3D Printed Rocket Engines Redefine Low-Cost Spaceflight
09-04-2025 | By Robin Mitchell
While single-use rockets have long been the backbone of space travel, the push for more cost-effective and sustainable solutions has sparked a quest for new manufacturing approaches. Recently, companies like Rocket Lab have made a notable breakthrough in the realm of 3D-printed rocket engines, which drastically shorten production times and lower costs without sacrificing performance.
Key Thing to Know:
- Rocket Lab’s 3D-printed Rutherford engine cuts production to just 24 hours, accelerating commercial satellite launch capabilities.
- Electron rocket’s precision Kick Stage enables exact orbital deployment, boosting constellation performance and satellite lifespan.
- Kinéis’ IoT constellation uses 30kg-class nanosats with AIS, expanding coverage for maritime tracking and environmental monitoring.
- Future designs with reusable 3D-printed propulsion and on-demand space manufacturing may support deep-space autonomy and sustainability.
What challenges do modern rocket systems face, what has Rocket Lab achieved with its innovative engine design, and what are the broader implications of 3D-printed propulsion for the future of space exploration?
The Complex Landscape of Modern Rocket Systems
The evolution of rocket technology has played a critical role in shaping the space exploration industry. From the early days of pioneering ventures to the sophisticated systems in use today, rocket technology has experienced countless developments. The shift from single-use rockets to reusable systems has been a pivotal development in this evolution, marking a turning point in the history of space travel, but while many see reusable rockets as the future, others hold reservations.
The move towards reusable rockets has been driven by the need for cost-effectiveness in space exploration. Traditional rocket launches have been plagued by high costs, with financial burdens arising from a multitude of factors, including materials, technology advancements, and labour costs.
However, while the advantages of reusable rockets are well-documented, the practical economic outcomes of such systems have been less impressive. The theoretical benefits of reusability, including reduced launch costs and increased launch frequency, have yet to be realised in a profitable manner. Barriers to achieving a return on investment for reusable rockets include the high upfront costs of developing such systems and the challenges of ensuring their reliability and performance.
The technical complexity of rocket engines is another critical factor in the development of modern rocket launch systems. The intricate design and engineering challenges associated with rocket engines make them one of the most critical components of any launch system. The extreme forces and environments encountered during rocket launches pose significant challenges to engine durability and performance, requiring engineers to develop innovative solutions to overcome these obstacles.
Reusability under extreme conditions is a significant challenge faced by rocket engineers. Designing rockets that can withstand multiple launch cycles and landings safely is no easy feat. Maintaining the structural integrity and functionality of reusable rockets requires careful planning and execution, making it a complex and demanding task. The challenges associated with reusability are further compounded by the need to ensure that reusable rockets can be integrated into existing launch systems, making them compatible with existing infrastructure and logistics.
Rocket Lab Launches IoT Satellites Utilising 3D Printed Engines, Sees Stock Surge
In a recent development in the field of space technology, Rocket Lab has successfully launched five satellites for French Internet-of-Things (IoT) operator Kinéis into a 647 km Low-Earth Orbit (LEO). The mission, titled "IOT 4 You & Me," marked the fourth in a consecutive series of five launches, deploying a total of 20 Kinéis satellites into orbit. The goal is to reach 25 satellites by the end of the year.
Kinéis' constellation, composed of 30kg-class nanosatellites, features integrated IoT technology and AIS (Automatic Identification System) capabilities. These enhancements support expanded applications in maritime tracking, wildlife monitoring, and environmental research. By scaling from 20,000 to potentially millions of connected devices, the constellation significantly strengthens Kinéis’ position within the global satellite IoT ecosystem.
Precision Deployment with Electron and Kick Stage
The Electron rocket, launched from Launch Complex 1 at Mahia, New Zealand—privately owned and operated by Rocket Lab—carried the five satellites into orbit on February 9, 20. Rocket Lab's founder and CEO, Peter Becks, stated that this mission is a demonstration of the reliability and efficiency of the Electron rocket, which has demonstrated pinpoint accuracy in deploying satellite constellations. The company aims to tailor missions and schedules to meet customer needs, emphasising its commitment to providing high-quality launch services.
The mission’s use of Rocket Lab’s Kick Stage—a precision orbital deployment system—enabled each satellite to be positioned in its designated 650km plane without compromising satellite mass for onboard propulsion. This approach improves constellation performance by minimising drift and reducing satellite fuel dependency, allowing for longer operational lifespans and more accurate data retrieval.
The Rutherford engine, which powered the Electron rocket, is a significant development in space rocket manufacturing. The engine is the world's first 3D-printed, electric pump-fed orbital engine, featuring primary components that are entirely 3-D printed. This design allows for rapid production, with primary components being printed in as little as 24 hours, significantly reducing production timelines compared to traditional manufacturing methods.
Proven Performance and Scalable Propulsion
This rapid engine manufacturing approach aligns with the increasing demand for responsive satellite deployment, particularly for sectors relying on real-time Earth observation and remote sensing. The streamlined supply chain also benefits mission resilience by allowing faster turnaround times for engine production and testing, enhancing scheduling agility for operators like Kinéis.
The Rutherford engine has undergone extensive testing, with a total of 350 engines launched into space since the first Electron launch in 2025. The engine's reliability and performance have been consistently demonstrated, making it one of America's most frequently flown U.S. Orbital Rocket Engines.
Electron’s track record in deploying small satellite constellations, including Kinéis and earlier missions for BlackSky, has solidified Rocket Lab’s authority in the small launch sector. These missions validate the scalability of 3D-printed propulsion in commercial orbital operations and reinforce Rocket Lab’s reliability as a trusted launch provider for high-priority, multi-launch campaigns.
The partnership between Rocket Lab and Kinéis has been a crucial factor in the successful deployment of the Kinéis satellite constellation. The two companies have collaborated on a series of five dedicated launches, each carrying five satellites into orbit. The first three launches took place in June, September, and November, and the final launch scheduled for March 2025 aims to complete the 25-satellite constellation.
Support for the Kinéis project has come from a consortium of public and private stakeholders, including the French space agency CNES and space systems specialists like Thalès Alénia Space. This collaboration underscores the strategic value of IoT constellations for national and international space-based infrastructure, from environmental monitoring to maritime safety and agricultural optimisation.
The Future of 3D-Printed Rocket Engines and Space Travel
The Demonstration of the newly 3D-printed rocket engines marks a new era in space exploration, one that promises to redefine the way rockets are designed, built, and launched. With companies like Rocket Lab demonstrating the viability of 3D-printed propulsion systems, the industry is on the brink of a transformation that could make space travel more accessible, cost-effective, and efficient than ever before.
One of the most significant advantages of 3D-printed rocket engines is the dramatic reduction in manufacturing time and costs. Traditional rocket engines require complex machining, assembly of multiple components, and extensive quality control procedures—processes that can take months or even years to complete. By contrast, additive manufacturing techniques allow engineers to produce highly intricate and optimised engine components in a matter of days, drastically streamlining the production cycle. This accelerated production capability means that rocket companies can scale their operations more rapidly and respond to the growing demand for satellite deployment, deep-space exploration, and even commercial space travel.
Moreover, 3D printing enables greater design flexibility, allowing engineers to create lightweight and more efficient engine components that were previously impossible to manufacture using conventional methods. Advanced materials, such as metal alloys specifically engineered for high-temperature resistance, can be integrated seamlessly into these designs, improving engine durability and performance under extreme conditions. The Rutherford engine, for example, has already demonstrated how this technology can enhance reliability while minimising production waste and cost.
Enhancing Efficiency and Environmental Sustainability
As the technology continues to evolve, future iterations of 3D-printed rocket engines are expected to push the boundaries of propulsion efficiency. New hybrid designs that incorporate reusable components and advanced cooling systems could extend engine lifespans and reduce the environmental impact of rocket launches. Additionally, research into novel fuel combinations and electric propulsion enhancements may further improve the sustainability of space missions, paving the way for greener and more efficient launches.
Beyond Earth, the potential of 3D printing extends to in-situ manufacturing on other celestial bodies. Space agencies and private enterprises alike are exploring the possibility of using 3D printers to construct rocket components directly on the Moon or Mars, utilising locally sourced materials. This capability would eliminate the need for costly and complex supply chains from Earth, making deep-space colonisation and interplanetary travel far more feasible.
On-Demand Manufacturing for Deep-Space Autonomy
For engineers and space agencies, the rapid advancement of 3D-printed rocket technology means greater autonomy and resilience in mission planning. The ability to print and repair critical components on demand could revolutionise how spacecraft are maintained during long-duration missions. Imagine astronauts on Mars fabricating replacement parts for their landers or satellites printing propulsion systems while orbiting distant planets—such scenarios may soon transition from science fiction to reality.
Ultimately, the integration of 3D-printed engines into mainstream spaceflight represents a crucial step toward a more democratised and economically viable space industry. As technological barriers continue to be overcome, we are likely to witness a future where space travel is not only more frequent but also more sustainable and accessible to a wider range of participants. Whether it's launching vast satellite constellations, enabling deep-space exploration, or supporting human settlement beyond Earth, 3D-printed rocket engines are set to play a fundamental role in the next chapter of humanity's journey into the cosmos.
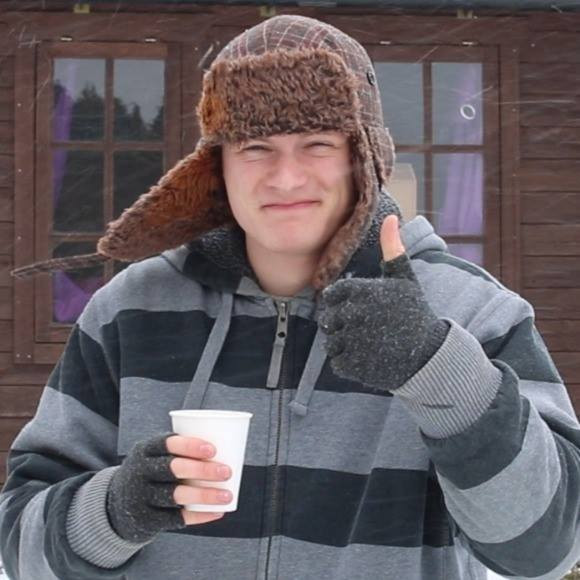