The Fundamentals of Smart Manufacturing
09-04-2025 | By Advantech
Key Thing to Know:
- Smart factories are reshaping manufacturing through hyper-connectivity, machine automation, and real-time data, driven by the Industrial Internet of Things (IIoT).
- Digital convergence of IT and OT enables near-complete automation, edge computing, and AI-powered decision-making for greater productivity, agility, and safety.
- Human-machine collaboration improves safety and empowers workers with tools like AR, co-bots, and real-time analytics to drive innovation and efficiency.
- Advantech’s smart solutions like EdgeLink and WebAccess support legacy system integration, edge intelligence, and data-driven operations for next-gen manufacturing.
Today’s customers demand more personalization, whilst manufacturers demand higher productivity and faster responses to market changes. Product quality and worker safety are also becoming a much higher priority. Competitors are popping up all over the globe, and new technologies such as 3D printing are redefining who is a ‘producer.’ Manufacturers still experience a significant amount of annual downtime, 30% of it unexpected. In addition, as skilled labour pools age, there is a chance that two million positions in the US alone will go unfilled.
Manufacturing is changing at a very rapid pace. There is a new type of connected, data-driven, and architecturally open factory emerging in response to these demands, led by the Industrial Internet of Things (IIoT). Along with increased machine automation, other characteristics of this new smart factory include hyper-agility, autonomous production, and data utilization as a tool for business.
Research conducted by Accenture for the World Economic Forum showed that 73% of the C-level executives interviewed were convinced that the IIoT would fundamentally change their industry. But just 20% had a strategy for harnessing it. Companies that want to succeed in the future must master the radical digital transition headed our way by opening themselves to a journey that will change their organization models beyond recognition – the alternative being a catastrophic loss of market share and profitability.
Smart, connected and data-driven
Smart manufacturing is now seen as a natural progression of the “digital convergence” already underway between information technology (IT) and operational technology (OT). There are four essential characteristics that set it apart.
Firstly, the smart factory uses data and IIoT connectivity to easily control all aspects of operations in near real-time, with near full automation across all locations. IoT and digital investment is the foundation for proactive, self-aware factory operations, maintenance and innovation.
Sensor-equipped machines, inter-operable systems and reliable real-time computing are connecting machines across the smart factory. Product, raw materials, equipment, and control systems all have the potential to collect and share data. This data can be analysed in context and in real time to equip workers with actionable information.
Throughout the factory, end-to-end security at both hardware and software levels helps reduce vulnerabilities as more machines are connected. With more than 40 years of experience in both OT and IT solutions, Advantech is uniquely qualified to address the issues of OT-IT convergence which are fundamental to migration from yesterday’s ‘islands of automation’ to tomorrow’s smart factories.
A self-managing “Systems of Systems”
Secondly, the smart factory is based on multiple interconnected systems, each with a high level of flexibility, efficiency, and autonomy. Future factories will eventually become one large system comprising hundreds of smaller systems independently working toward the same goal. From production and maintenance to supply chain and security, each system and subsystem uses AI, machine vision, deep learning, and edge analytics to control everything on the factory floor.
This environment of machine-to-machine communication improves operational efficiencies and reduces unplanned downtimes. Production becomes so responsive to custom requests and material variations that the factory essentially operates at “economies of one” to compete with today’s economies of scale.
Self-monitoring equipment using sensors such as Advantech’s LoRaWAN smart vibration sensor can detect when quality could suffer due to degradation and then schedule its own service. Materials follow the most efficient path, and workloads are consolidated at all architecture layers to provide the flexibility to respond to fast-changing demands. Orchestration of applications and services across hardware enables data aggregation and control to provide new levels of performance.
Human-machine collaboration
A third aspect of the smart factory is its emphasis on machine-to-human collaborations, allowing employees to work more safely and empowering them to make faster, more educated, innovative responses to business needs. As smart factories reduce the number of humans on the floor, workers are helped by collaborative ‘co-bots’ on complex tasks, while repetitive, injurious work is handled by robots.
Workers use augmented reality and data visualisation to overlay information about production, maintenance and product status. A digital culture encourages the use of data for daily work, freeing employees to respond with greater creativity to resolve issues and support business success. A younger workforce is attracted through updated technology, safer work environments, and roles better suited to their generation.
Autonomous and self-adapting
Through autonomy and adaptability, the smart factory enables manufacturers to expand IIoT’s application and value to support changing business strategies.
The factory is becoming smarter and more autonomous over time, using data to optimise resource allocation and transform businesses. As more machines and systems are connected, manufacturing matures into an intelligent factory model in which OT and IT converge and strategically engage in business decisions.
AI and deep learning produce increasingly detailed, accurate and meaningful digital models of equipment and processes, enabling data-driven decision-making; and devices will grow more intelligent over time and respond to events more efficiently. Production controls become self-running, and new business approaches emerge.
Aided by the insights from data, the main manufacturing drivers have expanded from efficiency and product quality to also include production flexibility. Amid this continually evolving environment, the factory systems become increasingly intelligent and autonomous with systems beyond themselves.
Key trends shaping the future of manufacturing
In a smart factory environment, "data collection" refers to the process of gathering information from the manufacturing processes, equipment, and systems involved in production. Data collection in a smart factory is typically facilitated by various sensors, IoT devices, and automation systems that continuously monitor and record relevant information in real-time. This data is then aggregated, processed, and analysed using advanced analytics, machine learning algorithms, and other tools to gain insights, optimize processes, improve efficiency, and make data-driven decisions.
EdgeLink, a versatile IoT gateway software, is engineered to connect with over 200 edge devices and diverse platforms. It adeptly supports multiple protocols, unifying data sources, optimizing data processing, and publishing data to mainstream platforms or other automation systems through cellular, 4G, 5G, Wi-Fi networks, and VPN connections.
"Edge AI" and "Edge Computing" refer to the processing and analysis of data at or near the ‘edge’ of the source of data generation, rather than relying on centralized cloud computing resources. In the context of an intelligent or smart factory, edge computing and AI technologies are employed to perform data processing, analysis, and decision-making tasks directly within the factory environment. They play a crucial role in enabling the responsiveness required in modern manufacturing environments, contributing to the concept of Industry 4.0 and the evolution of smart factories.
MES (Manufacturing Execution System) and ERP (Enterprise Resource Planning) are software systems used to manage manufacturing operations and overall business processes, while OEE (Overall Equipment Effectiveness) is a performance metric used to assess the efficiency of equipment or processes. These concepts are all essential components of modern manufacturing management practices.
In the context of a smart factory, "Analytics AI" and "Machine Learning" (ML) are critical components that enable data-driven decision-making, optimization, and automation. They play crucial roles in leveraging the vast amount of data generated in a smart factory environment to drive insights, improve decision-making, optimize processes, and ultimately enhance productivity and profitability. They enable the transformation of data into actionable intelligence, empowering manufacturers to adapt quickly to changing conditions and stay competitive in today's fast-paced business environment.
Industrial connectivity refers to the network infrastructure and technologies used to connect various devices, systems, and components within an industrial environment. It enables seamless communication and data exchange between machines and other equipment, facilitating industrial processes. Industrial connectivity is a foundational element of Industry 4.0 and the concept of the IIoT.
Overall, industrial connectivity is essential for enabling automation, data-driven decision-making, and optimization in industrial environments. It forms the foundation for Industry 4.0 initiatives aimed at improving efficiency, productivity, and competitiveness in industrial sectors.
Advantech’s Role in Driving Smart Manufacturing
Software tools play a crucial role in the optimization of smart factories. These tools encompass a wide range of applications and platforms designed to support manufacturing planning, execution, monitoring, analysis, and optimization. Advantech’s WebAccess and other IoT software products provide a complete solution for device and data management to enable edge intelligence.
Advantech has implemented Industry 4.0 in its manufacturing centres, including a ‘situation room’ as the factory’s central brain where data is collected, analysed and visualised for real-time management. The equipment connectivity solution – consisting of an edge data gateway and distributed digital I/O – facilitates machine connections without replacing existing equipment while also collecting data. The industrial computer with Advantech software enables data transfer between production and management systems.
The process visualisation solution enables production monitoring, data integration with MES, and visualisation on the situation room dashboards. This allows production optimization and data-driven decision making. The Advantech WebAccess app gives push notifications of unexpected downtime, allowing immediate action to be taken.
The fundamentals of smart manufacturing aren’t slowing down. When combined together, they usher a new Industrial Internet of Things (IIoT) era where machine automation, hyper-agility, autonomous production, and data utilization deliver transform business processes.
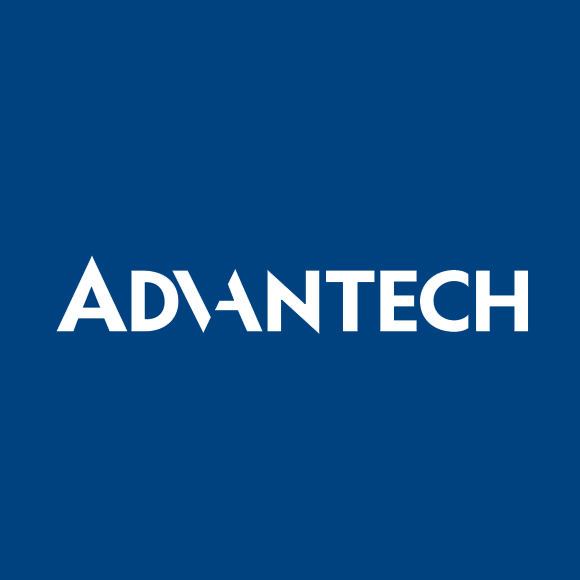