Addressing Design Challenges to Unleash the Full Potential of Drones
08-04-2025 | By Jack Pollard
This article was written by James Stratford, Technical Director, Universal Science and Materials Direct.
Drones have revolutionised aerial tasks that previously required hugely expensive approaches such as the use of helicopters or were just not possible at all. Drones are now used in applications as diverse as photography for real estate agents, traffic monitoring, sports filming and military tasks. Larger drones are already being trialled for delivery by companies including Amazon. Modern warfare has seen drones take on a key role – either for surveillance or as crude, simple, low-cost weapon carriers or highly sophisticated unmanned aerial vehicles (UAVs).
In terms of design, drones present a significant number of challenges and conflicting requirements. They incorporate complex and sensitive electronics that need to operate reliably in harsh environments for as long as possible between battery recharges.
A Challenging Electronic Design Environment
The focus of this article is the thermal management and physical protection of batteries and the electronics within a drone, but to build a complete picture it is important to cover some of the other areas of their electronic design and operation.
Addressing electronics challenges is crucial to ensure the reliability of drone functionality and safety. Efficient power management schemes are needed to distribute electricity to energy hungry components like motors as well as lower power demand devices such as sensors without excessively compromising battery life. The battery itself must strike a delicate balance between capacity and weight, providing enough power for adequate flight time while keeping the drone as light as possible so as not to require lots of power. Energy density is also important here - ensuring the battery is compact yet powerful. Looking forward, the development of exciting new battery technologies and alternatives to Lithium-Ion will be pivotal in improving power density and the operational time and range of drones and therefore the number and diversity of applications they can address.
In what is typically a hostile electrical environment, protecting circuitry from overcurrent, overvoltage, and short circuits is vital to prevent component damage. Drones often operate in high or unpredictable interference environments so minimising susceptibility to electromagnetic interference (EMI) is also necessary to avoid disruptions to the electronics and communications systems. Signal integrity must also be maintained to ensure effective control and communication. At device level, the trend of integration of smaller electronic components helps this as well as reducing the drone's size and weight while preserving its functionality. Integration can also have a positive effect on reliability as result of fewer, more exposed interconnects that are external to the components. Lastly, with the reliability of all electronic systems paramount, robust redundancy measures must be employed for critical components to provide a safeguard and back-up against in-flight failures.
Physical Protection
The cells within battery packs used in drones need to be protected against vibration and other environmental factors such as moisture ingress. This needs to be achieved with lightweight materials and a repeatable solution. Cell carrier materials that lend themselves to easy manufacture can offer a clean and beneficial alternative to potting compounds that are much heavier and harder to integrate into a production process.
Specialist foam materials used as cell carriers provide an important tool in the drone battery pack designer’s set of options and resources. Materials such as the EV-UniFoam range from Universal Science are a good example and can perform several roles in drone battery packs. The primary function is as a cell carrier with parts able to position, hold and protect multiple cells firmly in a fixed location within the pack.
Custom cell carriers, which in the case of Universal Science materials can be produced without tooling, also provide vibration dampening. During the life of a drone, all components, including the battery pack, are subjected to vibration and shocks that over time this can cause damage and even failure of interconnects and other aspects of the cell pack and surrounding electronics. Flame retardancy / self-extinguishing and low moisture absorption are other desirable characteristics of a cell carrier in a drone application.
Figure: Structural vibration damping foams provide a clean, lightweight and repeatable alternative to potting compounds for drone battery packs
Drone Thermal Management
The batteries, motors and other power electronic circuitry in drones all generate heat that must be kept within acceptable limits to guarantee safe and reliable operation. Active cooling components such as fans are effective from a thermal performance perspective, but they are heavy, consume a lot of precious power from the batteries, and are not as reliable passive cooling approaches achieved using heat conducting materials. Although heatsinks are one such passive cooling solution, their weight usually prohibits them from widespread use in drones. Coupling heat generating elements of the drone directly to the chassis or body – if it has metal elements - of the drone is an alternative way of effectively creating a good heat spreader and dissipator without incorporating additional components like heatsinks.
As drones usually need to be able to operate in all weathers, having a partially open or vented enclosure that would aid cooling, but raise the risk of moisture ingress is not viable. Therefore, using an approach to component heat management that ‘connects’ heat generating components to the chassis via thermal interface pads or gap fillers with high levels of thermal conductivity that can also mitigate vibration issues, is an approach that has proven to be highly effective in many applications over many years – not just on drones.
Figure: Gap filler materials used in drones can help dissipate heat to the chassis or enclosure
Lithium-ion batteries commonly used as the power source for drones need to operate within a temperature range of between approximately 5°C and 50°C so that premature degradation and the more serious worry of thermal runaway are avoided. A high-performing foam carrier such as EV-UniFoam that surrounds and holds individual cells within a pack is also useful in the overall heat management and stability of a drone battery pack. Its close cell structure protects the batteries from extremes of outside temperature and helps keep the pack within safe limits.
How Materials Direct Can Help
At Materials Direct, we specialise in providing advanced materials that can significantly enhance drone designs. Our range of thermal interface materials, including high-performance gap fillers and thermal pads, can help dissipate heat from sensitive components such as batteries and motors, eliminating the need for heavy, power-consuming fans. Additionally, our EV-UniFoam cell carriers offer a lightweight and repeatable solution to protect battery packs from vibration, moisture, and extreme temperatures, ensuring reliable performance in demanding environments.
By offering custom, tooling-free production of these materials, we provide flexibility in design, allowing manufacturers to streamline production and reduce costs. Whether you are seeking solutions for thermal management, structural protection, or electromagnetic shielding, Materials Direct is well-positioned to help overcome the technical challenges drones face, ensuring that they operate efficiently and reliably in the field.
Summary
Designing drones that are reliable, robust, have a good range and meet their task requirements in full, demands achieving a careful balance between physical protection and thermal management of both the battery pack and electronics, but without ending up with a design that is excessively heavy.
Cell carrier materials can provide a good alternative to potting compounds for protecting and ensuring a stable operating environment for battery packs, while thermal interface materials can overcome the need for active cooling such as fans to keep electronic components cool.
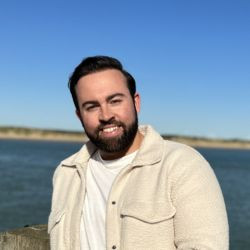