Improving Procurement Efficiency in Electronics
06-01-2025 | By Mouser Electronics
Electronic component procurement is a competitive and fast-moving industry. Inefficiencies from various sources pose challenges, requiring procurement professionals to address them proactively to maintain a competitive edge.
Common Causes of Inefficiency
Supply chain management is a crucial aspect of the electronic components sector. Globalised supply chains, coupled with events like inflation, geopolitical tensions, natural disasters, and evolving regulations, create disruptions. These, alongside routine market fluctuations, can hinder the delivery of components from suppliers to end customers. Effective supply chain management is essential for ensuring resilience.
Poor planning is a significant factor in supply disruptions and extended lead times. While planning is always necessary, its absence becomes more apparent during unforeseen national, global, or local events. Issues such as excess inventory, stock shortages, last-minute sourcing, and increased transportation costs can negatively affect operations and stakeholder relationships.
Miscommunication within the procurement process is another common issue, leading to errors, delays, and increased costs. Misunderstandings about requirements and specifications can result in incorrect orders, rework, and even product failures. Effective communication supports better decision-making, coordination, and supply chain agility.
Manual processes also contribute to inefficiencies. Paper-based invoicing and manual matching of purchase orders to invoices remain widespread but come at a cost. According to Jaggaer’s The State of Procurement 2024, 42% of respondents cited manual processes as a significant barrier to strategic procurement. While automation is increasingly recognised as essential, some organisations still view it as a future goal rather than an immediate necessity.
Using Audits to Enhance Efficiency
Regular audits can help identify inefficiencies and improve procurement processes. An audit reviews internal controls, supplier selection, contract management, and operational practices to ensure compliance and efficiency.
The audit process involves gathering documentation, such as procurement policies, vendor contracts, purchase orders, invoices, and delivery records. Audit teams should also review vendor performance, internal controls, and discrepancies in processes. By doing so, organisations can refine procurement practices, minimise risks, and align with regulatory requirements.
Audits also highlight workflow barriers, assess the effectiveness of controls, and evaluate resource allocation, including personnel, technology, and budgets. Engaging procurement staff in the process is vital—their insights can pinpoint pain points and drive improvements.
The Role of Automation and Digital Tools
Inefficient use of technology, or the lack of it, can hinder procurement efforts. Automation is a critical first step in improving processes like invoicing, accounts payable, and payment reconciliation. By leveraging digital tools, organisations can access real-time data, streamline procurement patterns, and make informed decisions.
Procurement software solutions, such as electronic procurement systems and spend analysis tools, play a key role in this transformation. Artificial intelligence (AI) is also becoming an integral part of procurement, offering new opportunities for efficiency and strategic value creation.
As electronic component procurement continues to evolve, adopting digital technologies will be central to maintaining competitiveness and resilience.
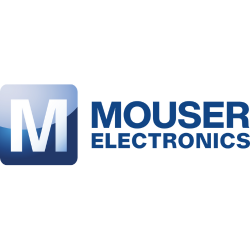