectifiers:
-
Function: Rectifiers convert alternating current (AC) to direct current (DC). They are fundamental in applications where DC power is required but only AC is available, such as in power supplies for electronic devices.
-
Types: Rectifiers can be classified as half-wave, full-wave, and bridge rectifiers. Full-wave and bridge rectifiers are more efficient as they utilise both halves of the AC cycle.
-
Case Study: A common application is in the power supply of household electronics. For instance, the adapter of a laptop uses a rectifier to convert the AC from the wall outlet into the DC required by the laptop.
Inverters:
-
Function: Inverters convert DC to AC, which is essential in applications like renewable energy systems where the generated power is in DC form but needs to be converted to AC for grid compatibility or usage in AC appliances.
-
Types: Inverters range from simple square wave inverters to more complex pure sine wave inverters. Pure sine wave inverters are preferred for their ability to produce a smooth, consistent wave, similar to the power supplied by the grid, making them suitable for sensitive electronic equipment.
-
Case Study: In solar power systems, inverters convert the DC power generated by solar panels into AC power for home use or for feeding into the electrical grid.
Buck/Boost Converters:
-
Function: Buck converters step down voltage levels, while boost converters step up voltage levels. They are used in applications where the voltage needs to be adjusted to a specific level.
-
Types: These converters can be non-isolated or isolated, with isolated converters providing galvanic isolation between input and output.
-
Case Study: A practical example is in LED lighting systems, where a buck converter is used to regulate the voltage to a level suitable for the LEDs, ensuring consistent brightness and improving efficiency.
Combination Converters:
-
Buck-Boost Converters: These converters can either step up or step down the voltage as needed. They are particularly useful in battery-powered applications where the battery voltage can vary over its life.
-
Case Study: In electric vehicles, buck-boost converters are used to maintain a stable voltage supply to the vehicle's electronics as the battery discharges.
In summary, conversion techniques in power electronics, including rectifiers, inverters, and buck/boost converters, are essential for a wide range of applications. These techniques enable the efficient and effective transformation of electrical energy to the required form, ensuring compatibility with different devices and systems. The ongoing advancements in these technologies continue to enhance their efficiency, reliability, and adaptability, meeting the evolving needs of modern electrical and electronic systems.
Protection and Safety Mechanisms
In power electronics, ensuring the safety and longevity of both the devices and the users is paramount. This section provides a comprehensive overview of various protection mechanisms employed in power electronics, including overvoltage, undervoltage, overcurrent, short circuit, and thermal protection, along with real-world examples of these mechanisms in action.
Overvoltage Protection:
-
Function: Overvoltage protection safeguards electronic components from voltage spikes that exceed their maximum voltage rating, which can cause damage or failure.
-
Mechanisms: Common overvoltage protection methods include the use of varistors, zener diodes, and transient voltage suppressor (TVS) diodes.
-
Example: In power supply units (PSUs), overvoltage protection is crucial to prevent damage to the PSU and connected devices in case of a surge, typically implemented using TVS diodes.
Undervoltage Protection:
-
Function: Undervoltage protection ensures that electronic devices do not operate below their minimum voltage requirement, which can lead to malfunction or unstable operation.
-
Mechanisms: This is often achieved using undervoltage lockout circuits that disable the power supply if the input voltage drops below a predefined threshold.
-
Example: In battery-operated devices, undervoltage protection is essential to prevent deep discharge of the battery, thereby prolonging its life and maintaining device performance.
Overcurrent Protection:
-
Function: Overcurrent protection prevents damage caused by excessive current, which can result from overload or short-circuit conditions.
-
Mechanisms: Fuses, circuit breakers, and current limiters are commonly used for overcurrent protection.
-
Example: In motor drives, overcurrent protection is vital to protect the motor from damage due to mechanical overloads or short circuits, often implemented using circuit breakers or fuses.
Short Circuit Protection:
-
Function: Short circuit protection is designed to quickly disconnect the power supply in the event of a short circuit, preventing damage to the power source and the circuit.
-
Mechanisms: This protection is typically provided by fast-acting fuses or circuit breakers that can interrupt the circuit in milliseconds.
-
Example: In home electrical systems, circuit breakers provide short circuit protection, disconnecting the power in case of wiring faults or appliance failures.
Thermal Protection:
-
Function: Thermal protection prevents overheating, which can damage electronic components or cause fires.
-
Mechanisms: Thermal protection can be implemented using thermal fuses, thermostats, and temperature sensors coupled with automatic shutdown circuits.
-
Example: In power amplifiers, thermal protection is critical to prevent damage from excessive heat. This is often achieved using temperature sensors that trigger a shutdown if the temperature exceeds safe limits.
In conclusion, protection and safety mechanisms in power electronics are essential for the reliable and safe operation of electronic systems. These mechanisms not only prevent damage to the components but also ensure user safety. The integration of these protective features is a critical aspect of power electronic system design, reflecting the importance of reliability and safety in the field of electronics.
Future Trends and Innovations
The field of power electronics is continuously evolving, driven by advances in technology and emerging applications. This section explores the future trends and innovations in semiconductor technology, the growing role of power electronics in IoT devices and smart grids, and their contribution to sustainable energy solutions, with a focus on environmental impacts.]
Futuristic vehicle dashboard display.
Advances in Semiconductor Technology:
-
Wide-Bandgap Semiconductors: Materials like Silicon Carbide (SiC) and Gallium Nitride (GaN) are at the forefront of semiconductor technology. These wide-bandgap semiconductors offer superior properties, such as higher efficiency, faster switching speeds, and the ability to operate at higher temperatures and voltages. This leads to smaller, more efficient power electronic devices.
-
Potential Future Developments: Research is ongoing into developing even more efficient semiconductor materials, such as Gallium Oxide (Ga2O3) and Diamond. These materials promise further improvements in power density, efficiency, and thermal performance, potentially revolutionising power electronics.
Emerging Applications in IoT Devices and Smart Grids:
-
IoT Devices: The proliferation of IoT devices has created a demand for efficient, compact power electronic solutions. Future trends include the development of ultra-low-power semiconductor devices that can harvest energy from their environment, reducing or eliminating the need for external power sources.
-
Smart Grids: Power electronics play a crucial role in the development of smart grids, which require sophisticated control and conversion technologies to integrate renewable energy sources, manage load, and ensure grid stability. Advancements in power electronics are enabling more efficient grid management and energy distribution, paving the way for a more resilient and sustainable energy infrastructure.
Sustainable Energy Solutions and Environmental Impact:
-
Role in Renewable Energy: Power electronics are key to maximising the efficiency of renewable energy systems, such as solar panels and wind turbines. Future innovations in power electronic converters can lead to even higher efficiencies, reducing the cost of renewable energy and accelerating its adoption.
-
Energy Storage Systems: The integration of energy storage systems, like batteries and supercapacitors, with power electronics is vital for balancing energy supply and demand, especially in renewable energy systems. Advancements in power electronics are enhancing the efficiency and lifespan of these storage systems.
-
Environmental Impact: The focus on developing more efficient power electronic devices directly contributes to reducing energy wastage and, consequently, the environmental impact. By improving the efficiency of electrical systems, power electronics play a significant role in reducing greenhouse gas emissions and promoting sustainable energy practices.
In summary, the future of power electronics is marked by exciting advancements in semiconductor technologies, expanding applications in IoT and smart grids, and a significant role in fostering sustainable energy solutions. These innovations not only promise enhanced performance and efficiency but also contribute to a more sustainable and environmentally friendly future.
Final Thoughts
This article has provided a comprehensive exploration of power electronics, delving into its fundamental concepts, historical development, key components, and the various applications and challenges it addresses in modern technology. As we conclude, let's summarise the key points and reflect on the significance and future of power electronics.
Key Points Summary:
-
Definition and Basic Concepts: Power electronics involves the control and conversion of electrical power using solid-state electronics, with a focus on handling higher power levels and efficiency compared to general electronics.
-
Historical Development: The field has evolved from early rectifiers in the 20th century to today's advanced IGBTs and MOSFETs, with each development enhancing performance and expanding applications.
-
Key Components: Semiconductors, converters, controllers, and regulators form the backbone of power electronic systems, each playing a crucial role in efficient energy management.
-
Efficiency and Size Considerations: Efficiency is paramount in power electronics, influencing energy consumption and system performance. Miniaturisation remains a key challenge, balancing compactness with performance.
-
Thermal Management: Effective heat dissipation techniques are crucial, especially as power densities increase in smaller devices.
-
Applications: Power electronics find diverse applications in high-power systems, consumer electronics, renewable energy, and electric vehicles, each presenting unique challenges and innovations.
-
Protection and Safety: Various mechanisms, including overvoltage, undervoltage, overcurrent, short circuit, and thermal protection, are essential for the safe operation of power electronic systems.
-
Future Trends and Innovations: Advances in semiconductor technology, the integration of power electronics in IoT and smart grids, and their role in sustainable energy solutions highlight the field's ongoing evolution.
Conclusion:
The significance of power electronics in modern technology cannot be overstated. As the world increasingly relies on electronic devices and systems, the demand for efficient, reliable, and compact power electronic solutions continues to grow. The field stands at the forefront of technological innovation, driving advancements in renewable energy, electric mobility, and smart infrastructure.
Looking ahead, the future of power electronics is bright and promising. With ongoing research and development in semiconductor materials, control techniques, and system integration, power electronics will continue to play a pivotal role in shaping a sustainable and technologically advanced future. As we embrace this future, the importance of power electronics in our daily lives and its contribution to global environmental goals will become even more pronounced, solidifying its status as a key enabler of modern technology.
References
- Power Electronic Tips - https://www.powerelectronictips.com/
- Wikipedia: Power Electronics - https://en.wikipedia.org/wiki/Power_electronics
- Power Electronics Design Methods & Automation by Cardoso, 2020 - PDF Link
- The Future of Power Electronics Circuits, IEEE PELS Magazine by R. Pilawa, 2020 - PDF Link
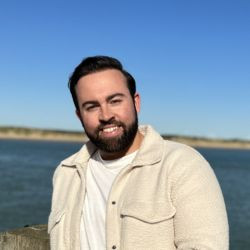